Screw conveyor type is an intriguing topic that many fans of this machine would like to know. You will be amazed at the diversity of screw conveyors, due to their huge category amount.
Rest assured that your inquiry about the above topic will be answered in this article, as we will go through:
- Three main types of screw conveyors.
- Twelve in-depth classification of screw conveyors.
- General understanding of screw feeders, together with their types.
Alright, no more waiting! Let’s get to the business!
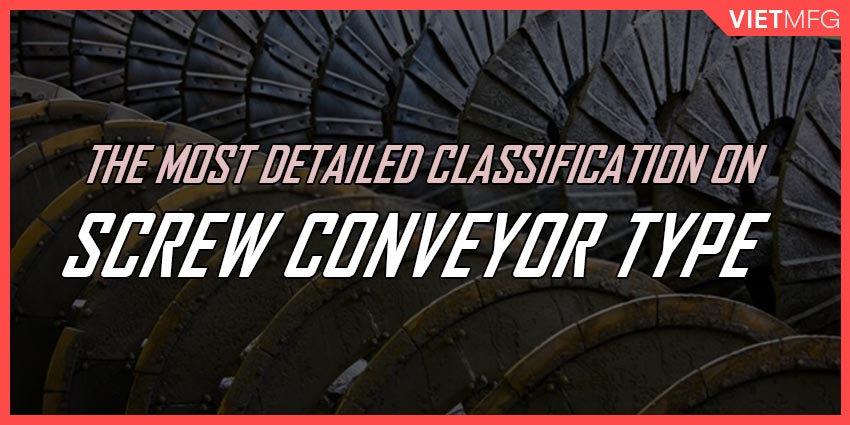
How Is Screw Conveyors Classified?
The term “screw conveyor” refers to one single manufacturing machine.
When put together different classes of the equipment, the overall conjunction is called “screw conveyor system”.
Depends on the overall screw conveyor design, the machine is classified into three (03) types:
- Horizontal screw conveyors.
- Vertical screw conveyors.
- Inclined screw conveyors.
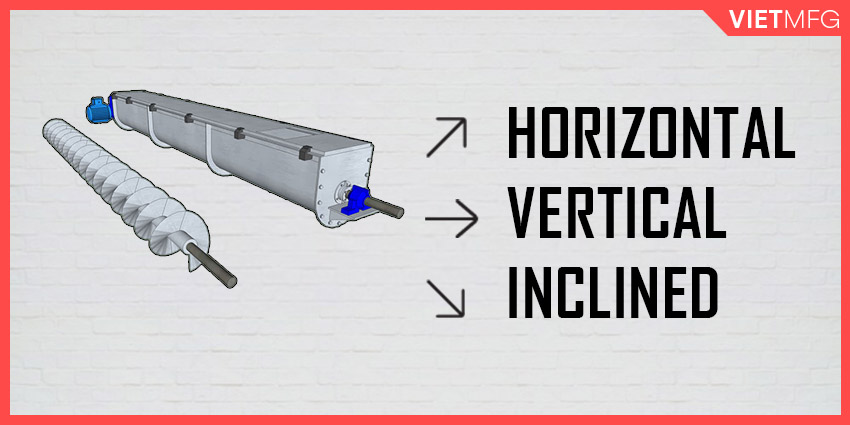
After learning about the overview of screw conveyor, it is essential to focus specifically on the three (03) above mentioned types of the machine.
1. Horizontal Screw Conveyors
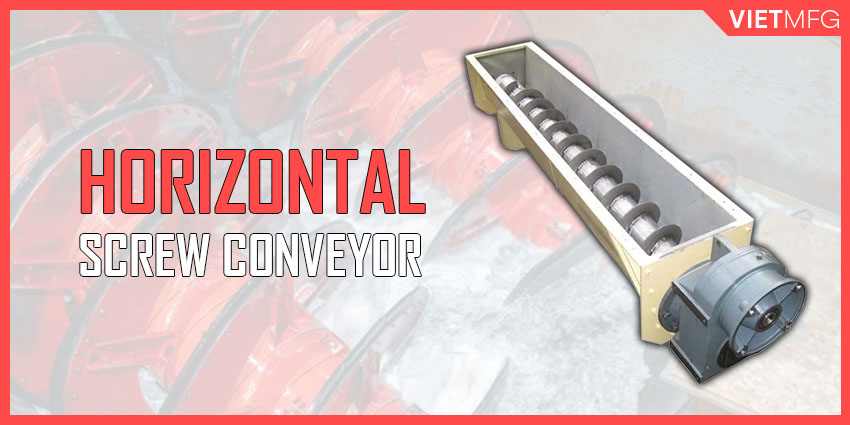
Being the most common type in industrial use, horizontal screw conveyors are designed to move bulk materials from one end of a procedure to another.
