Tungsten Electrode is the center of TIG welding world.
This article will cover the following content:
- What Tungsten Electrode is and its basic function.
- Exploring many types of Tungsten Electrode.
- Learning about six fundamental features of Tungsten Electrode.
- Some safety recommendations for using Tungsten Electrode during TIG welding.
Let’s join us on this amazing journey, right NOW!
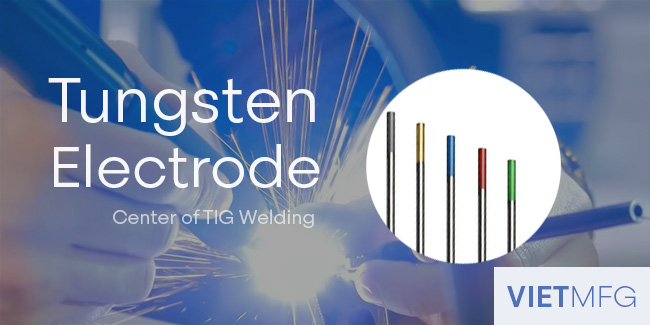
Basic information about Tungsten Electrode
1. What is Tungsten Electrode?
Tungsten Electrode is a critical component used to create an arc in TIG welding.
Sticking out of your TIG Torch, this electrode is made from Tungsten (same material as in your light bulb), with the highest melting point at 3,410 degrees Celsius (6,170 degrees Fahrenheit).
Thanks to this high melting point, Tungsten Electrode is not consumed during welding, and thus is called Non-consumable Electrode.
However, despite not being consumed, tungsten electrodes can have some erosion, which is called “burn-off”.
Electrodes can have either a clean finish or a ground finish:
- Clean finish: refers to the use of chemicals to clean the electrodes.
- Ground finish: refers to electrodes that have been ground to a uniform size to optimize their heat conduction.
2. Basic function of Tungsten Electrode
The basic function of Tungsten Electrode is to create an electric arc to your workpiece.
In other words, Tungsten Electrode serves as a terminal for the electric arc.
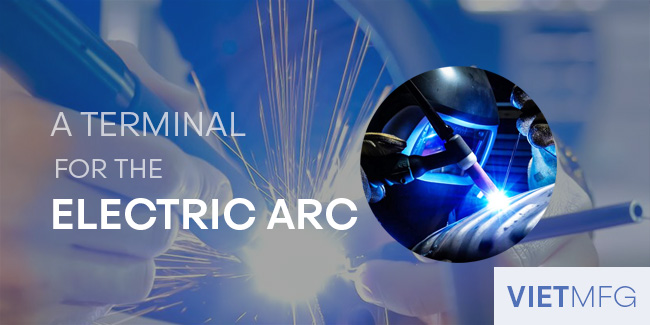
3. Can Tungsten Electrode be used in other welding processes?
Yes!
Besides TIG welding, Tungsten Electrode can be used in Plasma Arc Welding (PAW), Manual Arc Welding (MAW).
In these cases, Tungsten Electrode still plays the same role like that in TIG welding.
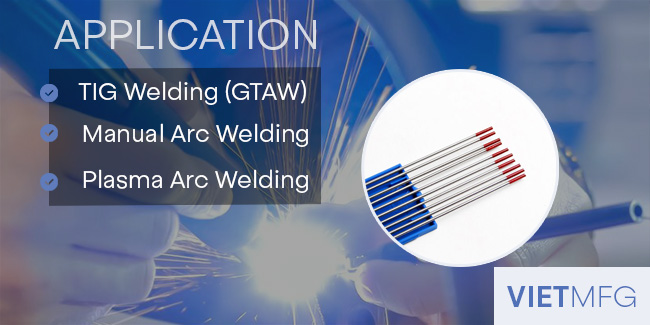
Understanding different types of Tungsten Electrode
Tungsten Electrode comes with many different types, with various sizes and characteristics.
For easy classification, each type of Tungsten Electrode is labeled with a unique color.
We will discuss the Tungsten Electrode Color Chart later in this article.
For now, in this section, we will analyze the 05 most common types of Tungsten Electrode:
- Pure Tungsten Electrode (GREEN)
- Thoriated Tungsten Electrode (YELLOW, RED)
- Ceriated Tungsten Electrode (ORANGE)
- Lanthanated Tungsten Electrode (BLACK, BLUE, GOLD)
- Zirconiated Tungsten Electrode (BROWN)
1. Pure Tungsten Electrode (GREEN)
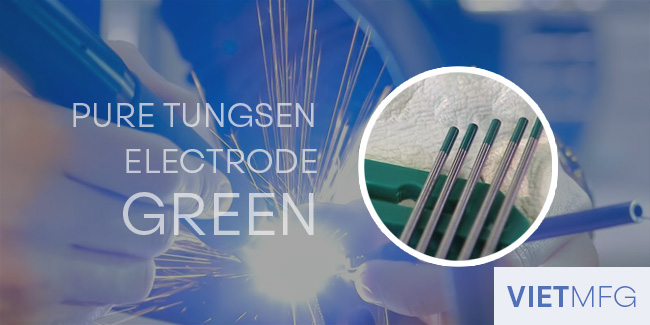
1.1 Composition of Pure Tungsten Electrode
Pure tungsten electrodes (AWS classification EWP) contain 99.5 – 99.7 percent tungsten, with no additional alloying elements.
