Stick welding stainless steel[1] is considered one of the most money-friendly methods. It is perfect if you are running a budget constraint.
In this article, let’s learn more about this welding process for stainless steel with the following content:
- When is Stick welding stainless steel applicable?
- Discovering the 5 basic variables (CLAMS) of stick welding stainless steel.
- Some tips and tricks for enhancing your stick welding stainless steel.
Let’s start!
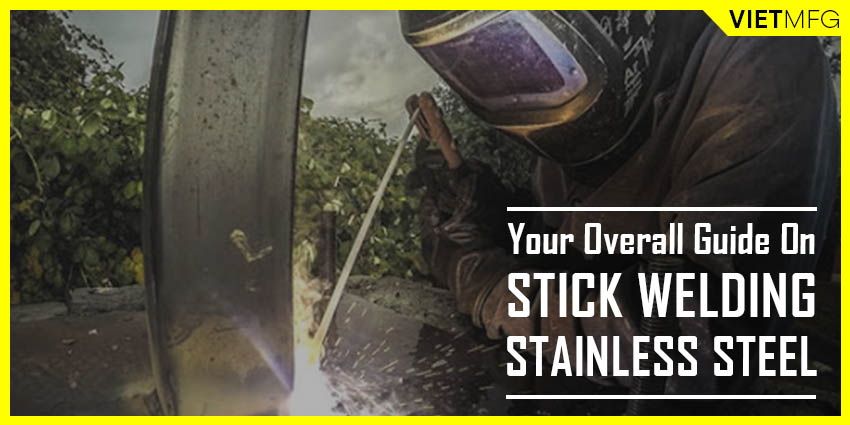
When Should Stick Welding Stainless Steel Be Used?
We all know that stainless steel can be welded by many processes, including TIG, MIG and Stick welding.
To answer the question, we need to understand our desired result for the final product.
If the project’s top priority is aesthetic and precision, you should obviously choose TIG welding.
If the project’s deadline is near, you might want to weld the stainless piece fast with MIG welding.
However, if budget is the key concern, you should consider using Stick welding. Among the three welding processes, Stick welding is regarded as the simplest and most portable process.
Stick welding can weld stainless steel from 0.05 inch all the way up to several inches of thickness.
Despite being the most economical welding process, stick welding also has the lowest deposition rates among all consumable electrode processes.
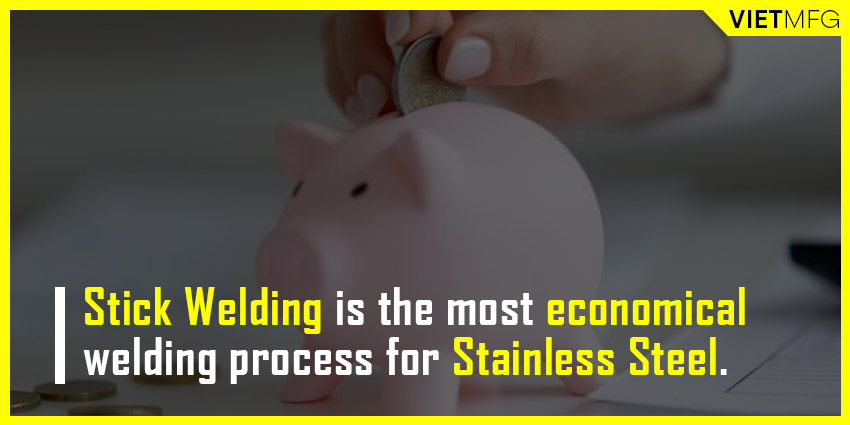
Five Basic Variables (CLAMS) In The Case Of Stick Welding Stainless Steel
If you have read my article on Stick Welding[2] in general, you will know that this process has 5 basic variables named CLAMS (Current setting, Length of arc, Angle of electrode, Manipulation of electrode, and Speed of travel).
In this section, let’s put them into the real case of stick welding stainless steel.
1. Current Setting For Stick Welding Stainless Steel
Usually, we use AC or DCEP to stick weld stainless steel. Among the two polarities, DCEP offers better weld penetration.
