Stick welding rod[1] is the single most important variable of the welding process. Your stick selection will determine the success or failure of a project, as it must be based on the base materials.
In this article, let’s explore everything there is to know about stick welding rods. This complete guide will support you with the following information:
- Basic knowledge about stick welding rods.
- Detailed analysis of each stick welding rod type, and how to select the right option for your project.
- Tips on storing and reconditioning stick welding rod.
No more procrastination! Let’s arm yourself with some knowledge right now!
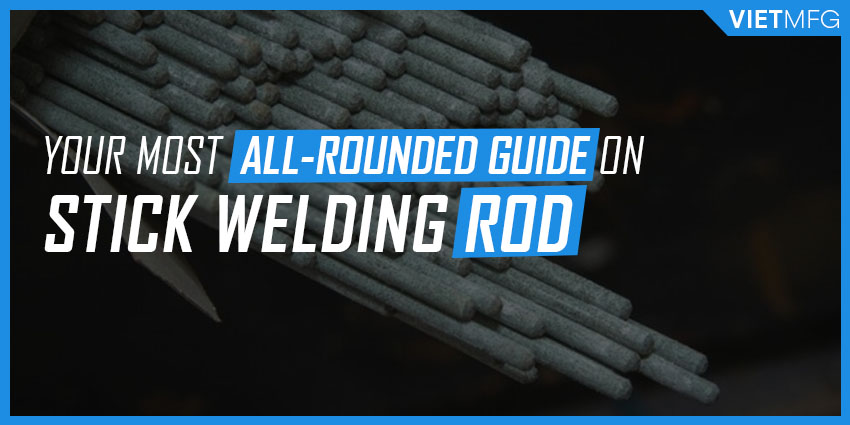
What Exactly Is Stick Welding Rod And Its Function?
In this part, we will go through the basic knowledge about stick welding rod, from its definition, composition to welding functions.
1. Let’s Define Stick Welding Rods
Stick welding rod is a consumable electrode used specifically for Stick Welding[2] (or SMAW) process.
Similar to MIG welding, the stick rod is considered consumable because it is consumed during the welding process. It acts as filler metal and melts down to become a part of the weld bond itself.
Stick welding rod is the soul of the stick welding process. Many stick techniques revolve around the utilization of a single rod. It gives the process high portability, reliability and simplicity. This is the reason why the stick welding process has yet to be replaced by other processes that are more modern.
2. Overall Composition Of Stick Welding Rods
Every stick rod comprises two parts: the core rod (internal part), and the coating flux (covering part).
The core rod is indeed a solid metal rod that is covered by a surrounding layer. That layer consists of mineral compounds and metal powders, mixing with a binding agent to provide its adhere ability to the welding surface.
The coating flux contains complex chemicals that release shielding gas upon when burnt. Moreover, it has many ionizing elements which helps form a slag layer on top of the weld joint. Some special types of flux are added deoxidizers (for better cleaning and penetrating effects) or iron powder (for enhancing electrode deposition rate).

3. What Is The Function Of Stick Welding Rods?
Each part of the stick welding rod carries a separate mission.
The core rod’s main function is to conduct electric current to the weld arc. Moreover, it serves as a source of filler metal for the joint. This is why you must choose the stick rod that has the same base metal as the workpiece. For example, stainless stick rods are used in stick welding stainless steel[3] .
Its size and type will determine the arc voltage and amperage requirements for the process.
With regard to the flux coating, it has two primary tasks:
- To shield the molten metal from atmospheric impurities, via the shielding gas released when burnt.
- To protect the weld metal from porosity and oxidation, via the slag formed after the welding process.