1.2 Advantages of Pure Tungsten Electrode
Such tungsten electrodes are super durable and conductive, thanks to the benefits of tungsten itself.
Their price is also very affordable, compared with other electrode types.
1.3 Disadvantages of Pure Tungsten Electrode
However, it is more difficult to create a stable arc than other electrode types, because of extremely high work function (this term will be discussed in the following section).
1.4 Current Settings for Pure Tungsten Electrode
Pure tungsten electrodes are built specifically for AC welding with a balanced wave, and are ideal for TIG welding aluminum and magnesium alloys.
2. Thoriated Tungsten Electrode (YELLOW, RED)
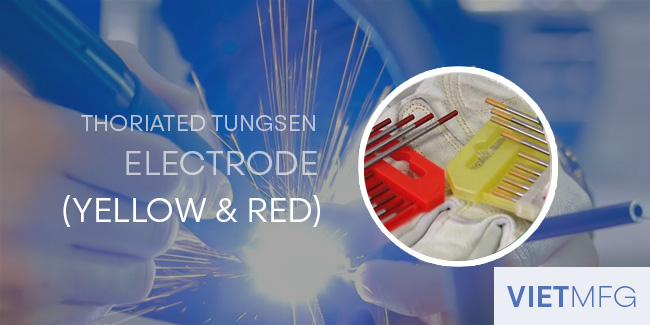
2.1 Composition of Thoriated Tungsten Electrode
Thoriated Tungsten Electrode contains thorium oxide (ThO2 or thoria) which is the most widely used tungsten electrode in the United States.
This electrode type is referred to as the standard of all electrodes.
Thus, it can be applied for many applications, including TIG Welding of Cast Iron, Brass, Mild Steel, etc.
2.2 Classification of Thoriated Tungsten Electrode
Based on the proportion of Thoria, there are two sub-types of Thoriated Tungsten Electrode available:
- The 1 percent Thoriated type (EWTh-1; YELLOW).
- The 2 percent Thoriated type (EWTh-2; RED).
Between the two, red tungsten electrodes are more commonly used.
2.3 Advantages of Thoriated Tungsten Electrode
Thoriated tungsten electrode is preferred for its durability, ease of use, and better resistance to weld pollution.
Moreover, this electrode type improves arc starts and can operate at high current ranges.
2.4 Disadvantages of Thoriated Tungsten Electrode
Thorium is radioactive, which can be harmful to fabricators.
However, the radioactive degree is low.
The main threat lies in the chance fabricators inhaling the Thorium dust.
Thus, we must follow the manufacturer’s alerts, directions and the Material Safety Data Sheet (MSDS) for use.
Also, install a suitable ventilation system in your workplace to clean thorium dust.
2.5 Current Settings for Thoriated Tungsten Electrode
Unlike Pure Tungsten Electrode, Thoriated Electrodes are used mainly for DC welding applications, especially the RED Tungsten Electrode.
With DC settings, Thoriated Electrodes are perfect for copper alloys, nickel alloys, titanium alloys, and non-corrosive steels.
However, they can also run on AC settings for welding thin aluminum (less than 0.6 inch) as well.
3. Ceriated Tungsten Electrode (ORANGE)
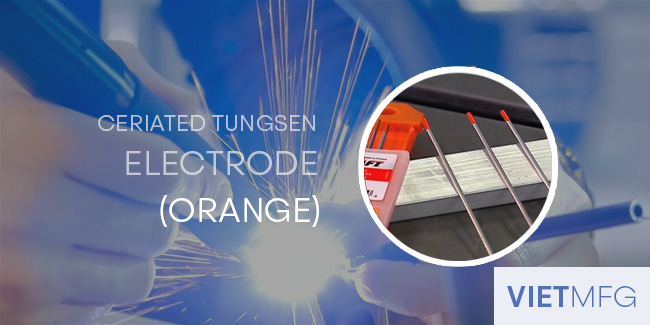
3.1 Composition of Ceriated Tungsten Electrode
Ceriated Tungsten Electrode (AWS classification EWCe-2) contains at least 97.3 percent tungsten, and about 2 percent cerium.
Thus, it is also called “2 percent ceriated” and is labeled ORANGE (AWS).
However, under ISO standard, Ceriated Tungsten Electrode is colored GREY.
