If you are looking for materials to build up your foundation knowledge on TIG Welding (also known as Gas Tungsten Arc Welding – GTAW), you have come to the right place.
This introductory content – TIG Welding 101 – is an easy-to-follow guide, which you can find extremely useful.
This article will open up a whole new world of TIG Welding in the simplest way, including:
- What is TIG Welding?
- When is TIG Welding applied?
- Pros and Cons of using TIG Welding.
- An A-Z list of terms of TIG Welding (special!)
Alright! Let’s start now!
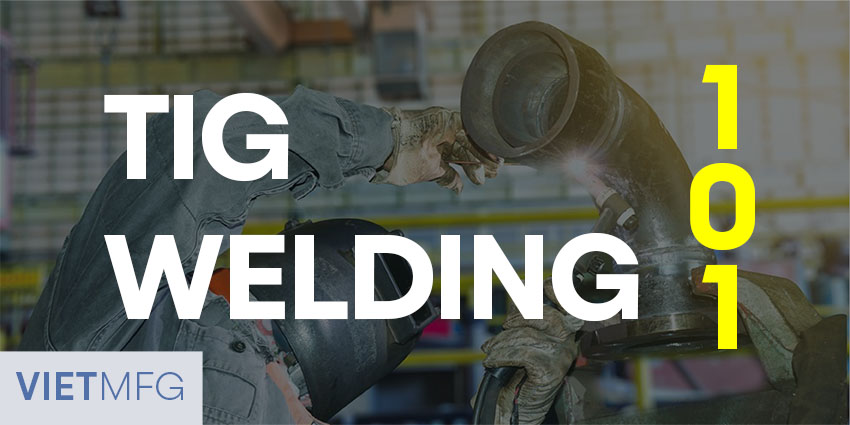
What is TIG Welding?
TIG Welding is a welding process that uses a tungsten electrode to heat the workpieces and join them together, under the protection of inert gases and/or the support of filler wire.
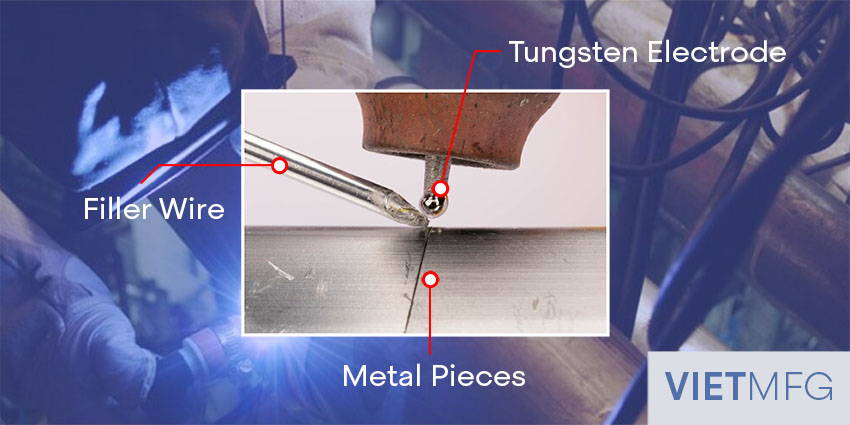
The process has many other names, including:
- Gas Tungsten Arc Welding (this name is used by American Welding Society – AWS)
- Heliarc
- Heliwelding
However, TIG is the most common name of all.
TIG means Tungsten Inert Gas, which sums up the two most important features of this welding process:
1. The use of Tungsten Electrode
Tungsten has a very high melting point, which would not be consumed into the weld pool during welding.
That is why Tungsten Electrode is often referred to as “non-consumable”, unlike many other processes (MIG, Stick, etc.) which requires a “consumable” electrode.
