Having a broken cast iron machine or component is a true nightmare, as the cost for replacement or repairing is very high. But do you know that with stick welding, you can fix some minor defects relating to broken cast components all by yourself?
Let’s find out about stick welding cast iron[1] in this article. We will walk through the following content:
- When should we apply stick welding cast iron?
- Selecting the most suitable rod for stick welding cast iron.
- Some discussion on the techniques and overall process of stick welding cast iron.
Alright boys! Let’s go!

When Should We Use Stick Welding Cast Iron?
Stick Welding[2] is a desirable option for many DIY welders to fix and repair some broken cast iron pieces.
The welding process is very simple and can run with various electrode types (stick rod types).
The only requirement for this method’s success is to pick up the right consumables. Using the wrong stick rod would lead to cracking.
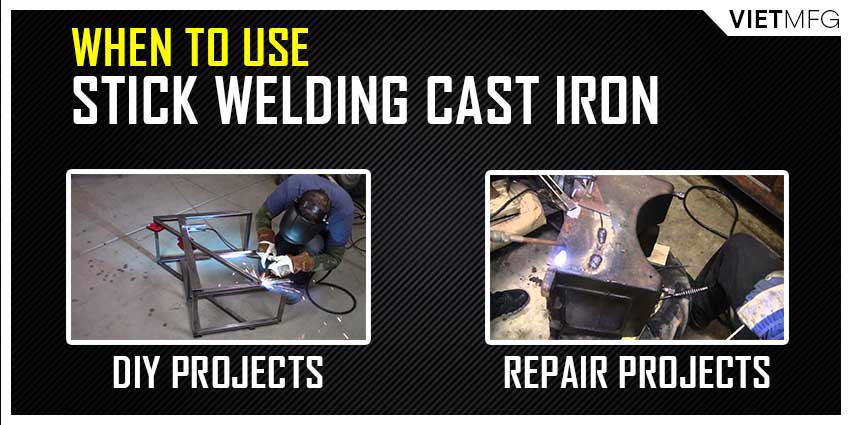
Choosing The Best Rod For Stick Welding Cast Iron
Basically, there are four main types of stick welding rod[3] that can be utilized for Stick Welding Cast Iron.
- 99% nickel rods: These pure stick rods are expensive and are regarded as the premium items. Welds produced from such rods are machineable. They run perfectly on cast iron pieces having low or medium phosphorus content.
- 55% nickel rods: These are more affordable options with nickel content of around 55%. They produce welds that are machineable, too. You will find these rods in repairing projects involving thick cast parts.
- Steel rods: These rods are the cheapest ones among the three types. They are the best seller for simple repair applications. However, welds produced by using these rods are not machineable and require some extra grinding for finish.
- Copper nickel rods: These options are often used when there is no emphasis on the final weld appearance, because stick weld cast iron with copper nickel rods will mess up the weld color.
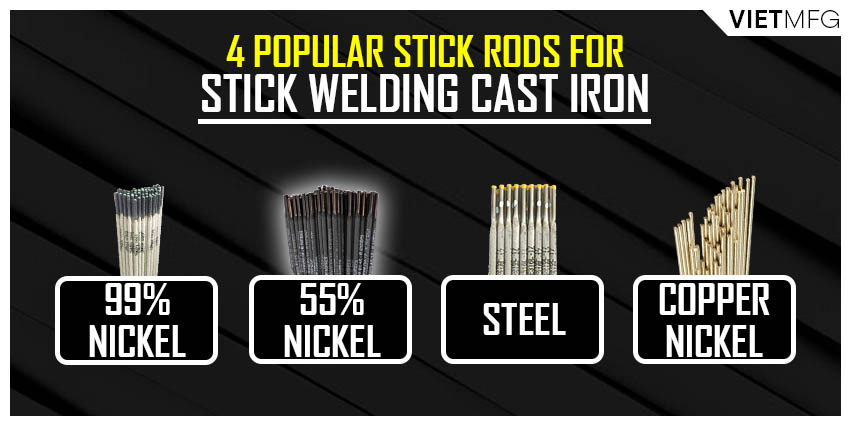
Preparation For Cleaning, Pre-heating And Post-heating Of Stick Welding Cast Iron
Cast iron is very sensitive to heat change. Thus, you must pre-heat and post-heat the cast iron pieces in order to avoid crackings. If cast iron faces a sudden heat change (from room temperature to welding temperature, and vice versa), the piece will experience too much stress and crack or fracture.
But before all of that, cleaning your workpiece is also important.
1. Cleaning Your Cast Iron Workpiece
Before a casting can be stick welded, it must be completely clean.
You have to remove all the grease, oil, paints and other contaminated compositions from the weld zone, just like in stick welding aluminum[4] or any other metal.
The edges of your weld joint should be chipped out and ground to form a 60 degrees angle as well.
Your cast weld joints should form a V groove with an angle ranging optimally from 60 to 90 degrees. This angle is called the “groove angle” in Picture 04.