3.2 Advantages of Ceriated Tungsten Electrode
Ceriated Tungsten Electrode runs well at lower amperages and provides excellent arc starts.
Higher ceria content in the electrode also helps reduce the burn-off rate.
Thanks to these advantages, Ceriated Tungsten Electrode is applied commonly in orbital tube and pipe fabricating; and some projects involving thin, delicate parts.
It is best to use Ceriated Tungsten to TIG weld stainless steel, nickel alloys and titanium.
In certain cases, Ceriated Tungsten is an ideal replacement for Thoriated.
3.3 Disadvantages of Ceriated Tungsten Electrode
However, Ceriated Tungsten Electrode does NOT perform well at higher amperages.
Higher current ranges cause the Cerium Oxide to migrate very quickly to the heat at the electrode tip, and thus remove the oxide content.
3.4 Current Settings for Ceriated Tungsten Electrode
Ceriated Tungsten Electrode works best in DC welding at low current ranges.
It is also possible to use this electrode type in AC welding, especially with the enhanced square wave power sources.
However, be aware that it may split when using with AC settings.
4. Lanthanated Tungsten Electrode (BLACK, GOLD, BLUE)
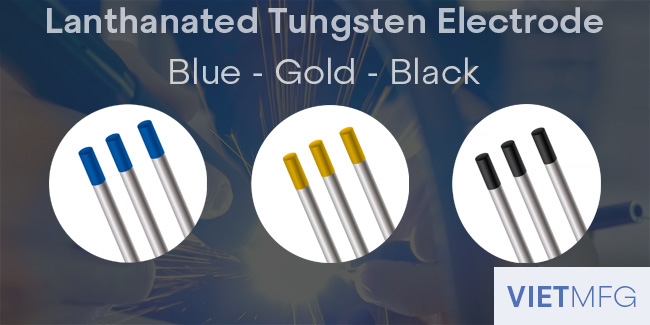
4.1 Composition of Lanthanated Tungsten Electrode
Lanthanated tungsten electrode contains a minimum of 97.80 percent tungsten, and about 2 percent lanthanum (La2O3).
4.2 Classification of Lanthanated Tungsten Electrode
Based on the proportion of Lanthanum, there are three sub-types of Lanthanated Tungsten Electrode available:
- The 1 percent Lanthanated type (EWLa-1; BLACK)
- The 1.5 percent Lanthanated type (EWLa-1.5; GOLD).
- The 2 percent Lanthanated type (EWLa-2; BLUE).
Among the three sub-types, the BLUE tungsten electrode (2 percent Lanthanated type) is most widely used.
4.3 Advantages of Lanthanated Tungsten Electrode
Lanthanated Tungsten Electrode has very low work function (the LOWEST actually) and thus is very easy in starting an arc.
Also, Lanthanated tungsten is very durable, acquires a low burn-off rate and excellent re-ignition feature.
Just like Ceriated Tungsten Electrode, Lanthanated type is NOT radioactive either. Hence, it is safer, and acts as a great substitution for Thoriated Tungsten Electrode.
Lanthanated Tungsten Electrode is best for TIG welding titanium alloys, copper alloys, nickel alloys, and stainless steel.
4.4 Disadvantages of Lanthanated Tungsten Electrode
Lanthanated Tungsten Electrode can be more expensive than Thoriated, and is not widely available at many fab shops.
Moreover, Lanthanated Tungsten Electrode is harder, and thus is more difficult to grind (sharpen) it.
4.5 Current Settings for Lanthanated Tungsten Electrode
Lanthanated Tungsten Electrode runs well on both AC and DC with a pointed end.
For AC sine wave power sources, Lanthanated Tungsten Electrode can be balled.
5. Zirconiated Tungsten Electrode (BROWN)
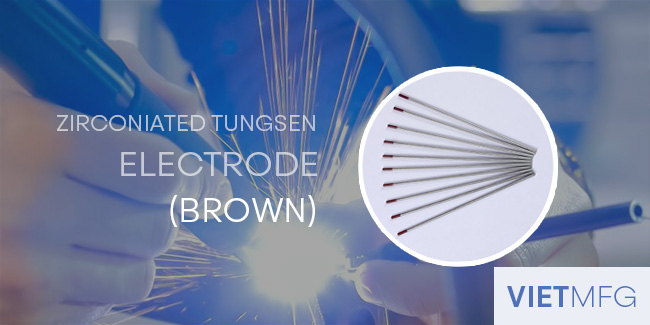
5.1 Composition of Zirconiated Tungsten Electrode
Zirconiated Tungsten Electrode contains a minimum of 99.10 percent tungsten, and about 0.15 to 0.4 percent zirconium.
5.2 Advantages of Zirconiated Tungsten Electrode
Zirconiated Tungsten Electrode produces an extremely stable arc and resists tungsten spitting during operation.
