Fully aware of your knowledge-seeking demand, we will share and uncover everything about combine harvesters in this following article, how the agricultural equipment is classified and what its specifications are.
Briefly speaking, based on the working mechanism, combine harvesters are divided into two (02) main types:
(1) the “controlled” combine harvesters
(2) the “self-propelled” combine harvesters.
In the present market, the latter type of combines is more dominant and widely used.
Keep on reading and exploring more about combine harvesters with us!
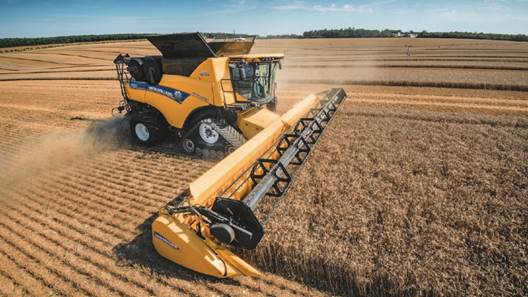
If you are a beginner about the concept, we highly recommend you get yourself more familiar with combine harvesters first.
However, if you have heard of combine harvesters before and would like to explore deeper about the machine, feel free to keep on reading.
Controlled Combine Harvesters
About controlled combine harvesters, they are also known as tractor-pull combines, or tractor combines, or pull-type harvesting combines.
Regarding operation, a farm tractor supplies pulling force for the machine, and simultaneously thrashing, cutting, separating and cleaning can also be powered by the power take-off shaft of the tractor.
They are still being in use for various different demands in multiple places.
Just with a small difference in working principle, another kind of controlled combine harvesters was born.
This type of machine is powered by a tractor but they need another engine that is mounted on the combine harvesters.
The separate engine helps run cutting, thrashing, and other necessary tasks.
Due to their inconvenience, these combines are not widely available.
Self-propelled Combine Harvesters
Main types of self-propelled combine harvesters
Self-propelled combine harvesters run by themselves with an engine attached above.
The engine power plays two roles: driving the machine and harvesting related operations.
There are two common types of combine harvesters:
(1) conventional combine harvester
(2) rotary (axial-flow) combine harvesters.
While the tangential threshing system and straw walkers are the core compartments of a conventional combine, a rotary combine is defined by its axial-flow threshing system.
Though rotary combines are still widely used, conventional combine harvesters have seen their growing quantity on the market.
So, how well do you know about conventional combine harvesters?
Conventional Combine Harvesters
Basic parts of a conventional combine harvester
The main parts of a conventional combine harvester are as follows:
- Chassis with installation of engine and fuel tank, ground power train, wheels, and steering mechanism
- Combine Header
- Threshing–separating system
- Separating straw walkers
- Cleaning system
- Conveying, storage, and discharge system
- Cab with seat, driving control, process control console and instrumentation, and climate control system
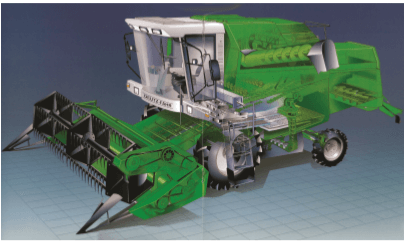
Part Functions and Material Flow
The material is cut and gathered by the combine header; then the feeder throat carries it up through a chain-and-flight elevator.
Next, the material is fed into the threshing unit/ system.
With regard to working processes and power demand, the most important component is the combine threshing unit/system.
In particular, a tangential threshing unit consists of a cylinder (a rotary threshing drum) and a concave with an adjustable position using manual or automatic mode.
It is noted that the cylinder needs to have a continuously-adjustable speed for different crops’ threshing processes.
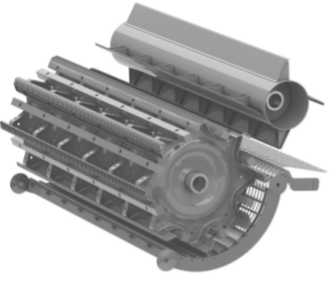
Regarding tangential threshing units, a narrow space bounded by rotational rasp bars of the cylinder and the concave surface is where the material goes through.
The effect of the threshing process largely results from the strike of the rasp bars or other active elements on material.
Specifically, the friction created by the working of the rasp bars and combine concave brings about the threshing processes.
The cylinder’s adjustable rotation against the concave plays a role in controlling the grooved rasp bars and concave bars’ separating the grain and chaff from the straw.
Then the mixture is separated and fell onto the cleaning shoe.
The dis-awing plates equipped for the concave help remove the awn thanks to the supplementary friction with the crop materials moved.
The fact that different crops have varied stem and grain sizes, and different mechanical and aerodynamic properties require the concave segments to be exchangeable.
Then, the straw walkers recover the grains that are threshed but unseparated and exit in the threshing unit.
