Have you ever concerned about how a combine harvester was in the past?
Are you curious about the “secrets” of how the combine harvesting machines work?
It may amaze you with a long history dating back hundreds of years ago and diverse stories of efforts made by inventors from different countries.
Now, let’s discover the journey of combine harvesters from the very first day till now,
how they have changed and contributed to easing the agriculture, leading to a better life for human beings.
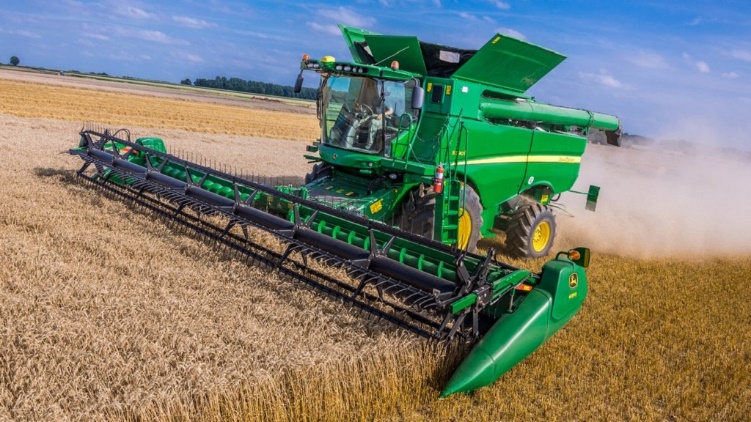
Before diving the history world of combine harvester, do you wonder what exactly is this kind of machine?
What is its function?
How does it work?
And what components do it make up the machine?
Well, an overview about combine harvesters is definitely a necessary kick-off information for all of you.
Ancient time of the very first combine harvester
Humans have always desired to conquer the nature and many efforts have been made to make this dream come true.
It was 75 after century that the basic wheat harvesting technology was launched.
With the determination to facilitate the farming, in his encyclopedia, Naturalis Historia,
the man known as Pliny the Elder – Roman Gaius Plinius Secundus (23–79 after century) described the device as a reaping device run by oxen to collect the wheat’s ears and plant stems’ barley.
The very first device consisted of a basic chassis that was attached with two wheels and a holding box above.
It also includes a row of sharp teeth at the front side to reap the ears. It was remarkable that they kept using this device for more than 300 years in spite of its wastefulness and straw destruction.
19th & 20th century: How a basic device has become modern combine harvester
1799 – First patented mechanical reaper
In 1799, Joseph Boyce – an English man – was honored to be granted the patent for the mechanical reaping inventor.
In terms of operation, the reaper could cut a with of relatively 0.6 m (2 ft) and grain would be laid to the lateral side.
In 1807, the first reaper using horse-pulling force came to use in agriculture as a devoted product of the designer Plucknett.
1811 – James Smith’s reaper implementation
In 1811, there was an introduction of a new reaper to the agricultural engineering by James Smith, Deanston (England).
This machine’s cutting capacity reached 0.405 ha (1 acre) / hour; however, the cutting disc demanded to sharpen fourfold.
Pushed by horses, the reaper had a cutting disc and a cone rotating around a horizontal shaft that are connected by had a vertical shaft.
Although there was an unsteadiness in using the machine for harvesting materials, they still considered this invention as a breakthrough in farming techniques.
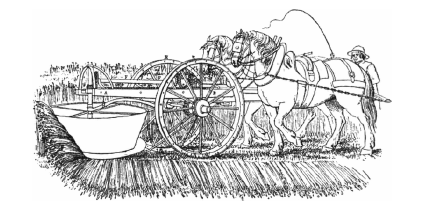
1826 – Reaping machine with scissors principle
Continuously, there was a next-gen invention for better working capacity. In 1826, A Scotist – Reverend Patrick Bell had a new design for the reaping machine.
With regard to operation, the reaper utilized the similar scissors principle of plant cutting which is still used on a daily basis.
In addition, the machine was run by using horses.
There were just several machines of Bell that could be found in the United States then.
1831 – Pulled reaper by Cyrus McCormick
In 1831, Cyrus McCormick said that he had spent 18 months developing a pulled reaper that could cut and bring the materials sidewards, as in his first public displays.
The revolving reel enabled the reaper to sweep the plants onto a pallet, then a man who went along with the reaper would rake materials into piles.
As a consequence, on June 21, 1834, McCormick received a patent for the reaper that he spent all his heart on.
A second patent was granted for McCormick for his new version reaper in 1935.
With reference to machine’s improvements, it is notable about the serrated edge of a straight and vibrating cutter played a role in cutting the grain.
The cutter was functioned by a crank, with the plants being held by fingers.