Its current-carrying capability is even higher than that of Thoriated Tungsten Electrode.
5.3 Disadvantages of Zirconiated Tungsten Electrode
One weak point of Zirconiated Electrode is that it cannot be applied for DC applications.
5.4 Current Settings for Lanthanated Tungsten Electrode
Zirconiated tungsten is best for AC welding, since it maintains a balled tip and has a high resistance to contamination.
It is also capable of handling higher current ranges for magnesium and aluminum alloys.
6. Other types of tungsten electrode
Besides the five materials mentioned above, there are other less common options, such as 1% Thoriated, 4% Thoriated, 2% Yttriated, and also mixes of different oxides in the same tungsten (rare earth mix).
Different material proportions exhibit unique results, including a stable arc in both AC and DC settings, greater service life, the ability to use a smaller-diameter electrode for the same job, the use of a higher current for a similar-sized electrode, and reduce tungsten spitting.
Key features of Tungsten Electrode
In this section, we will look at six key features of a quality Tungsten Electrode, including:
- Diameters and Lengths
- Current Ranges
- Color Code
- Electron Work Function (eV)
- Oxide Density
- Migration and Evaporation Rate
1. Tungsten Electrode Sizes
Tungsten Electrode Sizes are defined by 2 variables: Diameters and Lengths.
The following table shows the most commonly used Diameters and Lengths of Tungsten Electrode:
DIAMETERS (inches) | LENGTHS (inches) |
0.010 | 3 |
0.020 | 6 |
0.040 | 7 |
0.062 (1/16) | 18 |
0.093 (3/32) | 24 |
0.125 (1/8) | |
0.156 (5/32) | |
0.187 (3/16) | |
0.250 (1/4) |
The most common diameters include 0.020’’ (0.5mm) and 0.250’’ (0.5mm).
The most typical length of tungsten electrode is 7’’ (175mm).
Selecting the proper size of tungsten electrode is important, as the right choice will enhance the quality of your workpiece.
- If you are welding on thinner material at lower amperages, use a smaller diameter tungsten (less than 3/32’’).
- If you are welding on thicker material at higher amperages, use a larger diameter tungsten (more than 3/32’’).
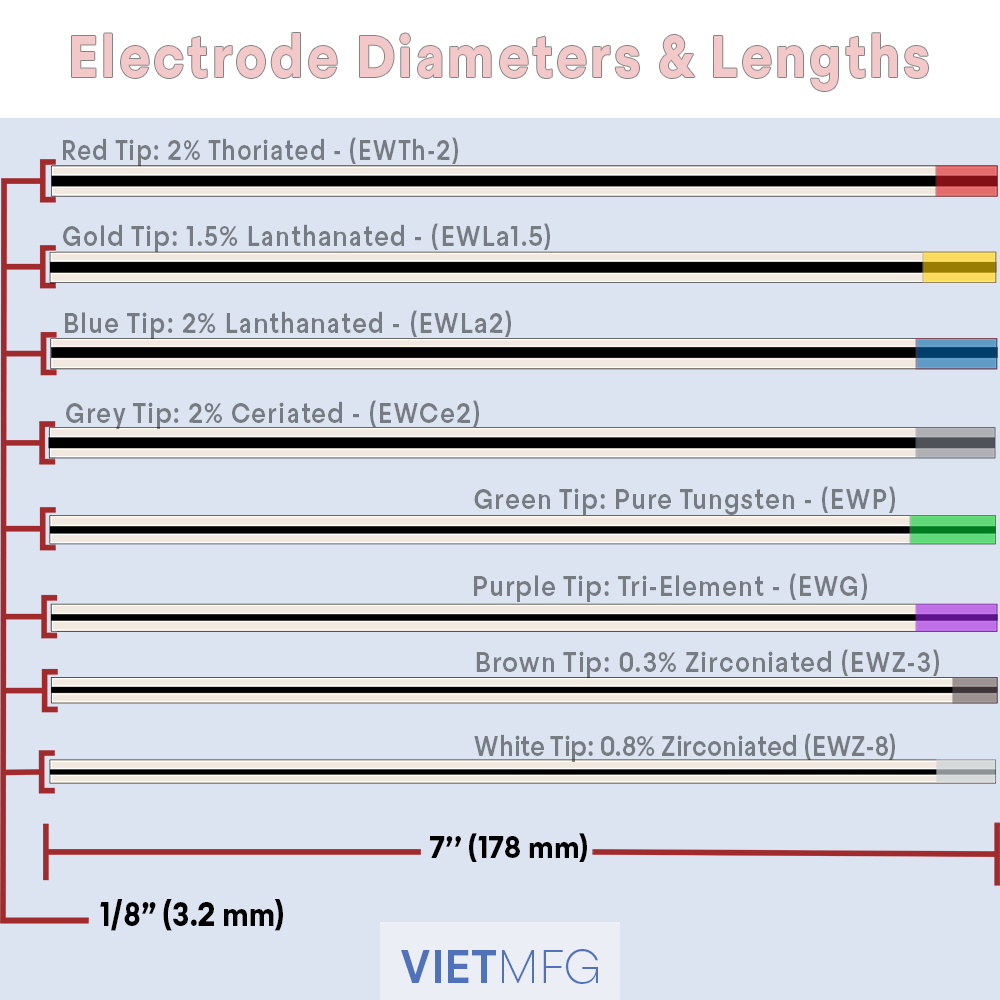
2. Tungsten Electrode Current Ranges
The following table is made by the American Welding Society (AWS), exhibiting the typical current ranges for Tungsten Electrode with DC and AC settings.