Horizontal screw conveyors are highly customizable, with a large range of lengths and sizes.
In general, screw conveyors are intentionally created to travel granular particulates certain levels of trough loading.
Depends on the characteristics of the conveyed materials, trough loading can be 15-percent, 30-percent or 45-percent.
- Specifically, the highest trough loading level is applicable for light, free-flowing and non-abrasive particulates
- With heavier, sluggish and more abrasive materials, lower levels of trough loading (15-percent and 30-percent) are more suitable.
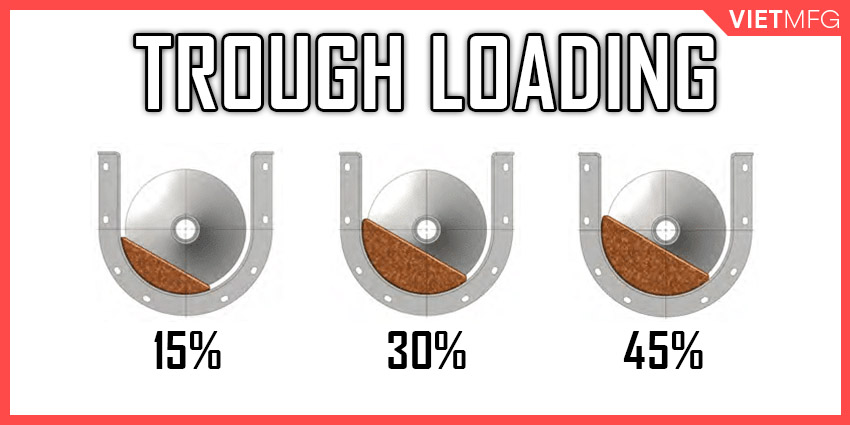
The drive unit of horizontal screw conveyors is ideally placed at the discharge end.
It helps put more tension on moving the particulates towards the discharge, and thus reduce wear and tear on the machine’s components.
Advantages of using Horizontal Screw Conveyors:
- Most suitable for moving semi-fluid materials, both free flowing and sluggish items.
- More cost-effective, compared to other types of screw conveyors.
- Effectively convey materials to various locations, by acquiring many inlet and discharge points.
- Completely enclosed for corrosive or hazardous conditions.
2. Vertical Screw Conveyors
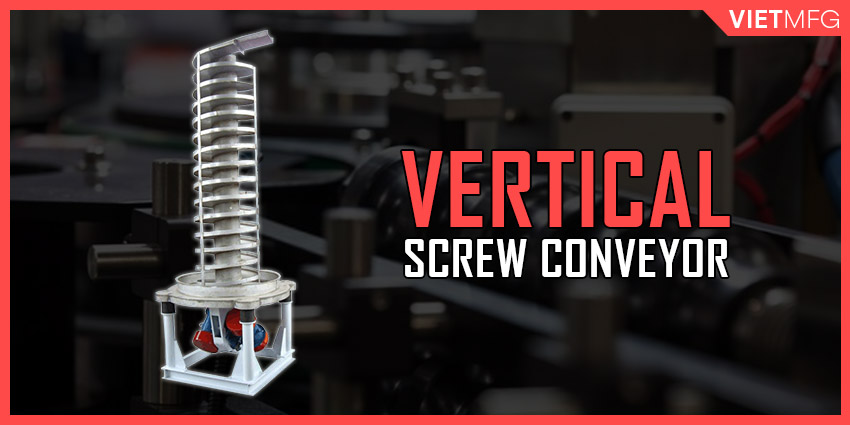
Under circumstances of fully vertical or very shaft inclines (over 45-degree), vertical screw conveyors prove to be highly effective in elevating granular materials.
Vertical screw conveyors can successfully meet the demands of various industries, ranging from minerals processing, chemical, wastewater treatment to even food products.
Additionally, the vertical equipment has neat designs that can fit into any plant layout.