Regarding the amperage level, the bigger your stick welding rod[3] is, the higher range of amperage you would like to use.
Table 01: Recommended Amperage Range For 3 Typical Stick Rod Size
Stainless Stick Rod Type and Size | Recommended Amperage Range |
E308L – 3/32 inch | 40 – 80 A |
E308L – 1/8 inch | 75 – 115 A |
E308L – 5/32 inch | 105 – 160 A |
2. Length Of Arc For Stick Welding Stainless Steel
A good rule of thumb is to maintain the arc length similar to your stainless stick rod diameter.
So, if you are using an E308L 5/32 inch, you should have an arc length of around 5/32 inch as well.
3. Angle Of Electrode For Stick Welding Stainless Steel
Let’s follow the general principle applied for stick welding.
For flat and horizontal welding position, pull the electrode at about 5 to 15 degrees.
For vertical up position, remember to push the stick rod at about 5 to 15 degrees.
4. Manipulation Of Electrode For Stick Welding Stainless Steel
Make sure to employ oscillating motion for your stick welding stainless steel.
Also, lay your beads in short bursts of about 3 to 4 seconds.
I will explain this in the later part of this article.
5. Speed Of Travel For Stick Welding Stainless Steel
Again, make sure to follow our general principle on stick welding’s travel speed. Take your stick rod diameter and multiply it to 1.5 or 2 times. The final number is your desired travel speed.
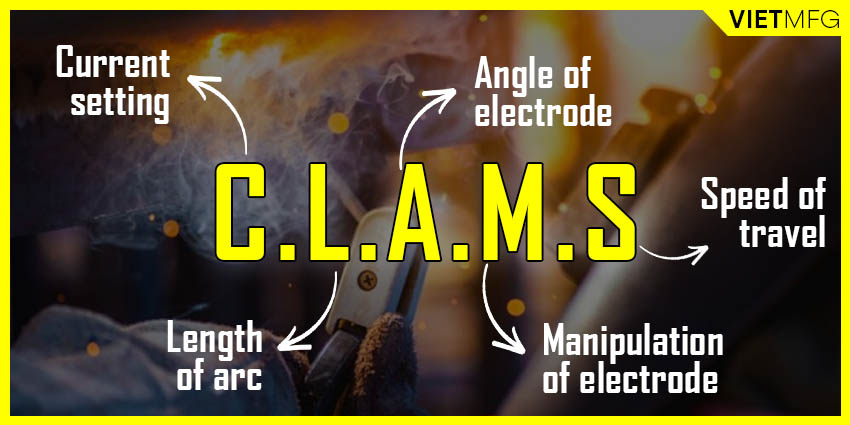
Tips And Tricks For Stick Welding Stainless Steel
In this following part, I will uncover some useful tips and tricks that you can use to enhance your Stainless Steel Stick Welding.
1. Make Sure To Wear Welding Helmet Properly!
During many of my articles, I always emphasize safety as the number one priority.
That rule still applies for Stick Welding Stainless Steel.
Besides safety apparels, you must wear a welding helmet properly, because the slag produced from Stick Welding Stainless Steel tends to fly off on its own.
Most of the time, this slag would get into your eyes, causing unnecessary damages.
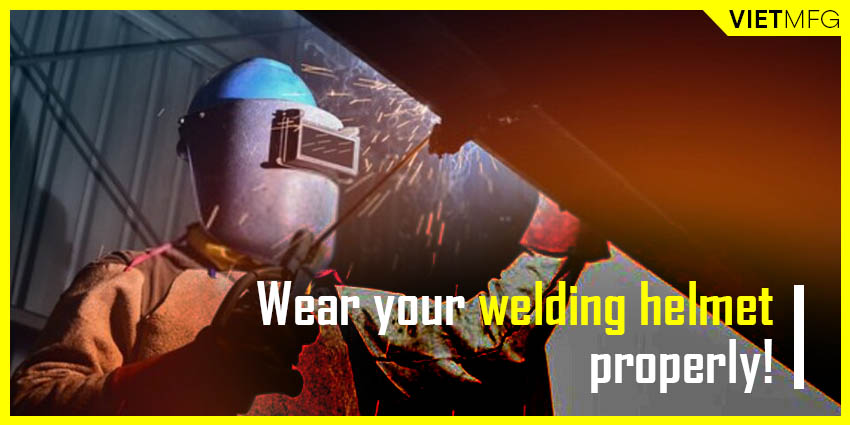
2. Set The Amperage Low And Slowly Increase It During Your Welding
We all know that stainless steel gets hot really fast (due to their low thermal conductivity).