Please note that all data are based on using Pure Argon as the TIG welding gas.
The application of other shielding gases will change the current settings as well.
Thus, the AWS table should be used as a general guide only.

Too high current range can possibly melt the electrode and contaminate the weld puddle.
However, too low current range leads to unstable arc.
3. Tungsten Electrode Color Chart
After exploring different types of Tungsten Electrode, you may notice each type is labeled with a distinct color for easy recognition.
This color code is applied to one end of the electrode.
Below is the official Tungsten Electrode Color Chart, based on AWS standard.
AWS Classification | Defined | Color |
EWP | Pure Tungsten | GREEN |
EWCe-2 | 2% Ceria | ORANGE |
EWLa-1 | 1% Lanthanum | BLACK |
EWLa-1.5 | 1.5% Lanthanum | GOLD |
EWLa-2 | 2% Lanthanum | BLUE |
EWTh-1 | 1% Thoria | YELLOW |
EWTh-2 | 2% Thoria | RED |
EWZr-1 | 0.15 – 0.4% Zirconia | BROWN |
How to read the AWS Classification?
The AWS Classification of each electrode type comprises 04 main parts:
Parts | Letter | Meaning |
FIRST part | E | Stands for Electrode. |
SECOND part | W | Stands for Tungsten, the main composition of electrodes. |
THIRD part | P – Pure Ce – Ceriated La – Lanthanated Th – Thoriated Zr – Zirconiated | Stands for the additional oxide of tungsten electrodes: |
LAST PART | 1 – 1 percent 1.5 – 1.5 percent 2 – 2 percent | Stands for the weight-percent of the additional oxide |
For example, EWTh-2 is a thoriated tungsten electrode containing 2 weight-percent of thoria.
4. Electron Work Function (eV)
Firstly, let’s define what Electron Work Function means.
4.1 What is Electron Work Function?
Electron Work Function is the amount of energy required to detach an electron from an atom.
It is measured in electron volts (eV).
Usually, we look at eV on Oxide level, and on Metal level:
- Oxide eV: relates to the ability to start an arc. Lower Oxide eV means it is easier to start an arc.
- Metal eV: relates to the durability of the electrode. Lower Metal eV means the electrode is more durable.
4.2 What happens when Electron Work Function increases/ decreases?
Electron Work Function is closely related with the tungsten’s ability of striking an arc:
The lower the Electron Work Function, the lower the voltage necessary for an electrode to strike an arc.
Thus, it is BETTER to lower the Work Function of the electrode.
4.3 How to lower Electron Work Function?
Electron Work Function can be lowered through the addition of certain oxides to a tungsten electrode.
The following table names some oxides that can help lower Electron Work Function:
Material | Oxide eV | Metal eV |
Lanthanum | 2.50 | 3.30 |
Thorium | 2.60 | 3.35 |
Cerium | 3.20 | 2.84 |
Pure Tungsten | No oxide present | 4.50 |
In short, a tungsten electrode containing high levels of oxide will have lower Electron Work Function, and thus can strike an arc more easily.
For example, a Blue tungsten electrode (2 percent Lanthanated) will strike an arc more easily than a Black tungsten electrode (1 percent Lanthanated).
5. Oxide Density
Oxide Density refers to the weight of oxide per unit volume of a tungsten electrode.
Thus, a 2 percent by weight of Lanthanum, Cerium or Thorium will all have different amounts of oxides by volume.
The following table illustrates the difference between weight and density for different materials:
Material | Density (g/cm3) | Volume (%) of 2% by weight electrode |
Lanthanum | 6.15 | 5.70 |
Thorium | 11.72 | 3.80 |
Cerium | 6.65 | 5.20 |
6. Migration and Evaporation Rate
Migration rate (diffusion rate) is the rate at which the oxides travel from inside the tungsten to the heat at the electrode tip.
Evaporation rate is the rate at which the oxides separate from their metal component and are emitted at the electrode tip.
The tungsten electrode performs best when it has a good balance between migration and evaporation rate.
