Combine harvester has become a common name for all farmers and workers in the agricultural field.
They come in various types and designs for particular purposes and crop conditions.
Whatever the type is,
all combine harvesters share the same missions:
- Facilitating the harvesting process
- Promoting agricultural mechanization, and s
- Saving labor and time for farmers.
As a result of development, the combine harvester’s design has been continuously upgraded and become increasingly sophisticated.
So, how are components arranged in a combine harvester? In other words, how does a combine harvester work?
In this article, we are going to discover the working processes of a combine harvester and the suggestions for common problems of this machine.
Overview of Combine Harvesters
A combine harvester is defined as a multi-functional machine that executes the main tasks:
crop cutting and gathering, grain threshing and separating, and grain cleaning and collecting.
Behind this rhythmic coordination, there is an excellent arrangement of components that function well with each other, namely combine header, feeder house, thresher, separator, cleaning fan, straw chopper, and so forth.
According to Case IH harvester marketing manager, Kelly Kravig, a combine is a sophisticated harvesting machine,
which is shown by its ability to do everything simultaneously.
He emphasizes that the combine harvester can take in the crops, thresh the grain, separate it, and disperse the residue successively without any disruptions, reaching the optimum performance.
Main Processes of Combine Harvesters
Combine Harvesters Take in the Crops
Header and feeder houses function as the first contact point between the crops and the machine.
The crops are cut and gathered by the combine header. Then, the material is carried up the feeder throat by an elevator.
Interchangeable combine headers are utilized to cut different crops under different conditions.
A rotating wheel, also known as a reel, rolls the crops into the cutter.
The combine performance can be affected by small grain and soybean platforms.
It should be noticed that the reel misadjustment on crops can result in bunch-feeding, which increases the grain damage and loss out the back of the machine.
Feeder houses are not just conveyors between the header and the combine but in charge of more functions.
In particular, the feeder house drum and conveyor chain press down the input crops and prepare them for further processing.
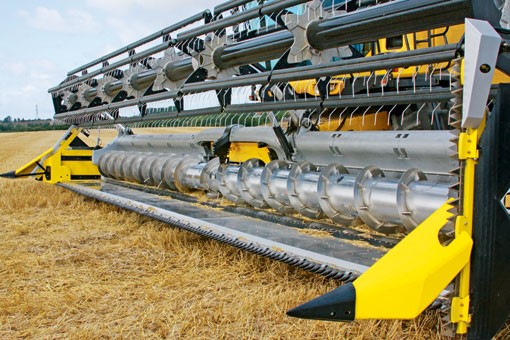
Combine Harvesters Thresh the Crops
Afterward, the material passes through threshing process.
The threshing unit of a combine harvester plays a role in beating the crops and shaking the grain from their stalks.
The core working principle is the effect of rubbing action between the threshing lobes or rasp bars, and the material.
The rubbing action’s effectiveness depends on the rotor/cylinder speed and the clearance between the threshing drum and the surface of the concave.
If the speed is too fast, the grain gets cracked.
Meanwhile, the grain can get crushed if the material flow is stuck.
Besides, the unthreshed grain from the threshing drum is further threshed when passing through the straw walkers.
Here, the straw walkers move the straw toward the back of the machine while allowing the remained grain to fall down through the shaking screen.