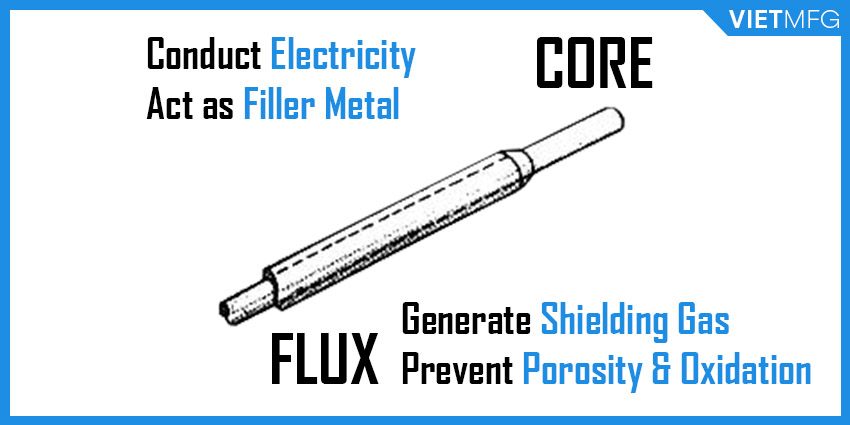
How Many Options Of Stick Welding Rods Do We Have?
There are a massive number of stick welding rods out there in the market that you can choose.
However, the trusted American Welding Society (AWS) has made an effort to categorize stick welding rods in their material called “A5.1 – Specification for Carbon Steel Electrodes For Shielded Metal Arc Welding”.
There are seven types of stick welding rods, namely E6010, E6011, E6012, E6013, E7014, E7018 and E7024.
These stick welding rods vary by the following criteria:
- Size of Core Rod: The most common sizes are 1/16’’, 5/64’’ and 3/32’’. Other sizes include 1/8’’, 3/16”, 7/32”, 1/4″ and 5/16”. The core rod’s size must be narrower than the materials being welded.
- Material: Stick welding rod’s materials must match with the base metal, as it serves as a filler rod. Usually, stick rods are made of mild steel, cast iron, iron-free and other special alloys.
- Tensile Strength: This criteria simply indicates the maximum amount of stress a piece of metal can withstand before failing or breaking.
- Welding Position: Most stick welding rods are applicable for all welding positions, except for E7024. You will understand why in the following section when I decode the stick rod names.
- Iron Powder Mix: This mix accounts for up to 60 percent of the flux composition. The more iron powder there is in the flux, the more molten metal available for the weld, as heat turns the powder into steel.
The Meaning Behind AWS Stick Welding Rod Classification
Before jumping into what each type of stick welding rod can do, I believe the first thing we need to know is the meaning behind those names.
1. Understanding AWS Stick Welding Rod Classification
The above AWS classification of stick welding rods is a part in their standardized classification system for welding electrodes. It is the combination of certain letters and figures that conveys the electrodes’ specific types and properties. It is always printed on the side of the electrodes for better recognition.
For stick welding rods, the AWS system works as follows:
- The first letter, which is “E”, indicates electrode.
- The first two figures signal the minimum tensile strength of the final weld, measured in psi (pounds per square inch).
- The third number represents the applicable welding position(s) of the electrode.
- The fourth digit reveals the type of coating (cellulosic, rutile, low hydrogen) and welding current (AC, DC, or both) that can be applied with the electrode.
Below is the table representing the meaning of the third and fourth digit from AWS Classification. These two digits specify certain properties that are suitable for the flux coating of your stick welding rod.
Table 01 – Meaning of third digit and fourth digit from AWS Classification.
Third Digit | Fourth Digit | |||
Digit | Meaning | Digit | Coating Type | Welding Current |
0 | Not applicable | 0 | High cellulose sodium | DCEP |
1 | All welding positions | 1 | Cellulose potassium | AC, DCEN, DCEP |
2 | Flat and Horizontal positions only | 2 | Titania sodium | AC, DCEN |
3 | Flat position only | 3 | Titania potassium | AC, DCEN, DCEP |
4 | Iron powder itania | AC, DCEN, DCEP | ||
5 | Low hydrogen sodium | DCEP | ||
6 | Low hydrogen potassium | AC, DCEP | ||
7 | Iron powder iron oxide | AC, DCEP | ||
8 | Iron powder low hydrogen | AC, DCEN, DCEP |
Let’s take E7018 as an example for better illustration of above ideas:
- E – obviously stands for electrode.
- 70 – means the minimum tensile strength is 70,000 psi.
- 1 – tells that all welding positions are applicable with this stick welding rod.