If the migration rate is slower than the evaporation rate, there will be a shortage of oxides arriving at the electrode tip to maintain a consistent arc.
Then, the tungsten electrode may be reduced to the performance level of pure tungsten.
On the contrary, if the evaporation rate is slower than the migration rate, the oxides will be crowded at the tip.
If both rates are very high, properties at the beginning of welding will be great. However, the oxides may be used up more quickly.
7. International Standards for Tungsten Electrode
Around the world, there are different published standards for different markets, such as the United States of America, Europe, Japan and Canada.
These standards regulate the dimensions and manufacturing requirements that tungsten electrodes must qualify.
Market | Published Standards |
The United States of America | American National Standards Institute/ American Welding Society A5.12 (ANSI/AWS A5.12) |
Japan | Japan Industrial Standards (JIS) |
Europe | The International Organization for Standardization 6848 (ISO 6848) |
Canada | American Society of Mechanical Engineers/ SFA (ASME/SFA) |
Tungsten Electrode Preparation
Tungsten Electrode Preparation refers to the geometry shape of the electrode tip.
There are three choices for tungsten preparation: balled, pointed, and truncated.
1. Balled Tip
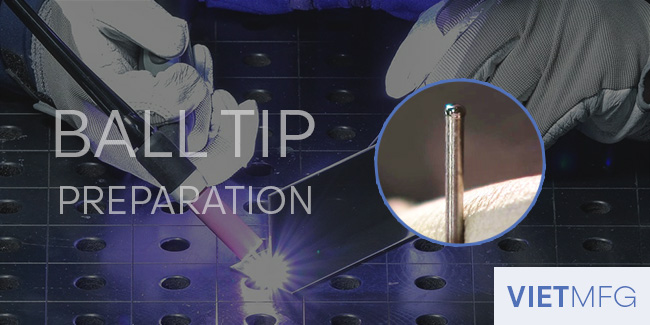
1.1 What is a tungsten electrode with a balled tip?
A balled tip has a shape similar to a ball (sphere) at the tip of the electrode.
This tungsten preparation is applied mainly on Pure Tungsten and Zirconiated Electrodes.
Recommended current settings for balled tip tungsten is AC, both on sine wave and conventional square wave.
To form a ball at the electrode tip, a good use of AC amperage and a suitable electrode diameter is highly suggested.
1.2 Advantages of balled tip preparation
Using a balled tip preparation helps fabricators perform TIG welding at higher amperages.
This tungsten preparation also provides better weld penetration and longer service life.
1.3 Disadvantages of balled tip preparation
Tungsten with balled tips can contaminate the weld, as too big the ball shape can fall off.
Also, this preparation can make it more difficult to start an arc, and reduce arc stability.
2. Pointed Tip
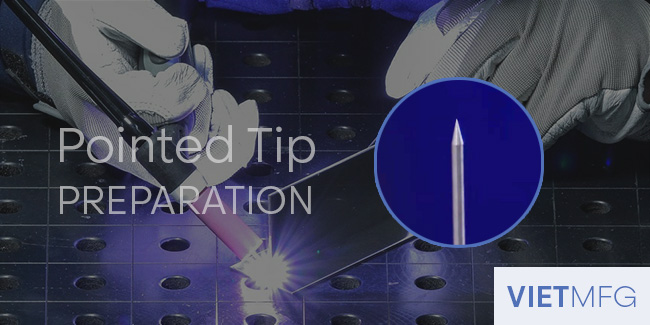
2.1 What is a tungsten electrode with a pointed tip?
A pointed tip has a sharp shape (like a spear) located at the electrode tip.
Tungsten Electrodes with pointed tips are applied for many electrode types, including Pure Tungsten, Ceriated, Lanthanated and Thoriated ones.
Pointed tips can be used for both inverter AC and DC welding processes, under lower amperages.
To achieve this spear-shaped tip, fabricators often use grinding machines, and grind the electrode tip to a conical shape.
Grinding electrode tips is a complex work, requiring to select a proper geometry and the correct grinding angle, in order to obtain the best performance.
2.2 Advantages of pointed tip preparation
A pointed tip helps create a more focused arc for better welding operation.
It also enhances the arc stability and provides easier arc starting.
2.3 Disadvantages of pointed tip preparation
Pointed tip preparation will shorten electrode life.
Also, it provides less weld penetration.
And more special note, it is highly NOT recommended to use pointed preparation for high current applications.
3. Truncated Tip
A Truncated tip is similar to the Pointed tip preparation, except for the spear-shaped tip being cut off.
By cutting off the sharp tip, the truncated tip helps fabricators to perform TIG welding at higher application without using the balled preparation.
A truncated shape prevents the high current from destroying the tip, which can contaminate the weld puddle.
Other properties of truncated tip are similar to that of Pointed tip preparation.