When the stainless stick rods get hot, they run very differently than before. The metal droplets will come off more quickly, and the weld bead tends to crown.
You can run the stick rod perfectly for the first one or two inches, and all of a sudden, things change when the rod becomes hot.
Well, that is why we should set the amperage at the low range of what might be considered hot enough, and build our way up from there.
Also, as most stainless pieces are in thin shape, starting off at low amperage values can help avoid warping as well.
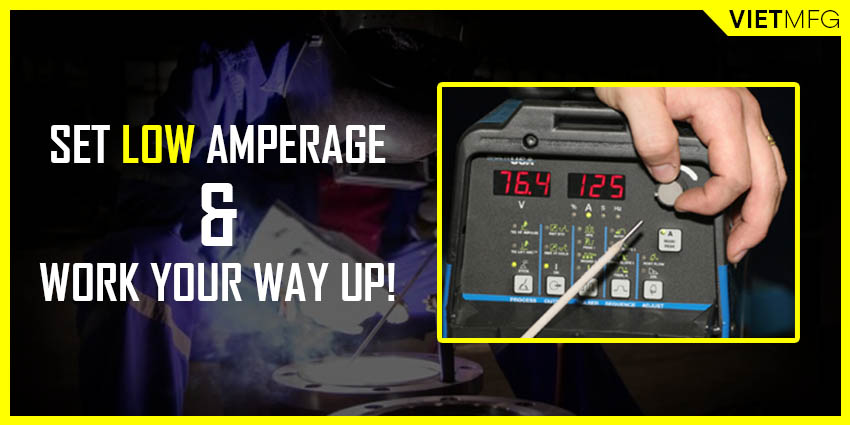
3. Pay Attention To How Red The Rods Become
Now, if you do not know how to set and adjust the amperage level in a suitable way, then let’s focus on the color of your stainless stick rods.
If they are way too red, you might need to turn down your heat (or amperage level) a little bit, unless you are welding on flat or horizontal positions.
Paying attention to how red the stick rods become is actually a pretty cool skill that only experienced operators have. It is very helpful when you switch from one machine to the other. You simply cannot copy the amperage setting on your last welder and paste it on the new machine.
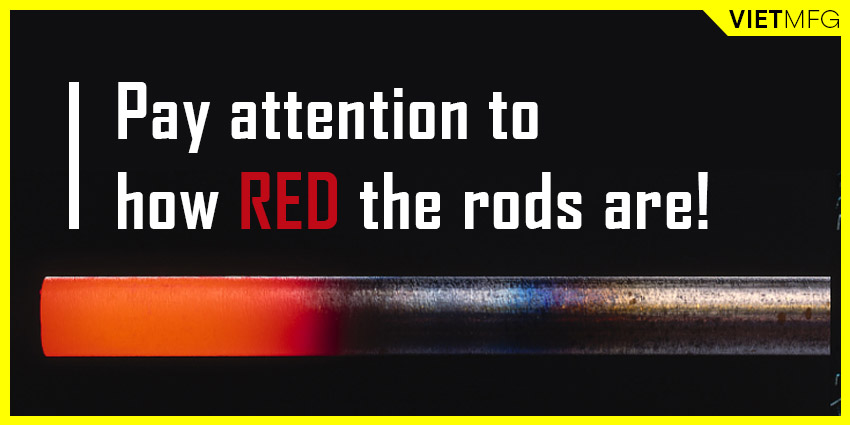
4. Exert Weaving Or Oscillating Motions
It is highly advised to use some sort of weaving or oscillating motions to allow the weld material to spread out a little bit.