- 8 – reveals that this stick welding rod can be used for both AC and DC current, and its coating type is iron powder low hydrogen.
In short, E7018 is a stick electrode with a minimum tensile strength of 70,000 psi, applicable with all welding positions and welding currents, and its coating type is iron powder low hydrogen.

Let’s pay a little attention to the third digit and all seven names of our stick welding rods. You will notice that the third digit of six out of seven names is “1”, except for E7024. This is the reason why in the above section, I say that apart from E7024, most stick rods are applicable for all welding positions.
2. Have You Ever Seen The H4R Mark?
Now, If you have had your hands on a real stick welding rod before, especially the E7018, you would somehow see the mark “E7018 H4R”. So what exactly does H4R mean here? Well, this is a little bit more in-depth, but you can simply understand it as follows:
- H4 – means the maximum diffusible hydrogen content of 4ml/ 100g of weld.
- R – signals the moisture resistant ability of the stick rod, which means the ability to meet low moisture pickup limits under supervised humidification tests.
In short, the H4R mark indicates that the E7018 stick rod can be utilized up to nine hours after getting out of the sealed package. It can still deposit weld metal with less than 4 milimiters of diffusible hydrogen per 100 grams of deposited weld metal, and absorb moisture of less than 0.4 percent in the coating after being exposed.
When you use the E7018 H4R stick rods over an eight-hour working shift, you can rest assured that these H4R rods have not absorbed too much atmospheric moisture. Hence, it can prevent hydrogen cracking and ensure that the stick rod is always hot for welding.
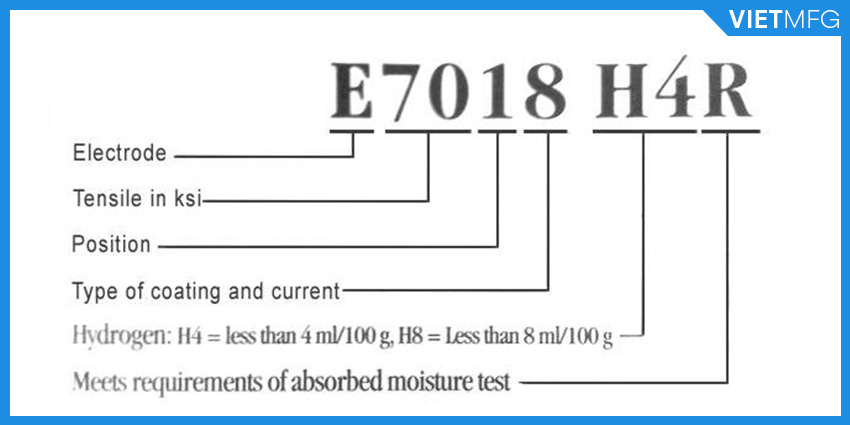
3. Do Not Classify Stick Welding Rods Based On Colors!
Some experienced welders can recognize different types of stick welding rods via colors. However, I personally think the colors are there for cosmetic purposes only. For beginners, please strictly follow the classification mark on the stick for correct identification.
But, if you are so curious about what those colors mean, then I will put the content right below for you:
Table 2 – Meaning of colors on Stick Welding Rods
Color | Meaning |
Red | Iron oxide |
Green | Chrome oxide |
Tan | Zinc ferrite and Iron oxide |
White | Titanium oxide |
Blue | Cobalt oxide |
Detailed Information On Each Type Of Stick Welding Rod
Just a quick recall. There are seven most popular types of stick welding rods, which are E6010, E6011, E6012, E6013, E7014, E7018 and E7024.
In this part, we will go a little bit deeper into each type of stick welding rod. Along the way, there will be small comparisons among every type, so that you can have a better picture in terms of their properties.
1. E6010 Stick Rod
E6010 stick rod is capable of delivering deep penetration and digging through many contaminants, such as rust, paint and oil.