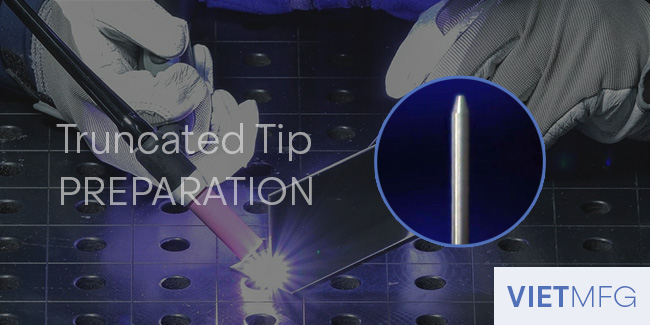
How to sharpen Tungsten Electrode?
After learning about three types of tungsten preparation, we know that Pointed and Truncated Tips are optimal for TIG welding.
This part will cover how to sharpen tungsten electrodes, by discussing necessary equipment and grinding technique.
1. Tungsten Grinder
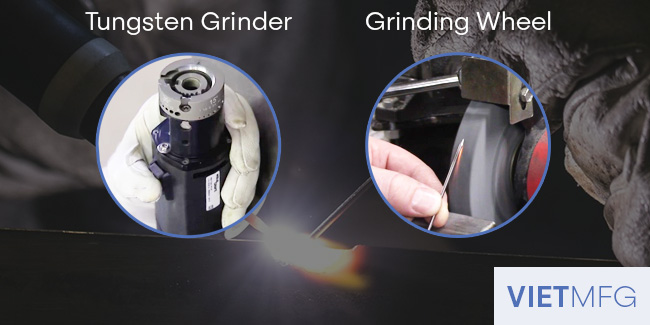
To grind a tungsten electrode, fabricators’ top choice is a specialized Tungsten Grinder.
However, in some cases, a diamond wheel is also suitable, as diamond’s hardness exceeds that of tungsten and thus provides a smooth grinding as well.
Please note that, whatever you choose, use it ONLY for grinding tungsten.
Do NOT grind other materials, as it can contaminate your tungsten and your weld puddle later on.
2. Tungsten Electrode Sharpening Technique
A proper sharpening is one that prevents the Tungsten from being too pointed but not too blunt.
We will look at tungsten electrode sharpening process from three different tasks:
- Tip (Flat) Preparation
- Angle (Taper) Grinding
- Cutting to Length
2.1 Tungsten Electrode Tip (Flat) Preparation
Tip Preparation is applied for a new electrode, or an electrode with its contaminated tip being cut off.
To do this, simply push the tungsten electrode to the side of the wheel at exactly 90 degree angle.
You should use an equipment to hold the electrode, so that the angle is maintained.
2.2 Angle (Taper) Grinding
While grinding with a diamond wheel, there are two options: to grind crosswise, or to grind lengthwise.
Please be aware that tungsten electrodes must be ground lengthwise.
This is because of the molecular structure of tungsten electrodes with grain running lengthwise, so grinding crosswise is similar to “grinding against the grain”.
Grinding lengthwise is the correct technique, which helps the electrode to strike an arc more focused and stable.
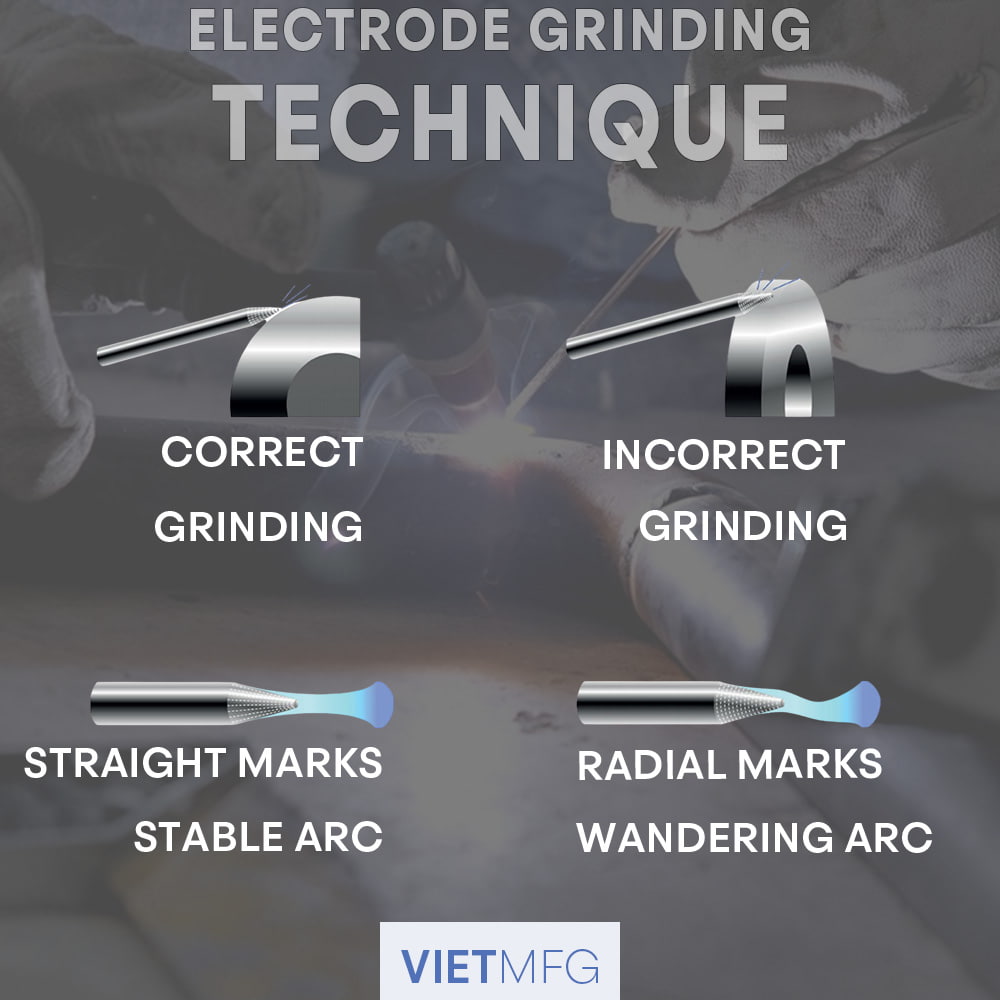
2.3 Cutting to Length
Cutting to length is one of the most overlooked processes of preparing a tungsten electrode.
Not only refers to cutting the tungsten to a specific size, cutting to length also means the removal of contaminated electrode tips.
NEVER use wire cutters or pliers to cut tungsten, as the electrode can be shattered and cause harmful injury to hands or eyes of fabricators.