Normally, I would use a J motion for stick welding stainless steel.
As stainless stick rods get hot too quickly, this J technique helps you spread your stainless out a little bit and flatten it. The J technique also helps you have a more even travel speed.
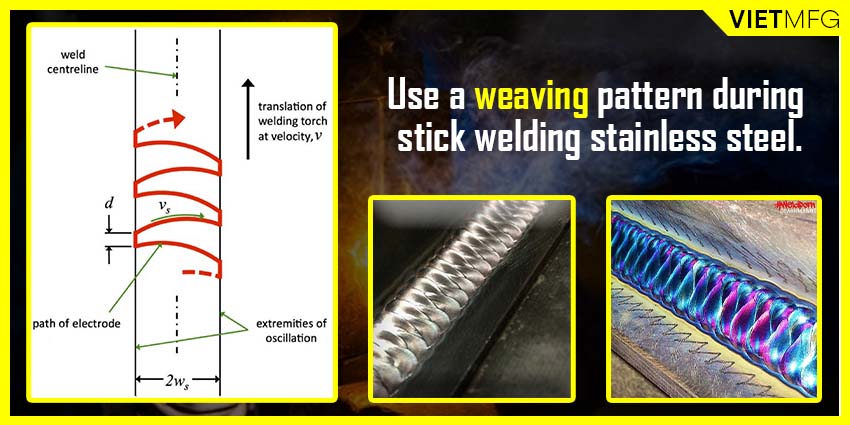
5. Secure Your Stainless Workpiece
Stainless steel can move on welding tables.
Therefore, remember to secure your stainless workpiece with clamps, and then tack weld it to your workpiece, just like in stick welding aluminum[4] and other base materials.
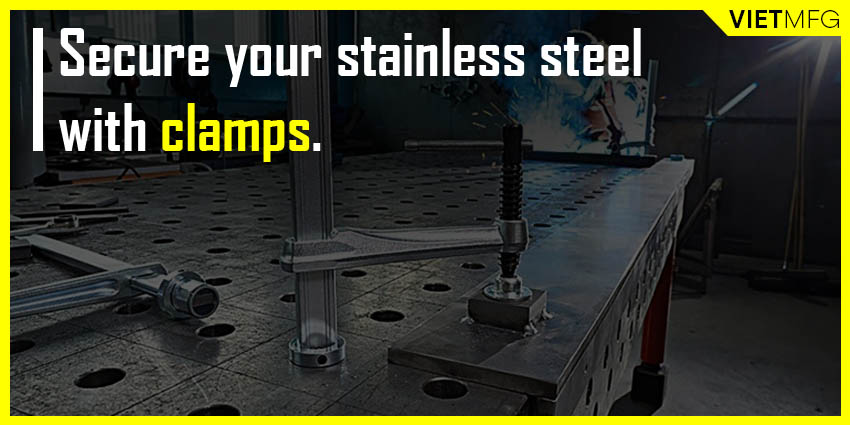
6. Preheat Recommended
Preheating your stainless workpiece is always useful in preventing cracking. This is very much similar to stick welding cast iron[5] .
This action is usually carried out with a blow torch, or an oxy acetylene (or oxy propane) torch.