Advantages of Vertical Screw Conveyors:
- Most suitable for moving semi-fluid materials.
- High capacity (around 6,000 ft3/hr).
- Can convey particulates up to 30-feet without internal bearings.
- Completely enclosed for vapor-tight conditions.
3. Inclined Screw Conveyors
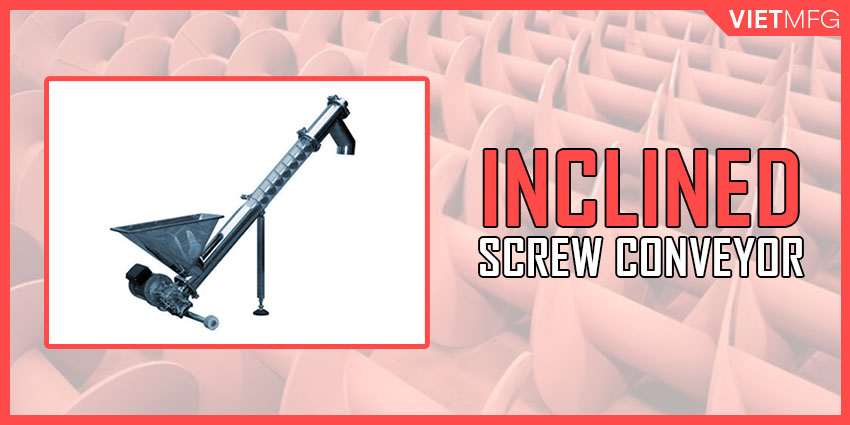
Inclined screw conveyors can efficiently operate from moderately above the ground level to a maximum 45-degree angle.
Any position above 45-degree, the machine is classified as a vertical screw conveyor.
The higher the incline angle, the lower the elevating efficiency.
Furthermore, in such cases, the screw conveyors would demand more horsepower requirements to compensate for gravitational force and the fall back of bulk materials.
In short, the machine efficiency relies on the incline angle, the material characteristics of conveying items, the trough and screw pitch of screw conveyors.
Below are some design features that engineers should pay attention to when manufacturing incline screw conveyors:
- Incline angle at maximum 10-degree: can minimize conveying efficiency loss. This loss is further reduced by boosting screw conveyor speed, expanding screw conveyor diameter, or lowering screw conveyor pitch.
- Incline angle between 10-degree and 20-degree: can control conveying efficiency loss at around 10-percent to 40-percent. This loss can also be reduced by increasing the speed and diameter of screw conveyors. Supplemental horsepower is required to compensate for gravitational force and the fall back of granular particulates.
- Incline angle between 20-degree and 30-degree: can control conveying efficiency loss at around 10-percent up to 70-percent. This loss can also be reduced by speed and diameter of screw conveyor. Supplemental horsepower is required to compensate for gravitational force and the fall back of granular particulates.
- Incline angle between 30-degree and 45-degree: can control conveying efficiency loss at around 30-percent up to 90-percent. It is recommended to boost screw conveyor speed. Supplemental horsepower is required to compensate for gravitational force and the fall back of granular particulates.
Other Types Of Screw Conveyors
1. Shaftless Screw Conveyors
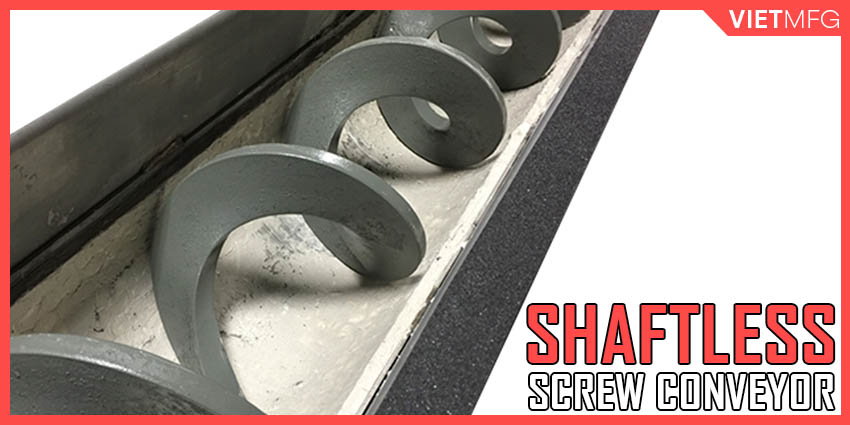
Particulates releasing from centrifuges or mixers is handled easily via a shaftless screw conveyor.