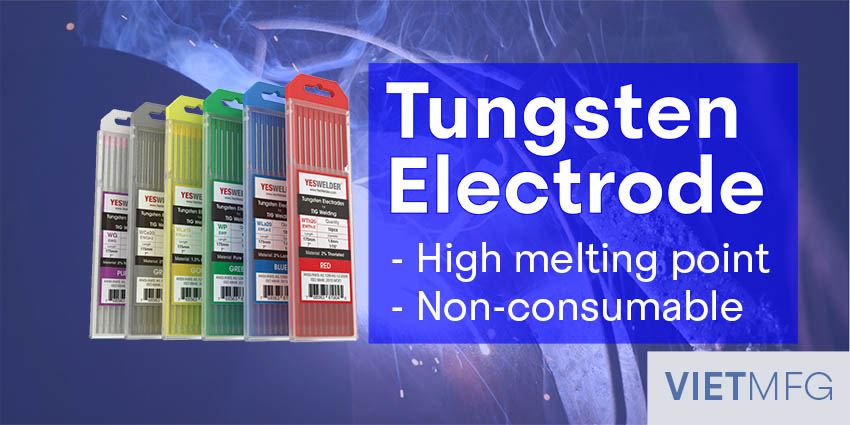
2. The protection of Inert Gas
Inert gas, such as Argon, Helium, or other gases, is used to cover the molten metal and tungsten electrode during and after the welding process.
It is also called shielding gas used for TIG Welding.
The reason for shielding gas use is to prevent the molten metal and tungsten electrode from reacting with oxygen and water vapor in the atmosphere.
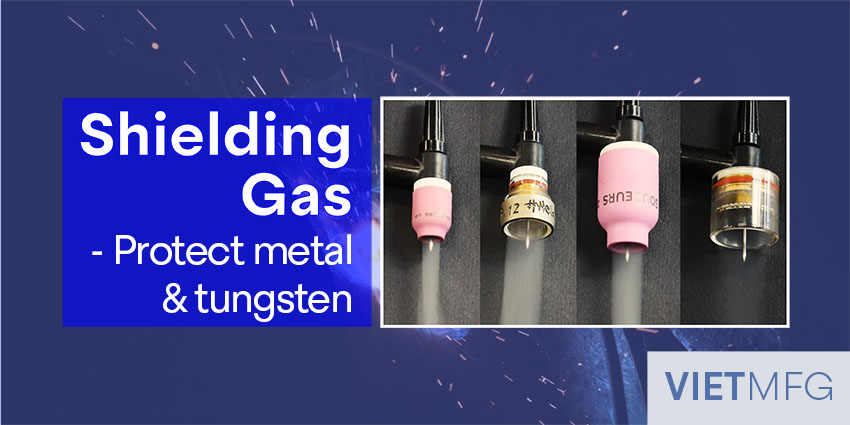
Two unique features of TIG Welding Process
1. Heat source coming from electric arc from tungsten electrode
The basic principle of welding is to heat the metal piece.
However, each welding process might have different ways to generate that heat.
In TIG Welding, the heat is initiated from the electric arc between the tungsten electrode and the workpiece.
The electric arc has a cone shape, with the base on the metal piece and the tip at the tungsten electrode.
- The closer your tungsten electrode is to the weld pool (or metal), the smaller the base of the cone becomes.
- And vice versa, the farther your tungsten electrode, the larger the base.
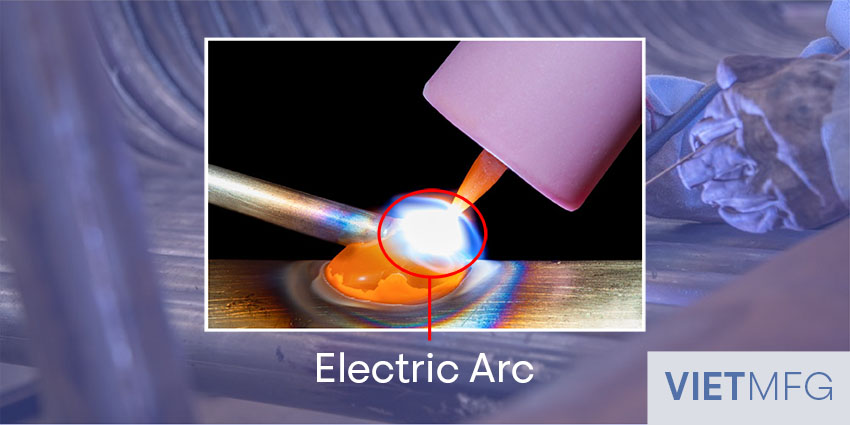
A smaller cone base is much more preferred, as TIG welding with a large base can leave a hold in your workpiece.
However, NEVER let your tungsten touch the weld pool.
If you let it happen, your tungsten will be contaminated and have to be resharpened before it can be used again.
Instead, maintain a proper distance between your tungsten and your metal (around 1/8″).