A small fraction of unthreshed ears or panicles is conveyed back into the threshing unit for rethreshing.
The clean grains are conveyed with a paddle elevator or auger for temporary storage in the combine tank.
A flapping auger discharges the grain from the tank into a trailer for later processing or storage.
For better efficiency, a portion of the unthreshed ears or panicles is brought back for the rethreshing process.
A paddle elevator or auger conveys the clean grains to the combine tank for the temporary storage. Then, the grain is discharged from the tank into a trailer to be stored or processed later.
The changes to boost the throughput capacity of conventional combines
Below are some configurations that allow for higher throughput capacity of combine harvesters:
- Increase tangential threshing unit’s width from 0.7 to 1.7 m or more.
- Enlarge concave wrap angle from 85°–90° to 110°–120° up to 145°.
- Increase diameter of cylinder up to 800 mm and keep wrap angle unchanged.
- Reduce concave rods’ size from 8–9 mm to 3.5–4.5 mm.
A proportion of 90% grain separation can be achieved under certain favourable conditions, while this number in a tangential threshing unit at nominal feedrates is 80%.
Furthermore, it is common to use a series of tangential threshing units together with around two cylinder-concave units to achieve better throughput capacity.
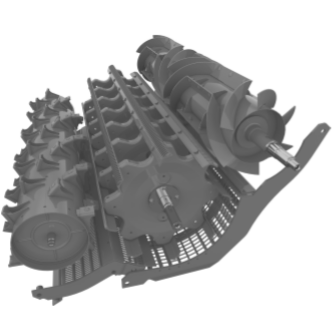
The threshing-separating area in a 2-cylinder threshing system gets an increase of 65%-75%;
however, the straw walkers have a 20%-25% decrease in the separating area.
It is clear that the capacity of a conventional combine with two cylinders outnumbers that of a combine harvester with one cylinder, about 15%-25%.
An auxiliary system has been attached on top of the straw walkers to enhance the efficiency of separation.
An example for illustration is a separation intensifier system which is composed of a rotary drum.
To increase grain separation, during the drum rotation, the fingers protruding to the maximum length at the bottom of the drum split the mat of straw.
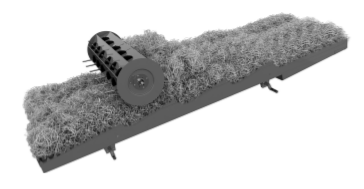
The variation for drum rotation frequently ranges from 100 to 200 rpm.
Through the change in fingers’ inclination angle, the material conveyance becomes aggressive, and thus prevents entanglement problems.
Because of a decrease of separation intensity compared to that of a threshing unit, straw walkers lessen the throughput capacity of a combine.
The grain separation becomes the most intensive when the straw falls down form a step onto the next section.
Being essential for not only conventional but also for rotary combines, the cleaning shoe includes a receiving part, a chaffer, a sieve, a grain pan, and a blower system.
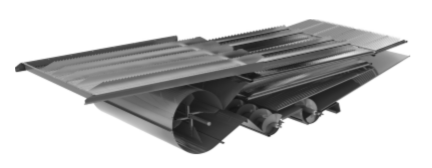
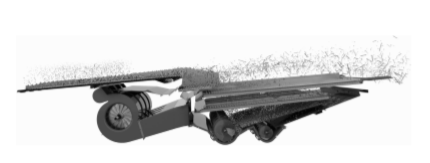
Equipped with an underair blast, the grain pan functions as a conveyor and a precleaner.
In addition, the conventional fingers placed at the end of the grain pan is where the material falls down on a second step.
During this process, the material which has been stratified along the grain pan shall be conveyed to a chaffer.
The straw falls out the rear of the combine after reaching the end of the straw walkers.
Then, it can be used for livestock bedding or spread at the back of the combine.
A system of metal shields which guides the chaff and chopped straw have a modifiable angle of orientation for the targeted width of spreading.
The metal shields are properly positioned for the crosswinds’ compensation.
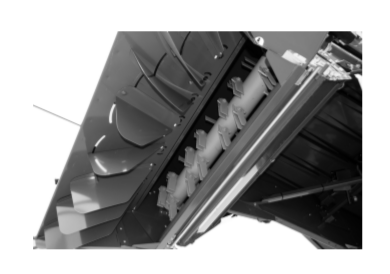
The design of harvester combines mainly aims to reach the balance of the machine throughput capacity and the efficiency of processes: crop gathering, threshing, separating, and cleaning.
This task meets difficulty when crop types, harvesting conditions, and machine operations and controls are divergent.
Nowadays, there is a downward trend in using the conventional combines because of the comparatively limited material throughput (up to 9 kg/s),
depending on the size of threshing-separating and straw walker systems. It is clear that this separating system has a limited performance.