Hard-to-convey materials are no longer a problem, as shaftless screw conveyors supply a very smooth conveying surface.
The machine is applicable in many industries, including minerals processing and wastewater treatment, to food and chemical production, to transport biosolids or catalysts, etc.
Advantages of Shaftless Screw Conveyors:
- Most suitable for sluggish materials.
- Enhance efficiency, compared to other types of screw conveyors.
- Greater flexibility for any plant layout.
- No Internal bearings required.
2. Belt Screw Conveyors
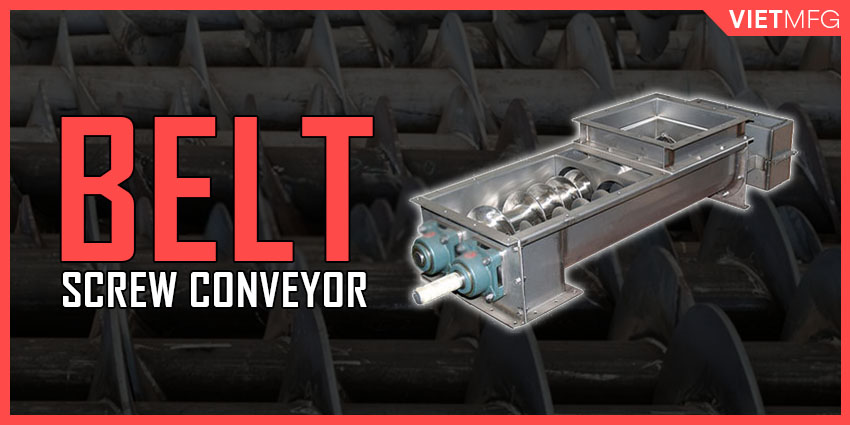
Belt conveyors are the most popular type of screw conveyor and thus have diversified applications in many industries.
Acquiring a long and rotating rubber or polymer belt, the machine can transfer materials, with the additional support of at least two uni-directional pulleys – which is covered by the belt.
3. Chain Screw Conveyors
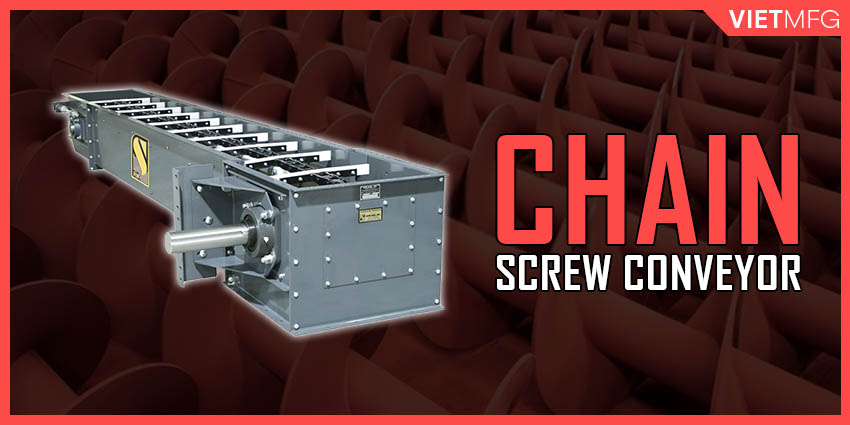
The power of chain conveyors comes from the drive unit.
Thanks to the chain drive, operators can easily adjust its speed by rotating gear ratio.
Chain conveyors are most suitable in moving items that are abrasive, fragile and/or dry.