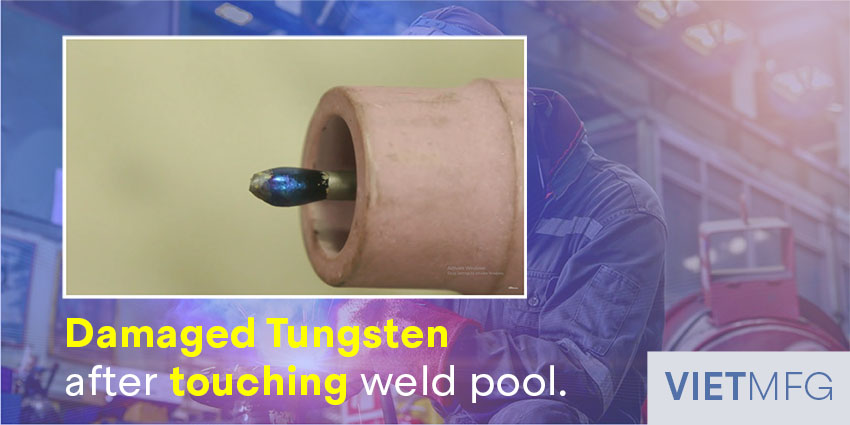
2. It is a two-handed job!
Unlike other welding processes, professional TIG welders always make good use of their two hands.
It is very much like playing the piano, with your left hand pressing the bass chords and your right hand doing the melody.
In TIG Welding, usually you will hold the TIG torch with your right hand, while the left hand is used to feed the filler wire.
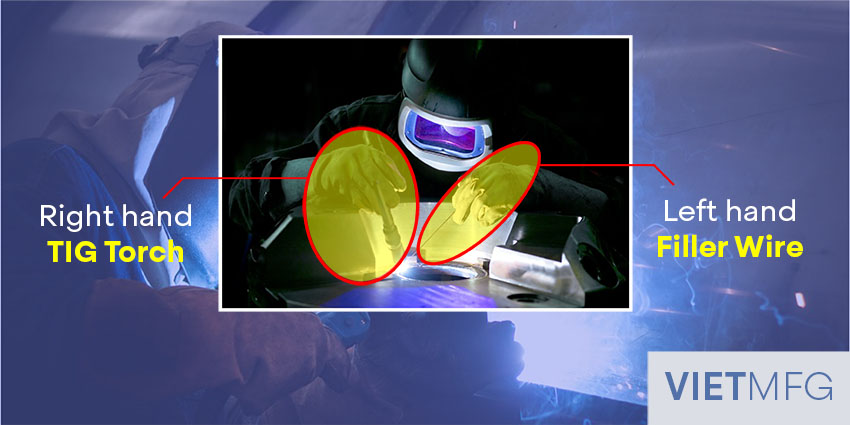
During the whole process, the two hands will do different movements, which is very confusing for beginners.
While the right hand (holding the TIG torch) has to move along the workpiece steadily and not allow the tungsten to touch the metal, the left hand (feeding the filler wire) has to dip and dap the rod constantly in the pool.
History background of TIG Welding
In the 1940s, a famous welder named Russell Meredith who worked for Northrop Aircraft Corporation (Southern California) invented the TIG welding process.
This technique is created due to the high demand for efficient welding of aluminum and magnesium alloys at the time.
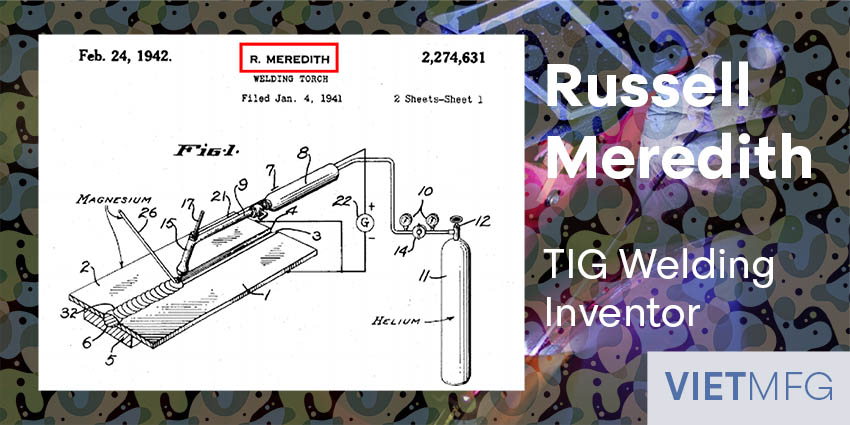
Fortunately, the invention was a big hit and gave a huge boost to many American industries, including aircraft, shipbuilding, etc.