Only use diamond grinding wheels to cut tungsten, and maintain a cutting angle at 90 degree to ensure a clean and smooth cut.
Also, the grinding wheels must have a scale to ensure the exact cutting length for fabricators.
Safety Recommendations
Every type of tungsten electrode contains heavy metal.
Thus, the use of electrodes represents certain risk to the users, especially the risk of breathing the tungsten dust, or the hand injury from manually grinding the electrode.
Therefore, always follow these safety standards when dealing with tungsten electrode:
- Equipped yourself with safety glasses.
- Loose clothing is not recommended as it can be caught in machines and moving parts.
- Wear protective hair covering and safety shoes.
- Install a proper ventilation system to remove tungsten and thorium dust from your workplace.
- When tired or under medication, never operate power tools.
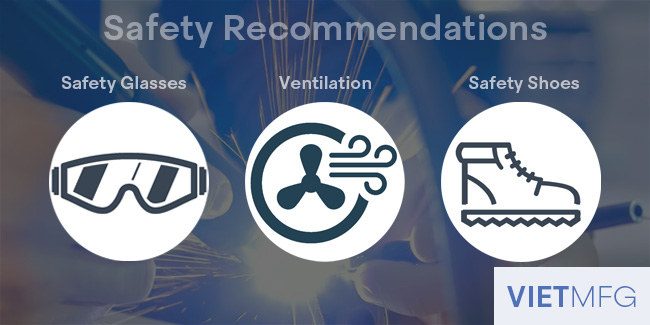
Conclusion
That’s it! Every fundamental thing about our little friend – tungsten electrode.
Please be aware that selecting a proper type and shape of tungsten electrode is very important.
A good selection will improve your arc quality and welding performances.
Whichever electrode type you select, whether you are using AC or DC settings, it is always crucial to choose your tungsten wisely for each welding application.
frequently asked questions for Tungsten Electrode.
Reference
- Welding Principles and Practices (5th Edition) – McGraw Hill Education. Edward R.Bohnart. [2017]
- Specification for Tungsten and Oxide Dispersed Tungsten Electrodes for Arc Welding and Cutting. American Welding Society (AWS). Retrieved 04 August 2020.
- Selection and Preparation Guide for Tungsten Electrodes. Miller. Retrieved 04 August 2020.
- TIG Welding Tungsten Electrode Selection Chart. Midwest Tungsten Service. Retrieved 05 August 2020.
- TIG Tungsten Electrodes. Midwest Tungsten Service. Retrieved 05 August 2020.
- Tungsten Electrode Guidebook. Diamond Ground Products. Retrieved 05 August 2020.
- TIG Welding Tungsten Selection | TIG Time. Weld.com (Youtube). Retrieved 06 August 2020.
- https://youtu.be/g4_iBmK8mhc. The Fabrication Series (Youtube). Retrieved 06 August 2020.