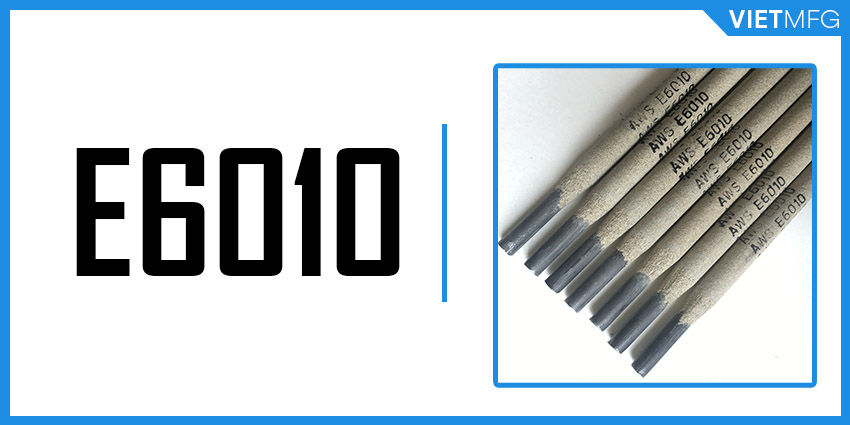
It is a great choice for many veteran pipe welders in performing root welding passes on a pipe, usually on its inside surface. Moreover, this stick rod is also wonderful for maintenance and repair welding projects, especially those with tight fit-up joints.
However, it is not very friendly with beginners. The E6010 stick rod has an extremely tight arc, which requires high precision.
It is applicable for DCEP power sources only, so take note carefully. Welding on AC or using some inverters will not burn this stick rod well enough.
Another important remark is to never put E6010 in electrode drying ovens.
Key properties:
Minimum tensile strength | 60,000 psi |
Welding current | DCEP only |
Coating type | High cellulose sodium |
Welding position | All welding positions |
Welding characteristics | Deep penetration, but tight arc |
Application | Root pass in pipe welding; maintenance and repair projects with tight fit-up joints |
2. E6011 Stick Rod
E6011 stick rod is regarded as the cousin of the E6010. They share many properties, such as the deep penetrating profile that can cut through dirty or corroded metal pieces.
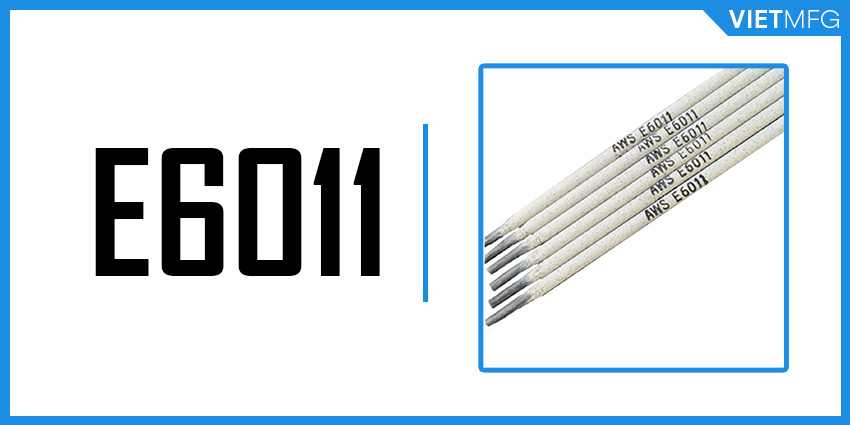
In addition, It has a soft arc designation with minimum spatter creation. Its slag formed after the stick welding process is also very easy to remove.
The only difference here is that E6011 is applicable with both AC and DC current. It gains this stick rod more versatility to be used in maintenance, repair projects, as well as wide root openings.
This stick rod is also NOT applicable for use in electrode drying ovens.
Key properties:
Minimum tensile strength | 60,000 psi |
Welding current | AC, DCEN, DCEP |
Coating type | Cellulose potassium |
Welding position | All welding positions |
Welding characteristics | Deep penetration, less spatter, soft arc, easy-to-remove slag |
Application | Wide root openings, maintenance and repair projects |
3. E6012 Stick Rod
E6012 stick rod is a perfect candidate for applications that require bridging the gap between two weld joints.