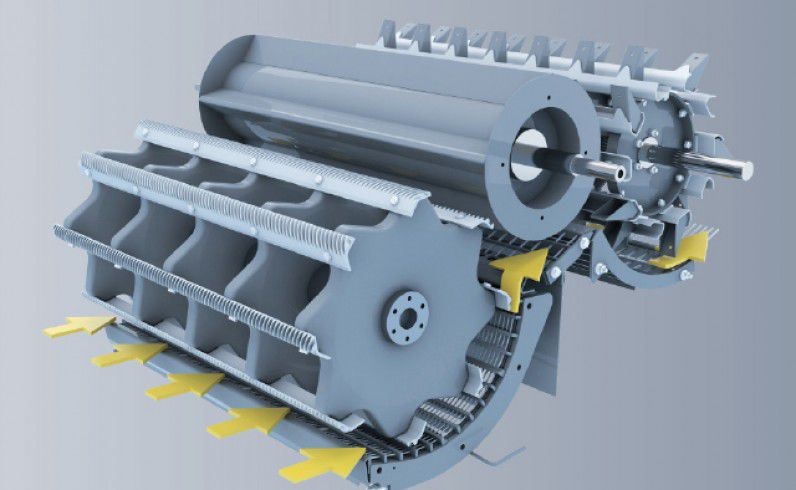
Combine Harvesters Separate the Crops
After the two stages as mentioned earlier, the material goes through the separating process.
The combine’s separating unit is composed of cleaning fan, upper sieve, and lower sieve.
The sieves are designed with the openings for the grain to pass through.
However, together with grain, other material containing straw pieces, chaff, dust particles, and other impurities also fall through these openings.
Therefore, the purpose of this process is to blow all the material-other-than-grain (MOG), using a strong fan.
Jeff Gray, the product coordinator for Class Laxion, says that some operators remove the upper sieve and let the lower sieve do all cleaning.
In his opinion, these people think that it will help prevent the grain from flying toward the back.
However, he comments that this action can result in the overload of the bottom sieve and the tailings return, and simultaneously emphasizes that the upper sieve should do the main task.
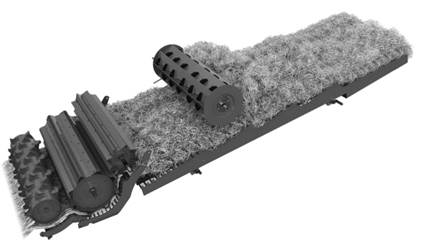
Combine Harvester Manages Crop Residue
In fact, modern, huge combine harvesters release a higher flow of MOG on a small-width swath relative to header width.
In the cleaning and collecting unit of combine harvesters, crop residue shall be managed.
The losses of weed and grain are accumulated behind the combine.
The vegetative material is processed more intensively by the axial-flow harvesters compared to conventional combines.
If the residues after harvesting are discharged behind the combine and are shallowly penetrated into the soil, the organic matter accumulation in the upper soil layers becomes an issue because the decomposition and conversion to humus are insufficient.
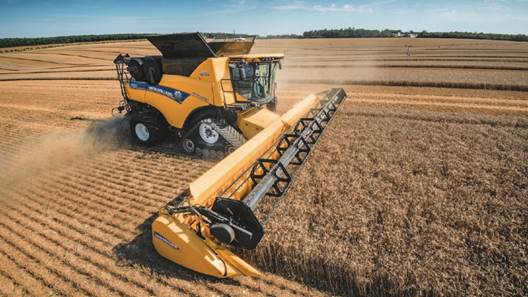
Cereal crop residues such as straw, husk, and chaff are considered as essential organic fertilizers, organic materials for bedding and forage in the livestock industry,
and for energy supply from direct burning and biogas production.
If collection is not implemented, post-harvesting crop residue management will be crucial for any successive seeding process, especially a reduced or no-tillage process.
Soil harrowing often gathers the straw and corn husks in bunches which may not be properly assimilated into the soil.
Therefore, if all these residual MOG components are not previously chopped and evenly spread, they cannot disintegrate into the soil to provide useful nutrients.
Uniform crop residue distribution helps improve soil erosion protection and stand establishment.
They suppose that single-pass harrowing or cultivating of the soil is not at as good as no-tillage because weed seeds are assimilating into the soil and loosen the stubble.
As a result, failed crop residue management has a negative impact on the seeding process efficiency, leading to uneven distribution, hair-pinning, plugging, lack of soil aeration and drying,
and ultimately, low and non-uniform germination and the emergence of the next crop seeds.
Plants that outcrop later than the surrounding plants may be overwhelmed during their development, reducing the crop growth due to plant emergence delay.