The two pieces should not stick together. A distance of 1/8 inch is highly recommended. This is termed the “root opening”.
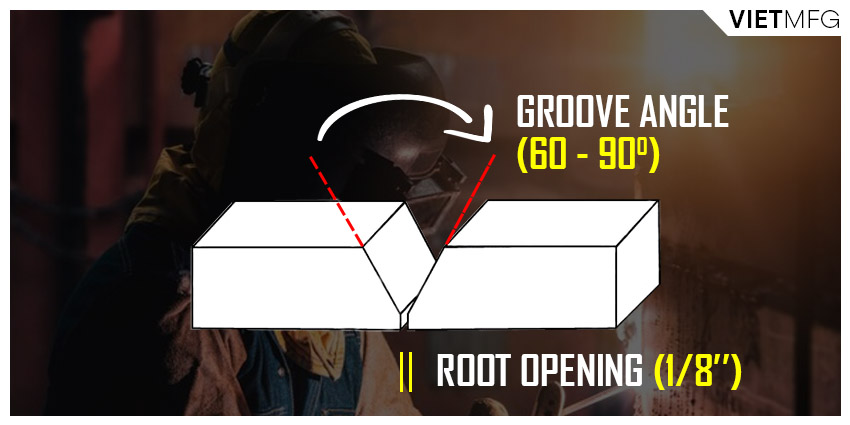
2. Pre-heating Your Cast Iron Workpiece
So, for pre-heating, you can simply use your blow torch to increase the material’s temperature.
Some hobbyists even use their car engines to deal with the job.
The ideal pre-heat temperature for cast iron pieces ranges from 260 to 650 degrees Celsius.
Just do not reach beyond 780 degrees Celsius, or you will overheat the material.
You can control the pre-heating process with a Tempilstik.
This pre-heating phase is very important, especially in repairing cast iron parts with complex shapes. The reason for this is that different thicknesses respond to heat differently. Without pre-heat, distortion and cracking is the inevitable result.
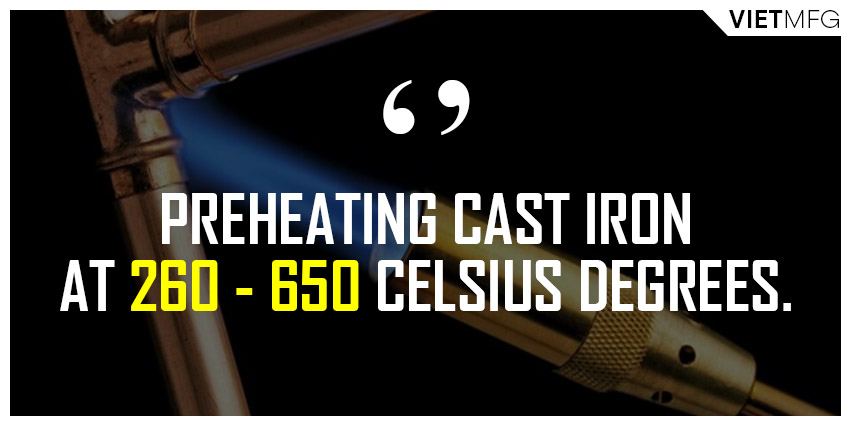
3. Post-heating Your Cast Iron Workpiece
To allow your cast iron workpiece cool down slowly, it is essential to wrap the object in an insulated covering.
Some DIY welders share that they let their cast iron workpiece sit in a bucket filled with sand, or place it on top of a wood fire oven to let the cool down occur gradually.
The top NOT-TO-DO thing in the cool down process is to quench your heated workpiece with anything cold like compressed air or water. The slower the cool down process is, the better.
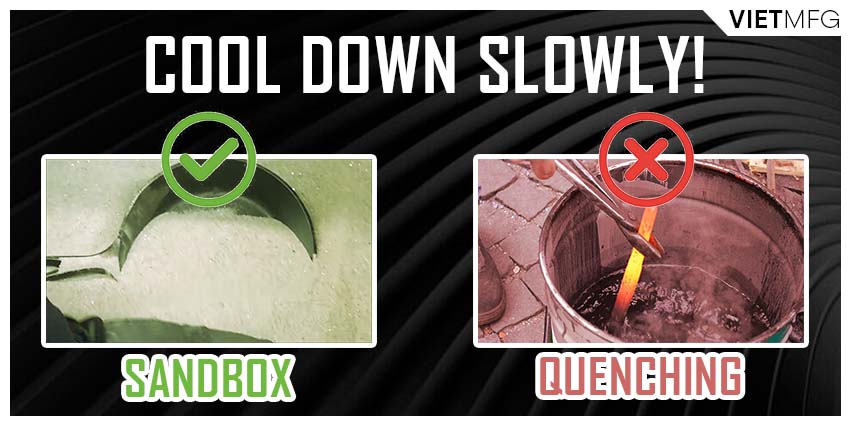
Heat Control During Stick Welding Cast Iron
The best advice on stick welding cast iron that I can give is to do it LOW and SLOW.