4. Roller Screw Conveyors
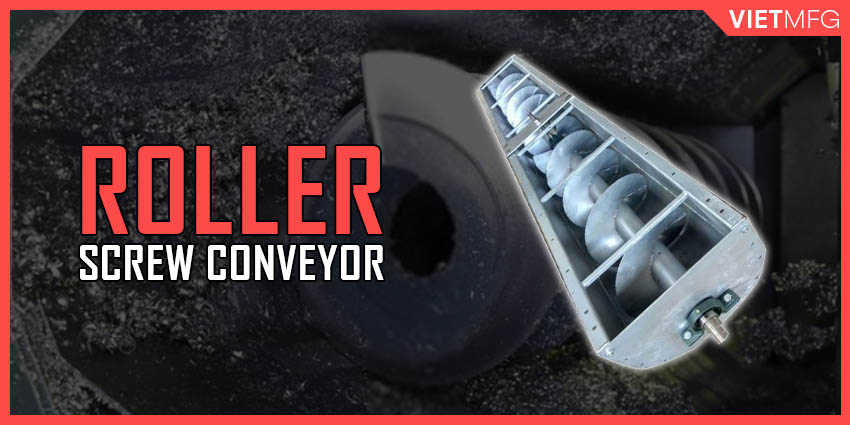
This type of screw conveyors comprises a number of round rotating components called rollers which are situated on a flat bottom.
The power source for roller conveyors is an electric motor, or even gravity.
Thanks to their simple and efficient design, roller conveyors are implemented in many fields, ranging from: shipping and distributing, to washing and drying.
5. Spiral Screw Conveyors
The term refers to any screw conveyor model having a fixed enclosed spiral screw.
6. Overhead Screw Conveyors
As per the name, overhead conveyors have their tracks mounted to the ceiling or walls, and fully operate upside down.
Thanks to the unique characteristic, overhead conveyors effectively utilize gravitational force and thus can run without electrical power.
However, there are still some models using electrical power, or pneumatic, vacuum forces.
Another pro of this screw conveyor’s type is that it does not occupy floor space. Such a spacious room is free for the company’s other arrangements.
7. Gravity Screw Conveyors
Gravity conveyors move items using gravity force instead of a motor engine.
8. Tubular Drag Screw Conveyors
Tubular drag conveyors possess a chain drive equipped with augers, or screw blades.
Tubular conveyors are very versatile, with various options for operating velocity, torque and capacities.
9. Pneumatic Screw Conveyors
Pneumatic screw conveyors transfer bulk powder materials mainly with the assistance of air power.
10. Flexible Screw Conveyors
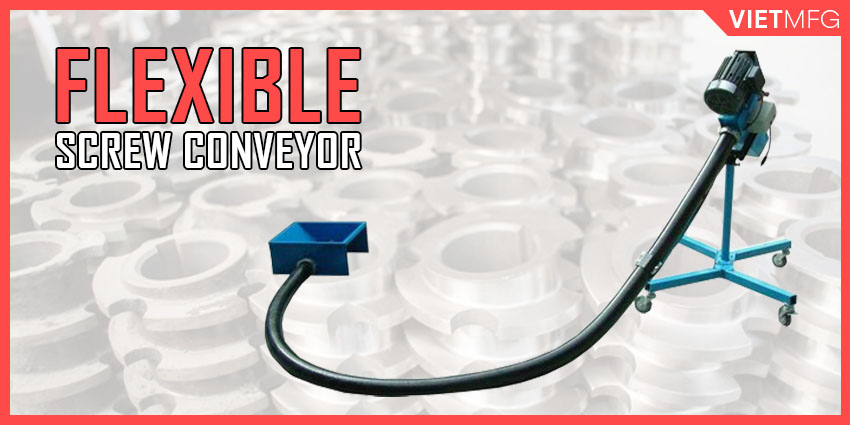
Flexible screw conveyors are capable of changing shapes to best fit your workspace.
Unlike traditional screw conveyors, which cannot be moved, flexible screw conveyors can significantly utilize the facility zone and have various applications.
11. Portable Screw Conveyors
Portable screw conveyors come with the option of mounting the machine to objects such as carts or vehicles.
Normally, they are used to deliver powdered or fragmented particulates.
12. Vibratory Screw Conveyors
Vibratory screw conveyors should be considered in need of horizontal or shallow inclined delivery of bulk materials.
For inclined convey, the optimal direction is downward with an angle less than 10 degrees.
Their main part is the vibrating trough made of metal.
The machine uses electromagnetic force or electromechanical force from the vibrators attached underneath the trough.
13. Bucket Elevators
Bucket elevators can be attached to a vertical screw conveyor or an inclined screw conveyor, with the aim of transferring items using buckets.
Basic Characteristics Of Screw Feeders
1. What Are Screw Feeders?
Screw Feeders are utilized in metering and conveying items. They are positioned in the first phase of the entire conveying procedure.