Without the difference of the angle of the teeth which was reversed for every alternate tooth, the blade’s serration resembled a sickle. By 1847, Cyrus
McCormick launched the mass production of his improved reaper in a factory in Chicago. McCormick’s “Virginia Reaper” started manufacturing in England in 1855.

1835 – First Combine Harvester by Hiram Moore
In 1835, with the capability of reaping, threshing, and winnowing cereal grains,
the first combine harvester of the American investor Hiram Moore was built and brought him a patent for this breakthrough.
This combine harvester was pulled by 20 horses that were totally controlled by man.
The machine was 5.2 m (17 ft) long and cut of 4.57 m (15 ft) wide.
1841 – First Threshing Machine powered by steam
In 1841, Alexander Dean – an manufacturer of UK created the first threshing machine run by steam.
At the same time, a threshing machine powered by a disc engine was unveiled by Ransomes and Co. in Liverpool.
This machine could be pushed by horses or be propelled itself using a pitched chain passing over a pulley on the main axle.
In 1842, Messrs. Tuxford produced a similar thresher in Boston.
It was shown that the engine and machine were both attached in a single frame.
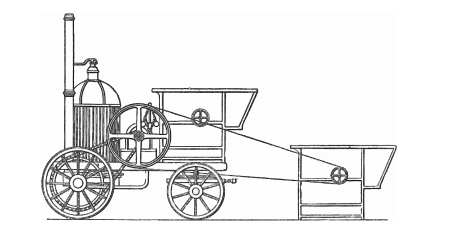
1857 – John F.Appleby (Wisconsin) invented the twine binder
In 1857, the inventor John F. Appleby (Wisconsin) successfully made the twine binder and got a good reputation for this machine.
1860 – Combine Harvesters in the US
In 1860, they built combine harvesters in the United States. The machine could cut several meters wide; they were drawn by up to 30 horses.
1872 – First reaper-binder machine built by William Deering
The inventors were satisfied with what had been made for the development of agriculture.
The fact is that in 1872, the first reaper-binder was made by William Deering, owner of Chicago-based Deering Co.
The reaper-binder was capable of cutting small cereal plants and pile them into small bundles.
Then, these bundles are made into conical teepees to facilitate drying process before threshing.
1879 – Stationary Threshing Machines
Stationary threshing machines were launched at the 1879 Kilburn Show (England).
The worker standing on a platform laterally could run the machine directly.
The machine was designated regarding levels of strength.
This opened a new kind of equipment for the better choice for harvesting.
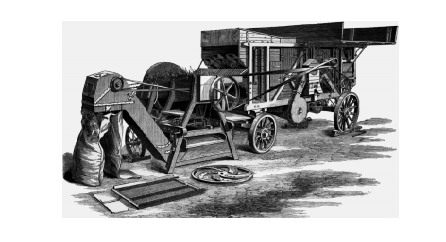
1890 to 1910 – Application of horse-drawn combines
By 1890, Best, Houser and Haines, and Young and Berry were some of the companies that participated in producing horse-drawn combines.
To operate properly, the machine required a team of 10 members including driver, separator man, header tender, sack jig, and sewers.
The combines were bigger and wider (30 ft) than the previous version.
The crew team included up to 10 people.
Though the machines were updated, there were still some problems.
For example, people could be injured or fires could be ignited since coals could be fell out of the boiler heaters when tipping in places like hillsides.
In 1891, a tilting mechanism to control the combine thresher’s level came to real-life by Holt Manufacturing Company.
This can slope up to 30° and improve the balance.
When integrating this mechanism, the combines would be called hillside combines.
With the ability to enhance harvesting work safety, fire hazard control, and repair cost prevention,
this was worth considering a leading technical breakthrough.
From 1911 – Using combustion engines in the threshing machine
In 1911, the Holt Manufacturing established the Holt Caterpillar Company after buying the facility of a farm implement maker.
Then the Holt Company developed the first combustion engines that powered threshing machines.
1925 – Tractor-pulled combines come into play, replacing horse-drawn combines
In 1925, The International Harvester made the first tractor-pulled combine.
Conveniently, If the farmers wish, they could also replace the horse-drawn combines’ horse hitch with a tractor one to have much more efficient machines.
1939 – First self-propelled combine with a combustion engine
In 1939, the first self-propelled combine with a combustion engine was developed by the company Massey Harris and named the Model 21. In comparison with the horse-pulled combine, it was quite smaller.
The combine can reach the efficiency of harvesting 12 ha (30 acres) / day. This model was regarded as an important point in the history of combine development history.
1927 to 1940 – First reaper-thresher-binder machine using power take-off drive
In 1927, Krupp company invented the first reaper-binder with a power take-off drive in Germany.