LOW here means setting up a low current. And SLOW refers to the slow travel speed.
When dealing with cast iron, make sure to weld at about one inch at a time and in various spots.
Try to maintain a 45-second break between segments to avoid the casting from being overheat.
All of this is done to keep your heat in control when stick welding cast iron.
Once your desirable weld appears, check for any slag hole or crack.
If you are clear with such defects, it is high time to remove any excess slag until you achieve a smooth surface.
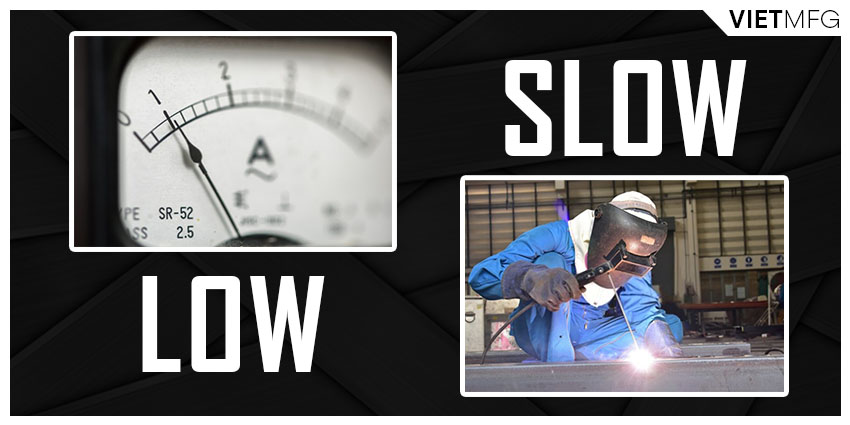
Certain Tips And Tricks In Stick Welding Cast Iron
In this following section, I will gather some tips and tricks that are helpful to get you done with stick welding cast iron:
- Use small-sized stick rods at a relatively low current setting. This helps minimize dilution and also avoid overheat issues.
- Maintain a medium arc length.
- It is best to perform stick welding cast iron in the flat welding position.
- Use multi-pass technique, which means you should skip welding the cast iron workpiece.
- Make sure to remove slag between passes, just like in stick welding stainless steel[5] and other metals.
- Peen the welds immediately after welding.
Preheat VS Cold Weld
I always recommend preheating your casting parts before stick welding them. However, with cast iron, there is always the debate on preheat and cold weld.
Some people argue that when using minimal heat to stick weld cast iron parts, the final welds are stronger than the preheat method.
This is not true. As heat is the only factor that can deform cast iron, stick welding this material in a cool manner will create internal stresses, which can be revealed later in the component’s life. Thus, the final welds must be weaker than when you actually preheat the metals before welding.
Preheating is always the advice of experienced welders to beginners. So, it is best to follow the expert’s advice.
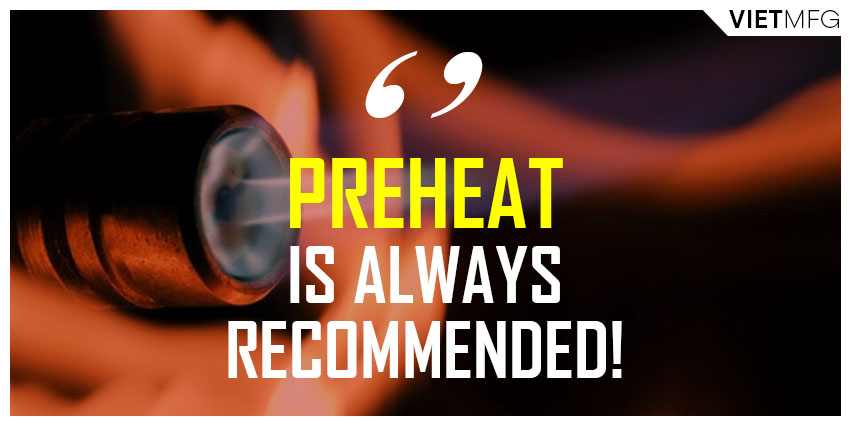
Conclusion
Stick welding cast iron is a quite challenging task.
It demands great preparation and heat control during the welding and cooling process.
However, fixing broken cast iron parts is a common welding project. Thus, let’s practice more with welding cast iron, especially stick welding of the material.
That’s it! Don’t forget to check out other articles of mine on the welding process in general.
Reference
- Guidelines for Welding Cast Iron. Lincoln Electric. Retrieved December 29th, 2021.
- Welding Cast Iron: The How-To Guide. Machines4u. Retrieved December 29th, 2021.
- How to Weld Cast Iron: A Full Guide. Welding Champs. Retrieved December 29th, 2021.
- Ultimate Guide to Cast Iron Welding. Weldguru. Retrieved December 29th, 2021.