From the usage of screw feeders, engineers can precisely calculate and moderate feed rate (or capacity).
Screw feeders are highly customizable, with various settings and configurations.
Screw feeder’s inlet is always fully loaded.
In drafting screw feeders, a valuable advice is to design the machine with unwavering outside diameter and pitch.
The rationale behind is to draw conveying particulates evenly across the full length of the screw feeder’s inlet, as the materials move towards the discharge.
2. Acquiring Screw Feeder Shroud To Prevent Material Flooding
Screw feeders must be equipped with a shroud to impede material flooding past the inlet. The shroud is a curved shelter, converting a standard U-trough into a tubular housing, with an aim to prevent conveying particulates from spurring out of the screw.
3. Screw Feeder Capacity And Speed
The Control Pitch is the pitch of the last screw auger that goes into the screw feeder shroud. This figure determines the machines’ feed rate (or capacity).
The capacity of the Control Pitch is measured in ft3/hr/RPM.
The screw feeder’s speed is calculated by dividing the maximum capacity of the screw feeder (ft3/hr) by the capacity of the Control Pitch (ft3/hr/RPM)
4. Screw Feeder Horsepower Requirements
Compared to screw conveyors, screw feeders demand higher horsepower and torque.
An important start-up condition of screw feeders is the fully loaded inlet of bulk materials.
As the pressure rises up, bulk materials have a tendency to pack in the hopper, bin or silo, which are directly mounted to the screw feeders.
Therefore, the denser the bulk materials, the higher level the horsepower and torque requirements.
Types Of Screw Feeders
1. Variable Or Stepped Pitch
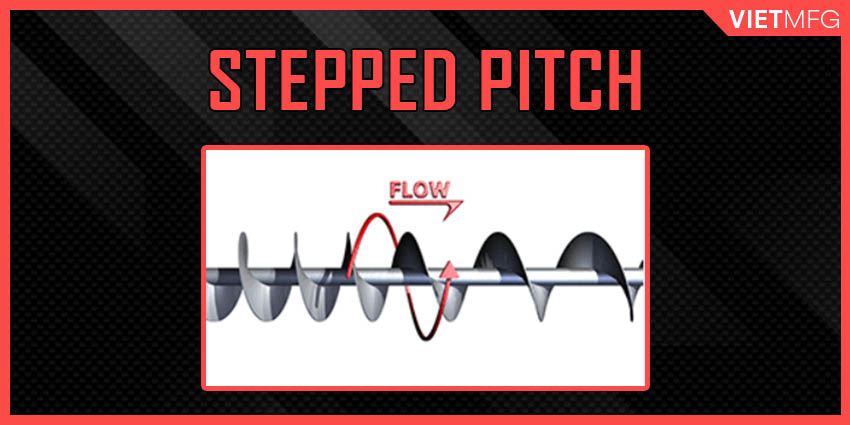
For variable pitch type, towards the screw feeder’s discharge, the pitch of the screw increases in length under the inlet area, thus creating more space for conveying items from the hopper.
For stepped pitch type, the auger pitch changes in increments.
For instance, a stepped pitch screw feeder may have 1-feet of 2/3 pitch, then 1-feet of 1/3 pitch under the inlet area.
2. Tapered Outside Diameter
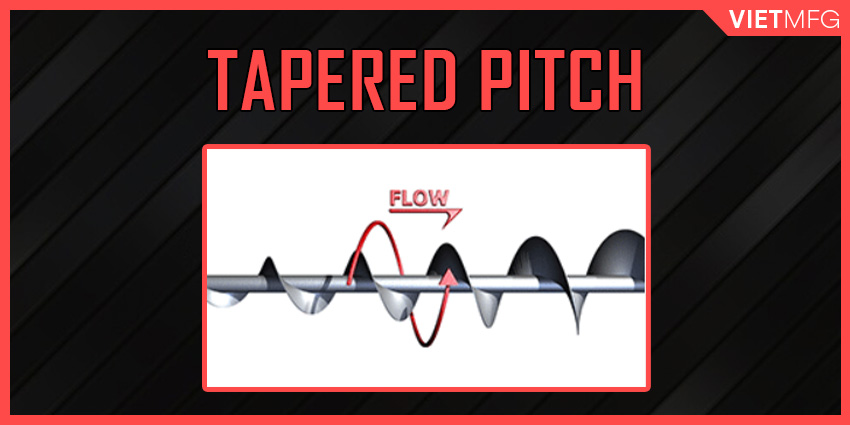
The outside diameter of the screw is tapered from the inlet rear to the shroud, to make room for more granular particulates receiving from the hopper.