Then, it was till 1940 that the German manufacturer CLAAS made the first reaper-thresher-binder. A tractor using a power take-off drive, playing a role in driving the machine.
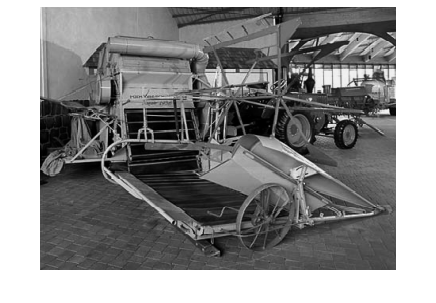
1951 – MD-1 – First self-propelled combine harvester
The agricultural devices continued to be more and more diverse. In 1951, MD-1 – the first self-propelled combine harvester was introduced by Fahr company from Germany.
Two years later, CLAAS debuted a self-propelled combine, named Herkules whose capacity was cutting up to 5 metric tons of wheat / day.
1960 – Continuous updates for the self-propelled combine harvesters
The self-propelled combine harvesters got the more spreading and evolving technology which enable its number to exceed that of the tractor-drawn machines in 1960.
Self-propelled combines were powered by not only a single operator but also their engine for both propulsion and process of harvesting.
Simultaneously, the designer equipped the engines with self-cleaning rotary screens to minimize the engine’s over-heating as a result of the chaff and dust blocking the engine radiator and the cooling airflow as well.
Moreover, some new combine harvesters are integated with diesel engines.
1977 – Introduction of axial-flow rotary combines
Then, engineers concentrated on improving the threshing unit, straw walkers, and cleaning shoe separation processes.
Also, the width of the headers was simultaneously increased with the cutting speed.
The introduction of axial-flow rotary combines in 1977
by International Harvester represented one of the most significant technical advances in modern combine development
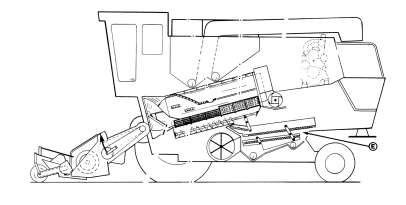
Current development of the combine harvesters
Nowadays, combine harvesters are much more efficient than before and they can cut swaths of more than 12 m (39 ft).
Not only are the machines efficient but they also have global positioning system (GPS) devices to follow their path and evaluate grain production.
Combines are equipped with air conditioning, heaters, cushioned seats, and adjustable steering wheel height to ease the combine operator.
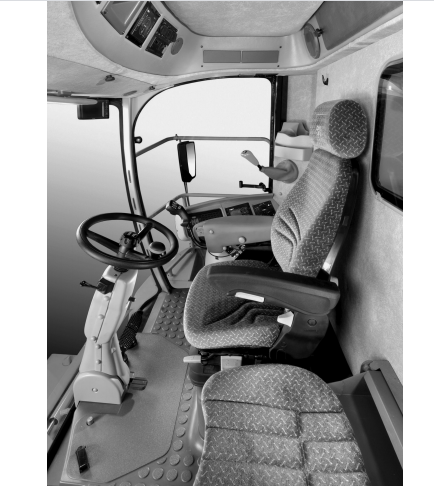
Summary of combine harvester development history
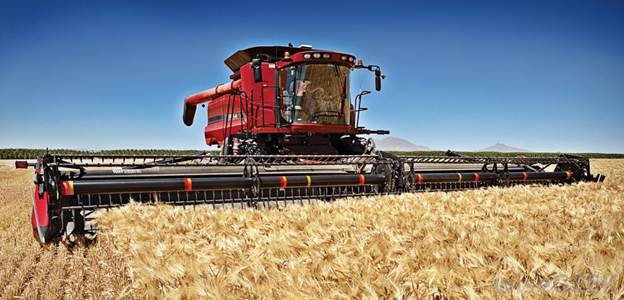
From the basic devices to modern machines, all of the efforts have been made to facilitate agriculture.
Through the history of combine harvesters, it is crucial to withdraw the key points about the technical evolution.
In particular, the number of operators for a machine has considerably decreased and the efficiency has been boosted incredibly with the grain quality preserved.
The clear production’s improvements together with combine harvesting techniques have led to a reasonable price for products.
Thanks to the new technology, it brings more profits and saves time for the workers that now can do multiple tasks flexibly.
At the same time, the workers can have a chance to spend the saved times on other activities, heading to a better life.
There you are, every detail about the history of development of combine harvesters are illustrated in our above article.
After having a broad picture about this equipment’s development, it is high time to learn more about how a combine harvester work.
Link out and prosper!