This became an American pride when President Roosevelt bragged about it in a letter for Winston Churchill.
Thanks to its success, its patent was purchased by the Linde Division of Union Carbide.
After the patent expired in the 1970s, many companies started developing and selling TIG-related tools, such as TIG torches and accessories.
Many top companies at the time include CK Worldwide and Weldcraft.
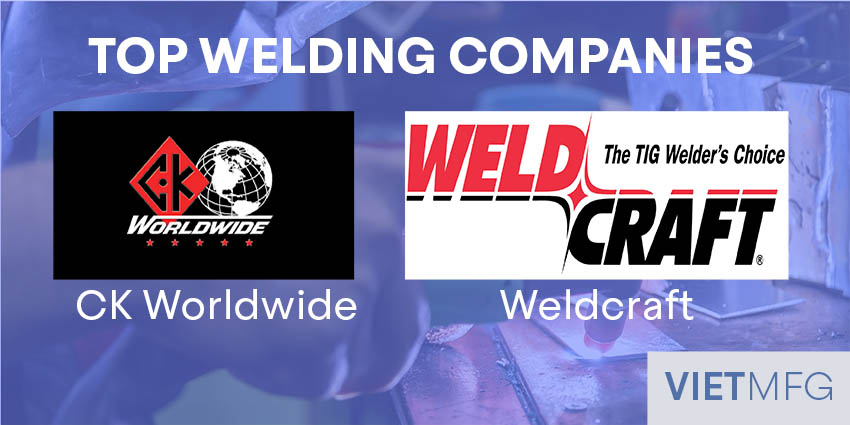
Why should we choose TIG Welding for our projects?
In spite of its difficulties, TIG welding can be an ideal option for many projects, thanks to the five following benefits:
1. TIG Welding can be applied for a majority of metals
TIG Welding can be applied to more metals than any other welding processes.
The metal list can go on and on, including stainless steel, aluminum, cast iron, copper, brass, magnesium, gold, etc.
Mainly, TIG is a useful technique for welding bike frames, door handles, fenders, wagons, etc.
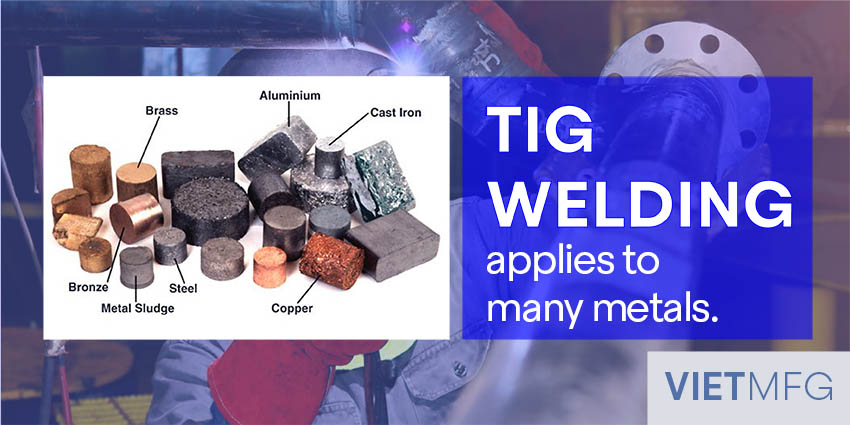
2. TIG Welding is an extremely precise technique
TIG Welding allows for excellent heat and weld puddle control.
This results in extremely precise and clean welds, and thus greatly enhances the appearance criteria of your project.
You may ask how can you control the heat in TIG Welding?
Well, it is all thanks to the foot pedal (or the thumb wheel) on your TIG torch.