3. Mass Flow
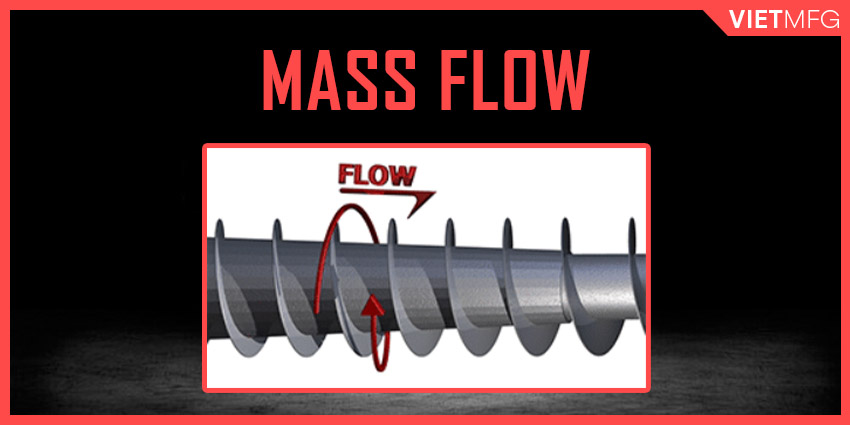
The mass flow design is a combination of variable pitch and tapered inside diameter.
A tapered cone is located on the center pipe of the screw, spanning from the inlet rear to approximately the center of the inlet opening.
Short pitch flights are mounted on the cone to open space for an additional amount of bulk materials from the hopper.
Variable pitch is then installed from where the cone ends to continue the discharge.
4. Multiple Diameter Screw Feeders
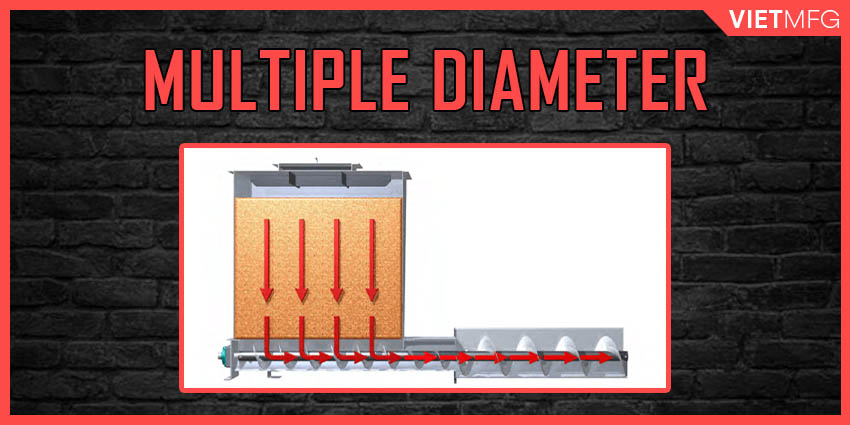
Simply put, Multiple Diameter Screw Feeder is a screw feeder, with the installation of an extension conveyor.
The screw feeder meters the conveying items to the larger diameter extension conveyor.
Once the items reach the extension conveyor, the trough loading then drops and the items are continued to be transported to the discharge.
Hanger bearings are available in the extension conveyor, only when trough loading level is below 45-percent.
5. Live Bottom Screw Feeders
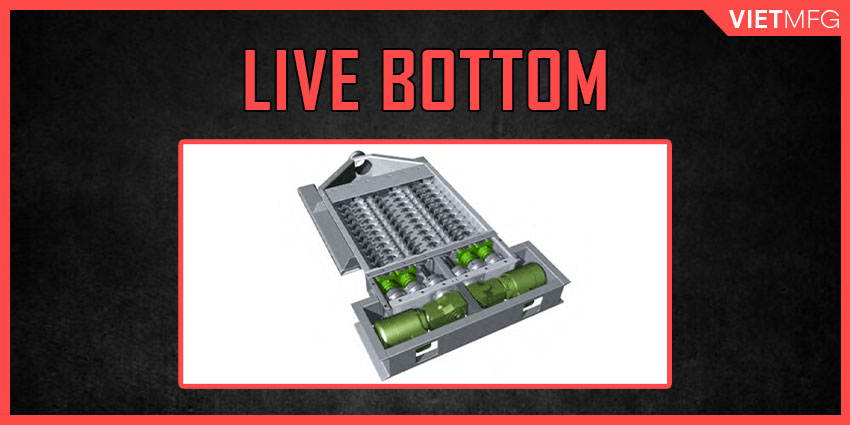
Live Bottom Screw Feeders are created for utilization with large hoppers, with large discharge openings.
