Straw walkers are vital components of separating unit in the combine harvesters. Separating process comes right after the threshing procedure, with the grain mixture being discharged onto the straw walkers. This grain mixture is called the residual grain, which contains straw, chaff, mineral components and even insects. This residual part shall be handled by the straw walkers. Through their operation, grain loss is recovered for re-threshing, and straw is separated from the MOG mixture and discharged toward the combine rear onto the soil surface. Detailed information about the construction of straw walkers, and their working process shall be discussed in the following article.
You can find more general information about combine harvesters through our articles.
Function of separating unit
Most grain losses and MOG resulting from the threshing unit are transferred to the straw walkers. Depending on the types and properties of the material, as well as the working mechanism of the threshing unit, the grain mixture discharged by a threshing unit onto the straw walkers may include long straw (20%-50%), short straw (10%-35%), chaff (10%-15%), together with weed components and grain losses of the threshing unit, as well as other parts of vegetal origin, small mineral components and insects.
The straw walkers of conventional combine harvesters have the following roles:
- Recovering grain losses of the threshing unit through separation.
- Delivering the recovered grains to the cleaning unit.
- Separating the straw from the MOG mixture.
- Delivering the straw toward the combine rear for field discharging.
The most challenging job of straw walkers is to handle the residual grains (free or unthreshed) from their straw. As a matter of fact, the capacity of grain separation performed by the straw walkers determines the total material feedrate of combine harvesters. Straw walker operation is dependent upon the combine inclinations (flow uniformity), MOG feedrate, and moisture content. Therefore, to support straw walkers’ performance and thus increase the efficiency of grain separation, a straw-mat agitator (or ruffling drum) is installed on top of the straw walkers to aerate the straw as it flows along and to allow the free discharge of grain for efficient separation.
A great advantage of utilizing straw walkers is the ability to maintain grain quality and straw size and condition, when compared with the process operated by an axial threshing unit. In the case of an axial threshing unit, its operation goes on without the use of straw walkers. At the rear of the combine harvesters, there is usually a chopper-spreader installed to grab the straw while in motion from straw walkers, chop it and spread evenly over the farm. The debris from the cleaning sieve reaches the chopper-spreader as well, and together forms a mixture with the chopped straw, and follows the same path before landing on the soil surface.
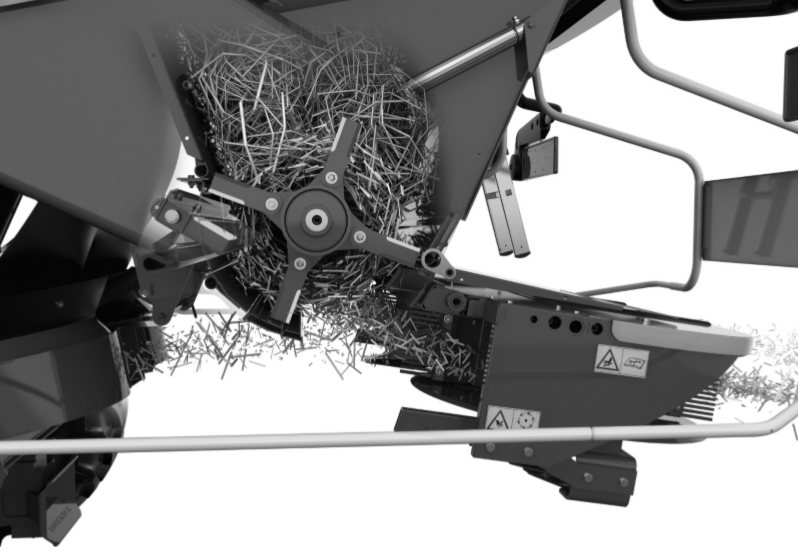
Construction of Straw Walker
For conventional combine harvesters, the straw walkers can be divided based on the following factors:
- Construction shape: referring to the straw walkers with oscillating platform, shakers, sliding screens and grain separation-intensifying devices (retractable finger drum, oscillating stellate discs, etc.)
- Motion type: referring to the straw walkers with uniform motion or oscillatory motion.
- Motion phase: referring to synchronous or independent straw walkers.