Therefore, there has been an introduction of a new axial-flow threshing system for better capacity.
Rotary Combine Harvesters
The first rotary combine – model TR70 Twin-Rotor combine with two longitudinally mounted axial threshing and separating rotors was unveiled by New Holland in 1975.
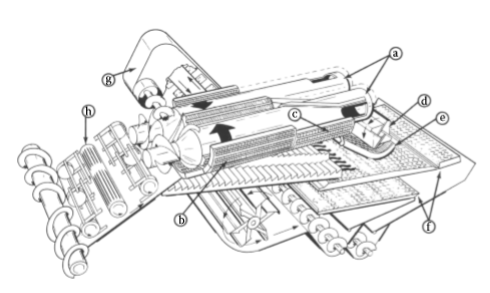
Below is a combine harvester with a longitudinal cutaway of a rotary (Case IH Axial-Flow AFX Series).
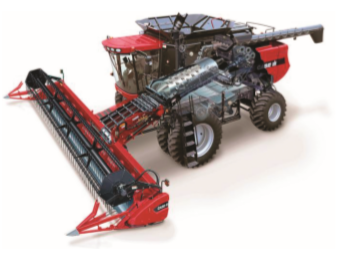
A bigger, rotary threshing-separating system has been used to replace the tangential threshing module and straw walkers.
About the flow of crop, the material can move smoothly and continuously on a helical path bounded by the rotor and a system of concave and cage with 360° wrapping.
There are three main areas in AFX axial-flow threshing unit: feeding, threshing, and separating.
Feeding zone functions as a mouth to draw large amount of material into the threshing space.
The modifiable vanes in the concentric cage of the rotor help direct the flow of crop.
Advantages and disadvantages of rotary threshing system
The rotary combines bring us the following advantages:
- Minimize damage to fragile grains.
- Adapt to all crop processing better.
- Decrease grain loss level.
- Lower volumetric feedrate’s variation sensitivity.
- Diminish fluctuation in grain loss with rising MOG/grain mass ratio.
- Extend efficiency at threshing crops
- Need fewer adjustments, lessen vibration level, and reduce maintenance
However, the rotary combines also have some disadvantages, which are the increase in power requirement and cleaning shoe system overcharging that stems from a higher degree of MOG fragmentation and separation when material passes through the concave and grates.
Moreover, no preservation of the straw quality through the rotary combines makes it hard to bale or remove it from the ground later.
Subsequently, different combine manufacturers applied different rotary combine techniques.
Following the design of Allis Chalmers producer, the Gleaner combines have the rotary threshing or separating with cross-mounting feature.
This intends to achieve a tangential angle when material is drawn into the rotor’s left end.
The after-threshing chaff separation efficiency is now more enhanced with a pair of rollers stimulating the material’s moving process to the cleaning shoe across from the airstream blown by a fan.
For better performance of threshing-separating system, a tangential threshing system is combined with an axial threshing-separating system, creating a hybrid threshing-separating system.
Below is this arrangement in a modern CLAAS Lexion combine.
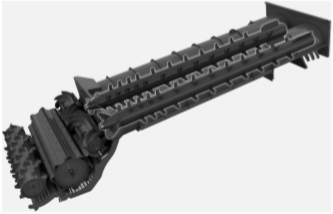
Source: Combine Harvesters, Theory, Modeling and Design, 2016
Jonh Deere’s C-Series combines utilize the same threshing system.
The material is inhaled into a large tangential threshing cylinder.
The material goes through a large tangential cylinder, and then an intermediate beater which helps minimize material wrapping and slugging.
After that, the material is processed by an overshot beater and pushed into counter-rotating tine separators.
After separation process, the grain, chaff, and some fragmented straw are taken to the cleaning shoe using pair of rollers, assembly of augers, or a backward inclined floor.
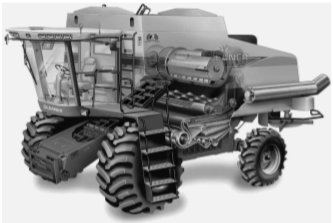
Though there are several different types of combines, they share some similar features in power system.
For a detailed sharing, you are recommended to take a look at the power system of combine harvesters
Conclusion
The more complex the harvesting demand gets, the more diverse the types of combine harvesters become.
It is evident that the self-propelled combine harvesters are prominent in grain harvesting with two main kinds of mechanism: Conventional combine harvesters and Rotary combine harvesters.
With different conditions, the farmers and workers use the appropriate ones for their crops.
Harvesting machines have made a huge contribution to the development of modern agriculture and enhanced people’s lives.
Hopefully, our information about the classification of combine harvesters and their specifications is useful to you!
You can explore our site more to learn about the working processes inside a combine harvester.
Link out and prosper!