The live bottom screw feeder acquires many screw feeders in use together, creating a “live bottom” to hamper bridging.
Particulates are metered and extracted equally from the inlet opening.
6. Inclined Screw Feeders
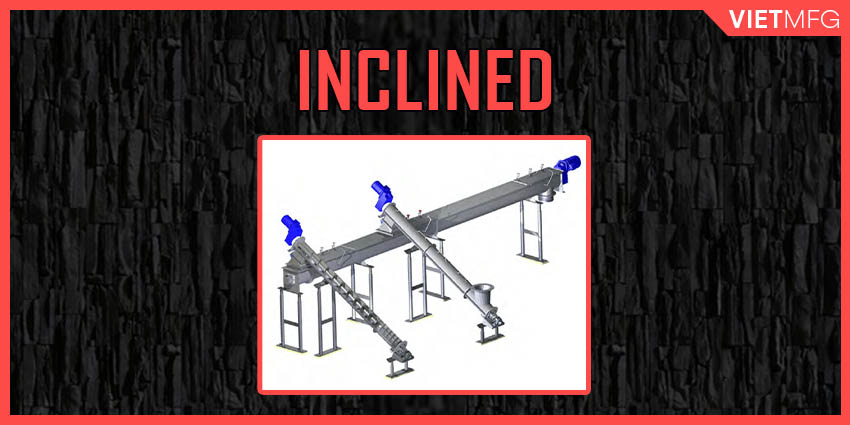
Inclined screw feeders meter and transport granular items from hoppers, and function similarly as horizontal screw feeders.
When designing inclined screw feeders, knowledge of the flow characteristics is significantly important.
Additionally, the angle of repose and flowability of conveying items will regulate the design of the screw feeder and the maximum incline angle.
Efficiency loss would be visible when screw feeders function at an incline angle larger than 5-degree, from horizontal surface.
Three (03) factors dictate the efficiency loss include: the incline degree of screw feeder, the repose angle and the particulates’ flowability.
Regarding the usage of screw feeder troughs, U-troughs are more suitable for an incline angle below 15-degree, and tubular housings are advised for over 15-degree inclination.
Regarding screw pitch, shorter pitch allows for greater incline efficiency factor, as it supplies a smoother conveying surface, and less materials falling back.
Therefore, full pitch augers on an inclined screw feeder are the least recommended choice.
- Inclined Screw Feeder Speed: In order to compensate for gravitational force and material fall back, inclined screw feeders must operate with higher velocity, compared to horizontal types.
- Inclined Screw Feeder Horsepower Requirements: Once again, inclined screw feeders demand extra horsepower and torque, compared to horizontal types. For the same reason, the additional specification requirement is needed to win gravitational force and cope with material fall back.
- Inlet length: The inlet length must be minimized to hinder the granular particulates from falling back in the inlet area. Most of the time, the length should not exceed 2 times the screw diameter.
Auger Pitch Changes
Inclined screw feeders are typically designed with many auger pitch variations. Shorter pitches are used in the inlet area to regulate the feed rate (capacity).
Typically, the flight pitch increases beyond the inlet to reduce the trough loading to less than 100-percent.
Last Note
That is everything about screw conveyor type. I believe the article has provided you with essential knowledge on the classification of this great agricultural machine.
There is a vast amount of information about other elements of screw conveyors. Therefore, make sure to stick around and check out other articles.
FAQs
Link Out And Prosper
1. Type Of Screw Conveyors. KWS. Retrieved on April 09th, 2021.
2. Different Types Of Screw Conveyors. Reinke And Schomann. Retrieved on April 09th, 2021.
3. Classification and working principle of screw conveyor. RICHi. Retrieved on April 09th, 2021.