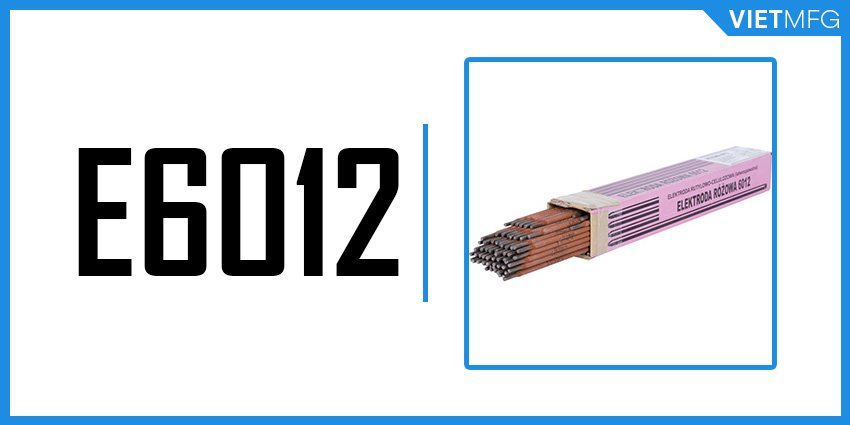
It is preferred by many professional welders for the use with fillet welds in the horizontal position. These particular situations demand high speed and high current. The stick rod also works well on thin metals and joints with poor fit-up conditions.
However, the drawback in utilizing E6012 stick rod is its shallow penetration profile. The rod also produces dense slag that needs extra efforts for removing.
Key properties:
Minimum tensile strength | 60,000 psi |
Welding current | AC, DCEN |
Coating type | Titania sodium |
Welding position | All welding positions |
Welding characteristics | Shallow penetration, dense slag, suitable with thin metals under poor fit-up conditions. |
Application | Joining fillet welds in the horizontal position |
4. E6013 Stick Rod
E6013 stick rod has a soft arc designation, easily-removable slag and produces little spatter as well. The biggest strength of E6013 stick rod is that it produces superior weld bead appearance.
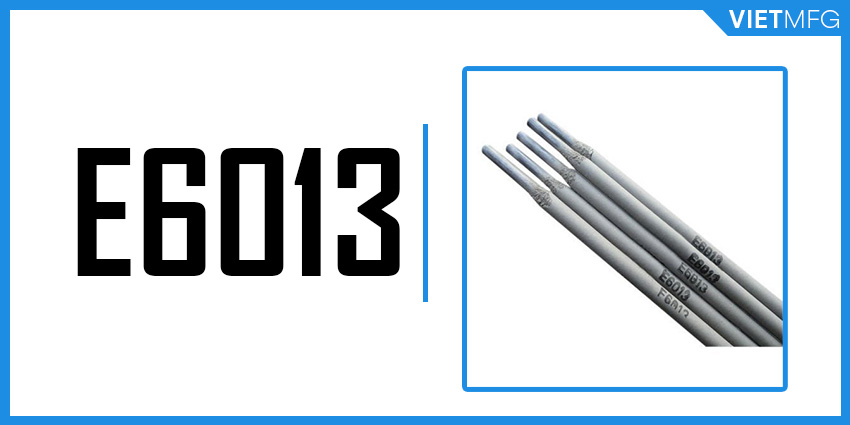
However, its penetration profile is moderately deeper than that of E6012, but not as deep as that of E6011 and E6010. Thus, E6013 stick rod is suitable for use with clean and new sheet metals only (as it cannot cut through dirt that well).
This type of stick rod is popular with farmers for many years. This is why it is called “farmer stick rod”. It is also a good option for beginners in their first try with stick welding.
Key properties:
Minimum tensile strength | 60,000 psi |
Welding current | AC, DCEN, DCEP |
Coating type | Titania potassium |
Welding position | All welding positions |
Welding characteristics | Superior weld bead appearance, soft arc designation, easily-removable slag, moderate penetration |
Application | Suitable with new, clean sheet metals; popular among farmers and stick welding beginners |
5. E7014 Stick Rod
E7014 stick rod is designed to have a run on carbon and low-alloy steels. It produces the equivalent level of penetration as that of E6012.