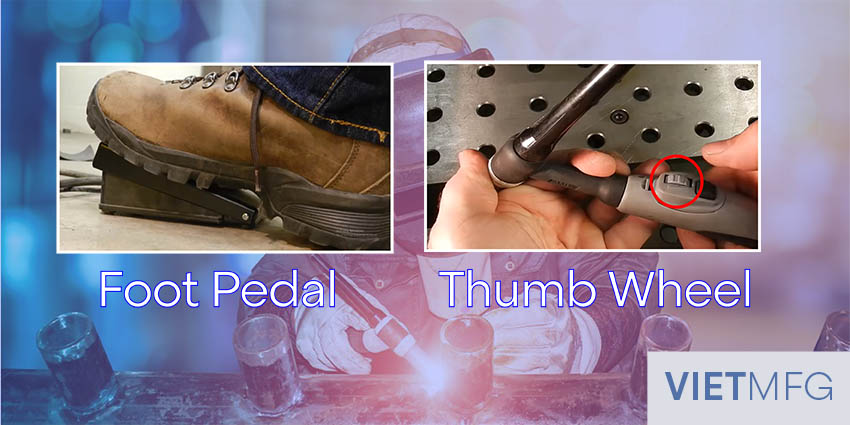
It is similar to driving a car, you can simply increase or reduce the heat by pressing the foot pedal.
This wonderful feature makes TIG a perfect choice for cosmetic welds (sculptures) and automotive welds.
3. TIG Welding creates very clean welds
TIG Welding creates no sparks or spatter during the process, thanks to the direct addition of filler rods into the weld puddle.
TIG also leaves no flux or slag, as the weld puddle is constantly shielded from contaminations in the atmosphere with inert gases (Argon, etc.)
This is very beneficial for TIG Welding Stainless Steel, as Stainless is a very unforgiving materials
Another thing is that no smoke or fume is produced in TIG welding, as long as the base metal is cleaned before the TIG performance.
4. TIG Welding has a one-size-fit-all shielding gas (Argon)
In TIG Welding, you can simply apply Argon for all your applications, regardless of what the base metals are.
So, no matter you are TIG Welding Cast Iron, or Brass, Mild Steel, Titanium, etc., you can always relay on a simple Argon tank as your shielding gas.
Thus, as a beginner, an advice is to prepare an Argon tank, and you are half ready for the job.
5. TIG Welding can be done in all positions
In addition to the high applicability (with many metals), TIG welding can also be carried out in all positions.
Some welding positions include flat, vertical, horizontal or overhead.
That is why TIG can be very useful for roll cages and inside confined areas.
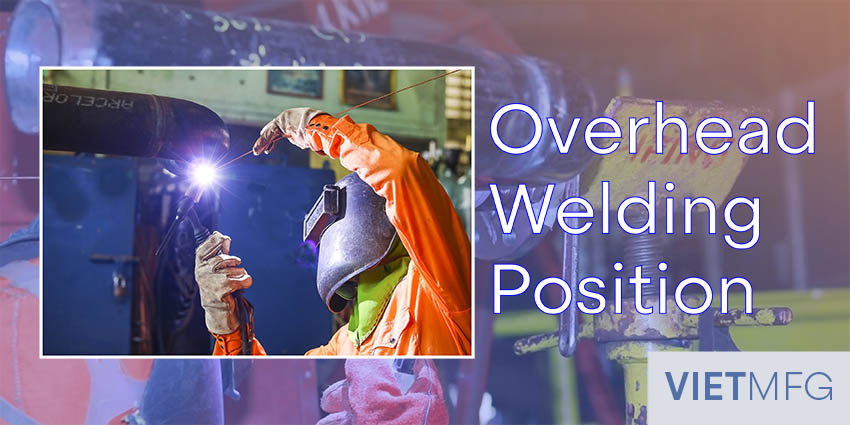
TIG Welding Application
Thanks to its high applicability, TIG Welding can be applied in the creation and repairment of many projects.
TIG Welding is especially common in automotive, aerospace, repair and art fields.
Below are some typical jobs using TIG Welding in common industries:
1. Aerospace
Many parts of an aircraft or spacecraft are joined by TIG Welding.
Thus, the next time you sit on a plane, or watch a movie about spaceships, you can be proud that these objects are strengthened by our friend TIG Welding.
2. Automotive
Automotive industry puts a huge emphasis on safety and secure criteria.
Thus, TIG welding is highly suggested for this particular industry.
TIG is proved to reduce corrosion over time, and so is frequently applied for car fenders to avoid rust.