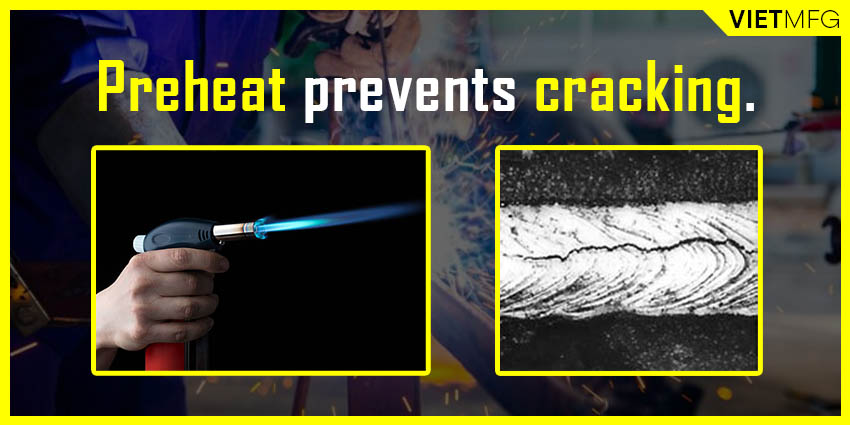
7. Don’t Trust The Weld Puddle
In Stick Welding Stainless Steel, the weld puddle is very deceiving. It makes you feel like you need to spend more time in some areas. But that feeling is not true. If you do that, you will have a very thick slag layer afterwards.
Thus, the solution is to just trust your gut. Bouncing the stainless stick rods between the two sides for about 2 seconds on each side, and keep repeating the process with that rhythm.
8. Let Your Stainless Workpiece Cool Down
After welding, allow your workpiece to cool down until all the redness disappears from that slag layer.
If you chip off the slag right away, the weld bead underneath will interact with the oxygen at high heat and become blue and purple.
One tip to speed up the process is to use the chipping hammer and just kind of touch the stainless piece to suck that heat out.
9. Weld Short Passes
Stainless steel can be warped very easily.
Thus, besides tack-welding to secure the pieces into proper shape, you also need to weld in short bursts of about 3 to 4 seconds. After that, stop and allow your stainless pieces to cool off and when weld again.
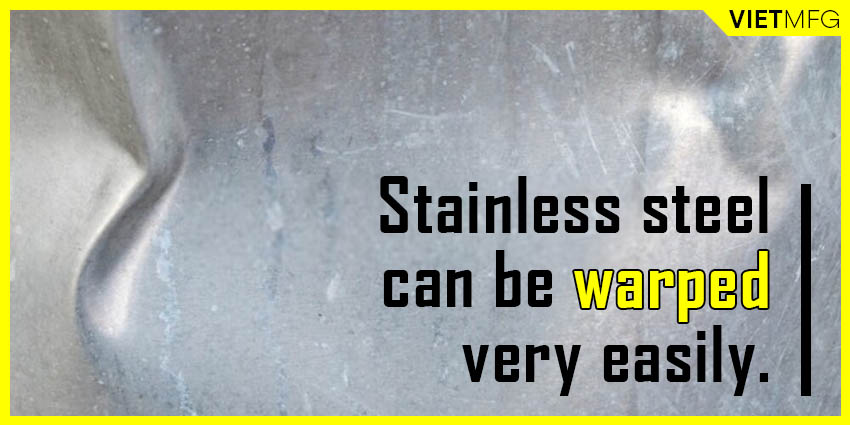
Conclusion
There you go! Another cool process of stick welding stainless steel to sharpen your skills.
Be patient and practice more! You will nail the process in no time.
If you find these articles helpful, then make sure to check out my other writings about other amazing welding processes as well.
Reference
- The Pros, Cons and Best Ways of Welding Stainless Steel. American Torch Tip. Retrieved December 25th, 2021.
- Welding stainless steel right. The Fabricator. Retrieved December 25th, 2021.
- Welding Stainless Steel. The Welders Warehouse. Retrieved December 25th, 2021.
- Stick Welding Stainless and Some Freakin Sweet Arc Shots. Welding Tips And Tricks. Retrieved December 25th, 2021.
- Welding Stainless Steel. R Tech Welding. Retrieved December 26th, 2021.
- Useful Tips for Welding Stainless Steel. Bakersgas. Retrieved December 26th, 2021.
- Stainless Steel Stick Welding – Adventures in Welding #117. Youtube (Adventures in Welding! channel). Retrieved December 26th, 2021.
- Stick Welding Tips For Stainless. Youtube (Weldingtipsandtricks channel). Retrieved December 26th, 2021.
- Vertical Stainless Stick Welding. Youtube (Weld.com channel). Retrieved December 26th, 2021).