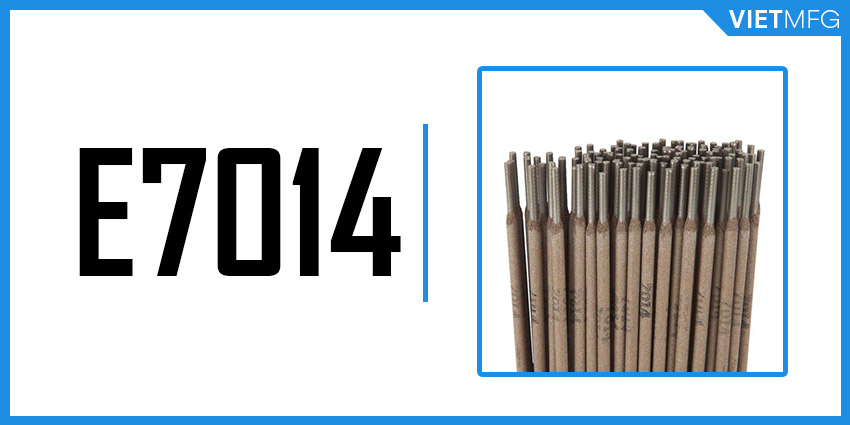
What makes E7014 different from the first four options is its higher tensile strength. Its coating also comprises a higher amount of iron powder, which enhances electrode deposition rate.
E7014 produces a strong weld. However, the wide puddle may pose difficult control issues for novice welders.
Key properties:
Minimum tensile strength | 70,000 psi |
Welding current | AC, DCEN, DCEP |
Coating type | Iron powder itania |
Welding position | All welding positions |
Welding characteristics | Shallow penetration, high deposition rate, strong weld, difficult to control |
Application | Carbon and low-alloy steels |
6. E7018 Stick Rod
E7018 stick rod is one of the easiest rods to use, with a thick flux of high power iron amount.
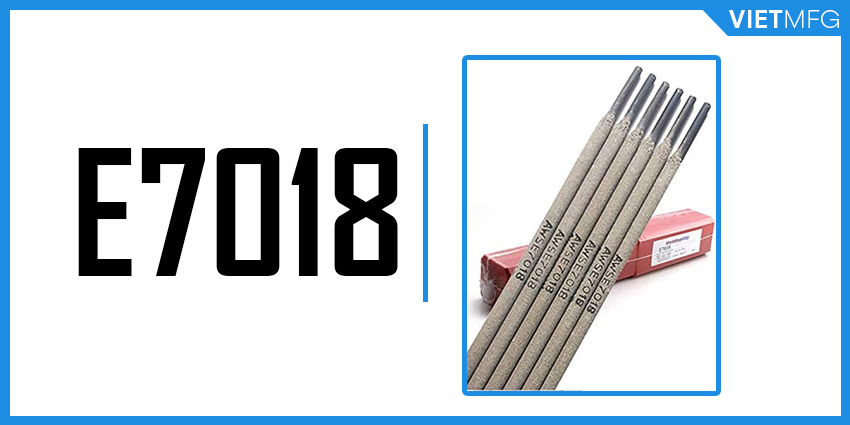
This all-rounded stick rod produces a strong and smooth arc, with high impact characteristics that can survive in cold weather. Its penetration level is medium, as the amount of spatter is very little.
Many experienced welders favor E7018 stick rod for applications of pipe welding and thick metals, such as structural steel. It can also be used on carbon steel, high-carbon or high-strength steel.
One interesting feature of E7018 is its flux coating composition. Thanks to the low hydrogen structure, E7018 has a lower moisture content and thus can prevent the entrance of hydrogen into the welds.
Please remember that this stick rod must be kept dry for use. Thus, use an electrode drying oven if it gets wet.
Key properties:
Minimum tensile strength | 70,000 psi |
Welding current | AC, DCEN, DCEP |
Coating type | Iron powder low hydrogen |
Welding position | All welding positions |
Welding characteristics | Strong and smooth arc, medium penetration, little spatter, durable |
Application | Suitable for pipe welding and thick metal application |
7. E7024 Stick Rod
Many welders select the E7024 stick rod for high-speed horizontal and flat fillet welds. It has a high level of iron powder content that greatly increases deposition rates. E7024 stick rod produces a wonderful weld bead appearance with easy-cleaning slag.