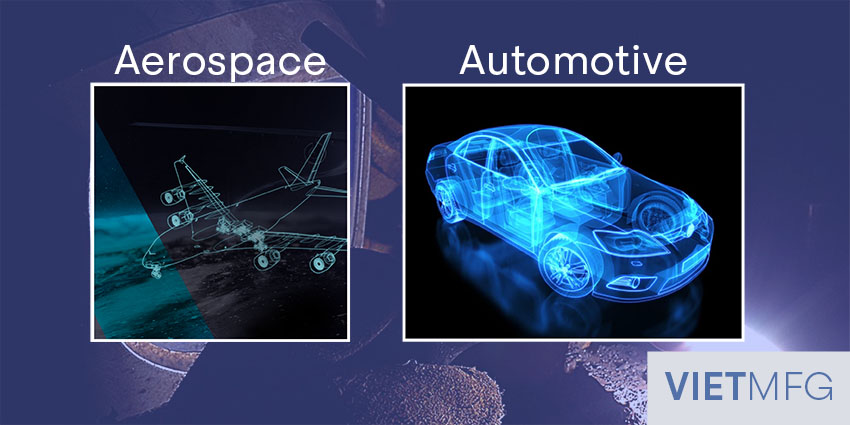
3. Repair
TIG Welding is famous for many fixing applications, from a child’s toy to aluminum and brass tools, etc.
4. Art
As TIG Welding provides very clean and precise welds, it is suitable for art projects which demand high appearance criteria.
For example, some artworks include industrial fixtures or metal sculptures, etc.
A-Z list of various concepts in TIG Welding
Arc Length
Refers to the distance between the tungsten electrode and the contact point on the workpiece.
Base Metal
Refers to the metal or alloy of your workpiece that you are TIG welding.
Crater
Refers to a defect located at the end of the weld, caused by either the sudden reduction in welding power or the removal of filler rods too quickly at the end of your application.

DCEN & DCEP
Refers to the two types of DC configurations:
- DCEN: the electrode is the negative pole and the workpiece is the positive pole.
- DCEP: the electrode is the positive pole and the workpiece is the negative pole.
Electrode Extension
Refers to the length of electrode extending beyond the end of the contact tube.
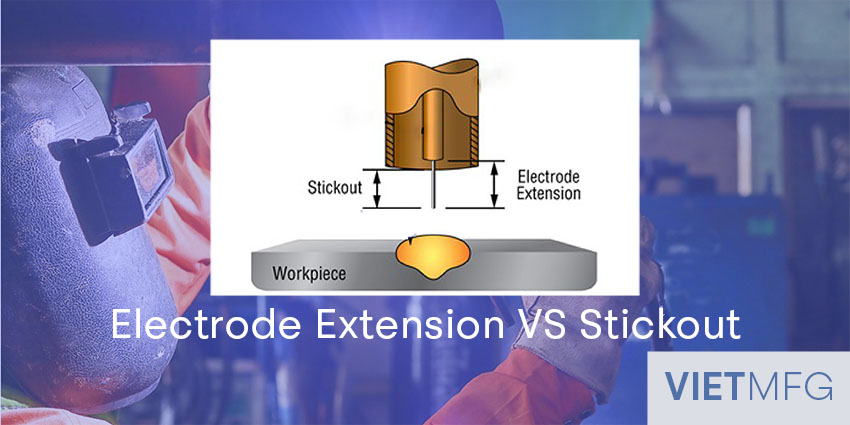
Filler Wire
Refers to the filler metal to be added in the weld pool during TIG process.
Filler material and diameter vary with the specific application.
Gas Nozzle
Refers to a device at the end of the TIG torch that directs the shielding gas.
High Frequency
Commonly applied to TIG welding, it refers to an alternating current consisting of over 50,000 cycles per second at high voltage and low amperage.
This function allows TIG welders to position the tungsten electrode near the workpiece, and simply press the torch trigger to start the arc.
Inert Gas
Refers to shielding gas, such as helium or argon, which does not chemically combine with other elements.
Such gas shields the welding arc and prevents the molten metal against contamination from the atmosphere.