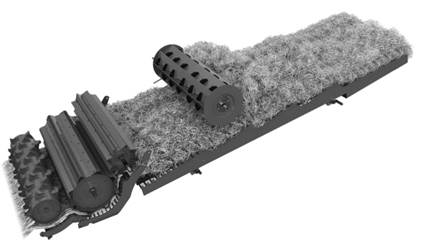
For modern conventional combine harvesters, the machines may be equipped with four to even seven independent straw walkers (or shakers, shoes), which are mounted on a crank axle at the front, and motion-driving crankshaft at the rear of the combine harvesters. Each straw walker is built upon four to six shaking units whose screens are inclined to form a series of cascades (steps) that intensify the grain separation.
Additionally, each cascade’s wall is a screen as well. Each straw walker may contain 4-11 cascades, and 5-12 screens (or sieves) to recover grain efficiently from the straw mat. The sidewalls of each straw walker contain a linear sawtooth profile which, together with the cascades, push the straw rearward to be pumped out directly on the farm, or to be chopped and spread all over the field.
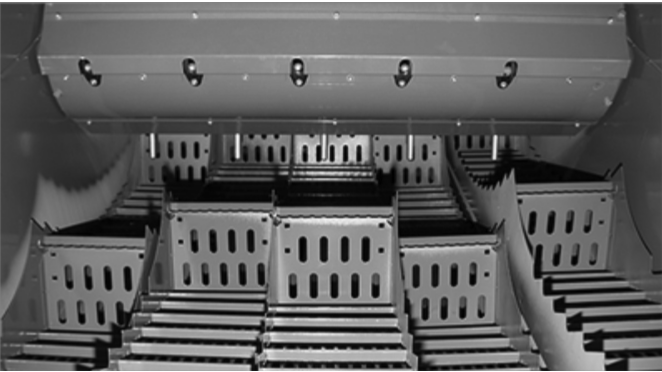
The straw walkers perform their function at three different areas: feeding, separation, and discharge areas. Each straw walker induces a plane-parallel motion with a vertical plane, in which the trajectory of every point results from a translational motion with an arbitrarily selected pole, around which rotational motion occurs due to the driving rotation of the crankshaft. The straw released by straw walkers then goes through chopping and spreading system as the final process.
For independent motion shakers of straw walkers, the location of each crack on the crankshaft and axle forms an angular offset whose value relies on the number of shakers. For four, three and six shakers, the angular offset is 90°, 120°, and 60°, respectively. For five shakers, the angular offset value is 72°. The independent straw walkers are very efficient when short straws and fine chaff make up a big proportion of the MOG mixture.
For synchronous motion straw walkers, they are classified into two groups with opposed motion flow: a group of odd-position shakers of 1, 3 and 5, and another group of even-position shakers of 2, 4 and 6. Under such circumstances, the cranks of the crankshaft and crank axle have a 180° angular offset. These straw walkers are ideal when the MOG mixture contains mainly a big fraction of long straws.
The typical measures of a shaker are width of 230-355 mm (9-14 inches), length of 2.75-4.5 m (108-177 inches), together with cranks length of 40-60 mm (1.58-2.375 inches). The crankshaft rotation can be adjusted between 180 and 270 rpm. Depending on the type and structure of the threshing unit, as well as the crop properties, the load of straw walkers can vary between 1.3 and 2 kg/s/m feedrate.
Conclusion
Through the separating process, most grain losses and MOG mixture discharged from the threshing unit are recovered and handled more efficiently. Straw walkers, the heart of combine harvester’s separating unit, are responsible for the handling of residual grain. Since not all grains are separated by the threshing system, straw walkers are installed in the combine harvesters to recover the rest of the threshed grains via the assistance of their oscillatory movement. The straw walkers are located above the sieves, and have holes in them. The remaining grain attached to the straw shall be shaken off and fall onto the top sieve.
When the straw reaches the end of the straw walkers, it is discharged through the rear of the combine harvesters. After that, it is baled for cattle bedding or spread by the straw spreaders located at the back of the combine harvesters. Most modern combines are equipped with a straw spreader to regulate the material discharge. With the help of straw walkers, grain loss is significantly reduced, and the grain quality is also well-preserved. In short, the performance of straw walkers can define the overall operating efficiency of the combine harvesters.
After going through the separating unit of combine harvesters, the materials are transported into the final stage – the cleaning and collecting section.
Link out and prosper!
https://books.google.com.vn/books/about/Combine_Harvesters.html?id=yn5jCgAAQBAJ