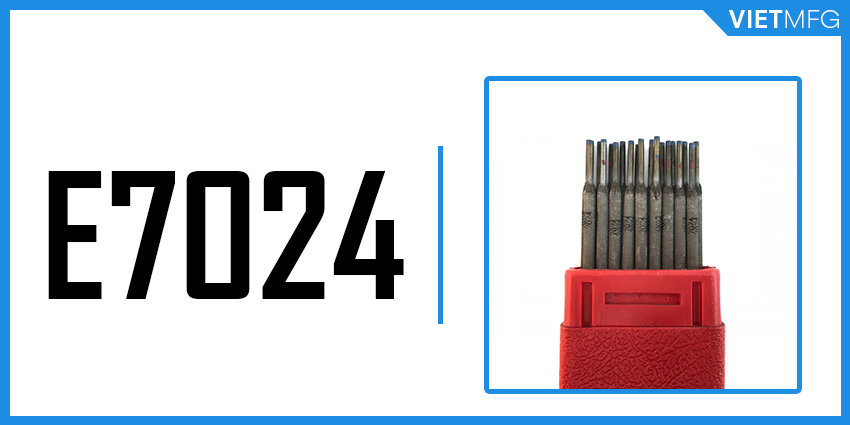
E7024 works well on steel plates with a minimum thickness of 1/4″, sometimes up to 1/2″.
Remember the special thing about E7024? It is only applicable for flat and horizontal welding positions. So, forget about applying it for vertical or overhead positions.
Key properties:
Minimum tensile strength | 70,000 psi |
Welding current | AC, DCEN, DCEP |
Coating type | Iron powder itania |
Welding position | Flat and Horizontal positions only |
Welding characteristics | Wonderful weld bead appearance, easy-removable slag, high speed, high deposition rates |
Application | Applicable on steel plate with thickness ranging from 1/4″ to 1/2″ |
Your All-Rounded Guide On Selecting Stick Welding Rods
Once you grasp the overall properties of each stick welding rod type, it will be easy to select the appropriate one for your project. What you need to do is to carefully consider these following factors:
1. Match The Strength And Composition Of Stick Rod To The Base Metal
The first and most important rule is to match the tensile strength and composition of the stick rod to your base metal.
For instance, aluminum stick rods should go with stick welding aluminum[4] .
However, stick welding cast iron[5] requires nickel rods (rather than cast iron rods).
2. Remember The Welding Positions And Power Sources That Your Stick Rod Can Perform
Coming up next are the criteria relating to welding positions and power sources.
Different types of stick rod will have different capability on welding positions and power sources.
As I have mentioned above, except for the E7024 stick rods, the remaining six types work fine with all welding positions.
Here is a small tip. For flat welding positions, you should consider those stick rods that offer high deposition rates (E7014, E7024) for better results.
For power sources, apart from E6010 stick rods, the rest can adapt well with both AC and DC current. However, be cautious with DC, as some stick rod types can only go with either DCEP or DCEN.
3. Assess The Fit-up Condition Of Your Joint
Fit-up condition also plays an essential part in your stick rod selection process. Why? Because fit-up condition is closely related to the amount of penetration required for the welding project.
Dealing with a tight fit-up joint (or the joint that is not beveled) demands stick rods that produce deep and digging penetration profiles. Suitable options for this case include E6010 and E6011.
On the contrary, for thin materials or joints with wide root openings, selecting stick rods that bring shallow penetration profiles is necessary to prevent burn-through. Ideal candidate for this case is E6013.
4. Consider The External Environment
Do not underestimate the effects of the external environment! Your stick welding rod may undergo significant impacts under too low or too high temperature, or shock-loading surroundings.
Thus, it is advised to think of these external conditions in advance, and select the stick rod that can live up to them.
For the above conditions (too hot or too cold environment), you can safely choose the low hydrogen E7018 stick rod for your application.
5. Choose Stick Welding Rods With Concentric Coating
Concentric coating refers to the uniform thickness of the covering layer encircling the core rod.