Nowadays, modern combine harvesters are built with chopping-spreading equipment that chops and spreads the straw, husks, and chaff uniformly across the header cutting width.
All of these operations are run by a complicated power system of combine harvesters,
so you can go through our article for further understanding of the working process and power system as well.
Basic Repairs for Common Problems in Combine Harvesters
Feeding
Feeding is an essential section of the rotor combines.
The feeder house throat needs to be narrow enough to prevent the slats’ ends from catching the crop.
The feeder house would move the crop along until the feed chain plugs.
Additionally, the stripper bar is required to reach this edge, and fairing extensions are demanded to complete this process.
The operator should make sure that the auger can touch the stripper.
The earlier augers are black, so they would bow a lot if the combine is parked in the sun.
The auger sometimes loads the crop along and throws it onto the pickup or the real.
The solution is adding a second stripper on the bottom of the header, enabling the auger to run on both strips.
Besides, the operator needs to check the flighting.
A knurled finish will be created by the forming tool in the middle of the flighting’s surface.
From this, the crop can be grabbed and carried around.
Feeding characteristics of the combines can also be improved by changing the time of the fingers.
When setting up the feeder chain, it should be noticed that the top one turns at a faster speed than the bottom one.
Furthermore, if the unit is equipped with a stone trap, it needs to open not too quickly.
Threshing
A piece of metal positioned on the bottom left corner of the concave helps direct the material coming out of the chain and into the concave.
It would tend to be loose, so the operator should make sure the bolts are tightened correctly.
While the concave is set from the back, pivots are in the front.
Another section, pivoting in the middle, is modified from the front for a positive setting that is continuously tighter with the cop passing the concave.
Meanwhile, if the front is tighter than the middle, a lot of unthreshed material will be put into the grain tank.
If operators find the grain on the ground right behind the straw spreader,
they should add extra reverse bars in order to back up the material in the cage.
Nevertheless, this might slow capacity.
Separating
As discussed above, the separating process starts when the shaking screen.
The cylinder commonly runs really fast without cracking disruptions.
However, there can be some modifications.
The straw is sometimes chopped too much and it moves through the cage, creating the overload for the trough below the cage.
In this case, the operator can decelerate the cylinder or eliminate six inches off each cage sweep.
Normally, the later models are not equipped with a cage sweep, relying on the contour of the openings instead.
If the operators have trouble building up the material between the underside of the hopper and the cage,
they should change the cylinder-rotor’s speed.
Cleaning
Accelerator rolls are regarded as an important part of the combine.
In their proper working process, the material is taken out from the trough underneath the cage and driven down.
That ensures most of the chaff is swept away before hitting the shoe.
If the accelerator rolls get worn or damaged, the trough on top will plug.
Simultaneously, the cage sweep also plugs, reducing the separation area, and the combines begin losing grain out the chute.
In addition, worn accelerators do not throw the mixture of grain and chaff fast enough through the blast of air.
When this mixture decelerates, the air is too strong, and grain is blown out.
In this case, the producers should slow down the air, but this action creates losses over the shoe.
Several combines have the upper lip which is pointed down, and this makes the material from the accelerator is blown back on the shoe.
Gradually, there will be the appearance of the wear on the inside of the machine in which it flows out of the air channels.
Noticeably, it should point back rather than down.
Furthermore, what to concern is the two cut-off points in the fan housing.
In fact, they should be totally straight and parallel to the fan.
Conclusion
Combine harvesters have been an indispensable machine for farmers all around the world.
The agricultural mechanization trend still continues and pays the way for the introduction of more and more multi-functional and upgraded implements and machinery.
In this article, we have discussed how a combine harvester works and have learned about working processes inside this machine.
Besides, the article also brings the readers some basic notes for consideration about the basic problems of combine harvesters.
We hope the information may address your concerns and be helpful to your business.
Thank you for reading and see you at our other articles!
Link out and prosper!