It has the function of directing and concentrating the weld arc.
When the coating is not concentric to the core rod, the stick rod melts unevenly, leaving a projection on the heavier side of the coating. This incident is called “fingernailing”. And it is not a good sign for your final welds. Fingernailing will cause poor arc direction and shielding, lack of penetration and inconsistent weld beads.
Thus, pay attention to this feature of your stick rod. Any stick rod having its coating concentric to the core rod is definitely of high quality.
Tips For Storing And Reconditioning Of Stick Welding Rods
The behind-the-scenes of stick welding rods include not only storage, but also the reconditioning process. Let’s uncover some tips on the two procedures that ensure a long-lasting lifespan for your stick welding rods.
1. Storing Stick Welding Rods
The best condition for storing stick welding rods is a heated environment with low humidity level. For example, the low-hydrogen E7018 stick rods are ideally stored at a temperature range from 250 to 300 degrees Fahrenheit.
The humidity level for storing stick welding rod should not surpass 70 percent at the temperature between 40 and 120 degrees Fahrenheit. For this reason, some stick rods like E6011 can totally be stored dry at room temperature.
Be careful with atmospheric moisture, as it can deteriorate desirable properties of the flux coating. Moisture can also cause the rod to produce massive spattering and even lead to porosity and cracking.
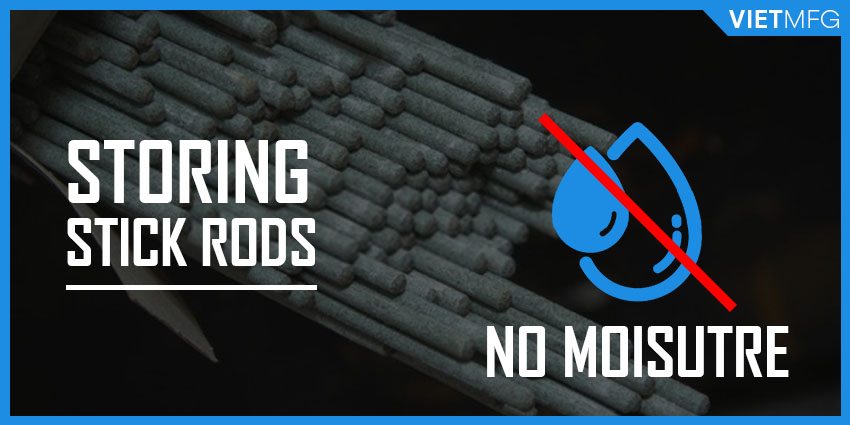
2. Reconditioning Stick Welding Rods
When the stick rods are exposed to damp air for more than two hours, it should be dried in an electrode drying oven. The heat set for these ovens is called reconditioning (or re-dry) temperature.
In general, reconditioning temperatures for stick welding rods are higher than the storage temperature. This higher heat helps in eliminating excess moisture.
Normally, stick welding rods require reconditioning heat at 500 to 800 degrees Fahrenheit for a duration of up to two hours.
Some stick welding rods having an “R” suffix can gain better resistance to moisture, and thus demand shorter reconditioning duration.
Conclusion
You have made it to the end of the article. I hope the writing has provided you with all the information there is to know about stick welding rods – soul of the stick welding process.
Keep checking out our other articles relating to stick welding, where I will go deeper into the application of certain specific metals.
Reference
- 8 Questions About Stick Welding Rods Answered. Miller. Retrieved December 09th, 2020.
- Stick electrode and welding basics. The Fabricator. Retrieved December 09th, 2020.
- Welding Electrodes. Weld Guru. Retrieved December 09th, 2020.
- Welding Rods Explained!. Keen Ovens. Retrieved December 09th, 2020.
- Stick Welding (SMAW) for Equipment Repair. Grainger. Retrieved December 10th, 2020.
- Shielded Metal Arc Welding Rods – Types of Welding Rods and where to use them. Welding Tips and Tricks. Retrieved December 10th, 2020.
- A BASIC GUIDE OF ARC WELDING ELECTRODES. Island Supply Welding Company. Retrieved December 09th, 2020.