Joint Type
Refers to the weld joint classification, based on five basic joint settings, such as a butt joint, corner joint, edge joint, lap joint, and T-joint
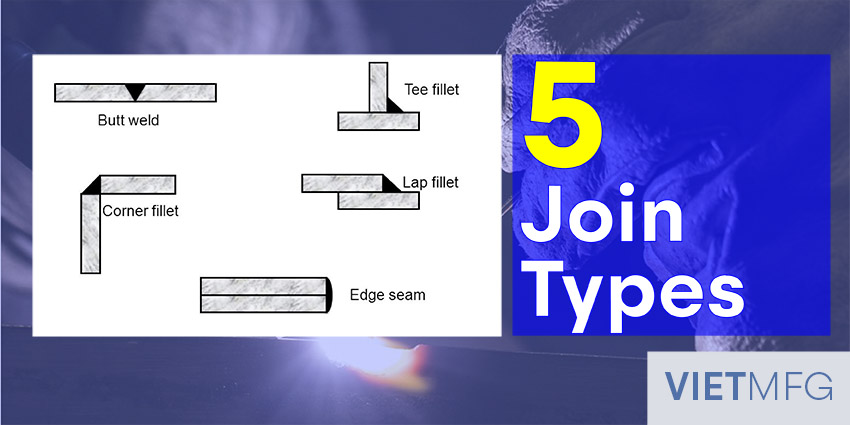
Lap Joint
Refers to one of the five joint types, which shows overlapping circles in parallel paths.
Melting Point
Refers to the temperature where the metal goes from solid state to liquid state.
Nozzle Diameter
Refers to the diameter of the nozzle through which the shielding gas flows through.
Out-of-Position Welds
Refers to welds made in positions other than flat or horizontal positions (overhead, etc).
Porosity
Refers to the scattered presence of gas pockets in your metal piece, resulting from poor gas shielding.
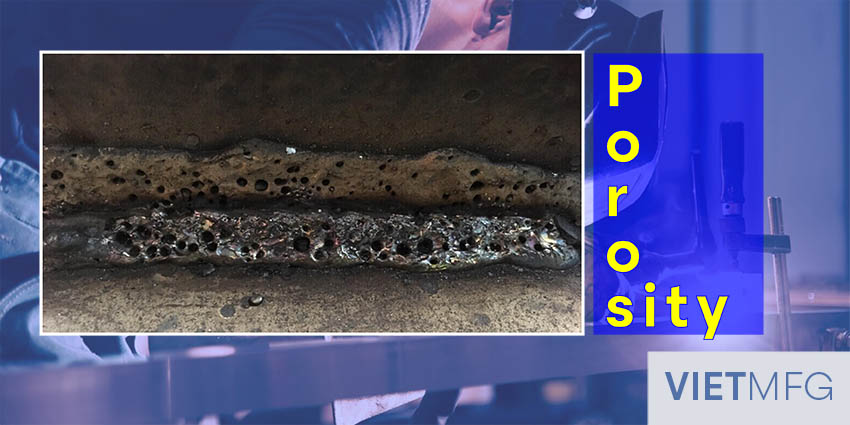
Reverse Polarity
Refers to DCEP, when the electrode is connected to the positive terminal and the workpiece is connected to the negative terminal of the welding power source.
Straight Polarity
Refers to DCEN, when the electrode is connected to the negative terminal and the work is connected to the positive terminal of the welding power source.
Stick-out
Refers to the length of electrode extending beyond the end of the gas nozzle.
Usually, the stick-out length should be the same as the gas nozzle diameter being used.
Tungsten Electrode
A non-consumable electrode made of tungsten, used mainly in TIG welding operations.
Besides TIG Welding, tungsten electrode is also applied in other processes, such as arc cutting and plasma spraying.
Uphill
Refers to welding with an upward progression.
Vertical Weld
Refers to the welding position in which the weld axis is approximately vertical and the weld face lies in an approximately vertical plane.
Weld Pool
Refers to the molten metal in a weld prior to its solidification as weld metal.
It is also called weld puddle.
X-RAY
Refers to a radiographic test method which helps detect internal defects in a weld.
Yield Strength
Refers to the stress point at which permanent deformation results.
Zirconium
Refers to an element used in some electrodes.
Zirconiated tungsten electrodes (BROWN) are used exclusively for AC settings in TIG Welding Aluminum.
Conclusion
That is the end for TIG Welding 101.
You have gone through every basic thing about TIG technique, as well as certain terms to get yourself more familiar with the welding process.
More in-depth topics are discussed in our other articles.
Read more at:
- TIG TORCH: THE #1 ULTIMATE GUIDE FOR BEGINNER (2020)
- The MOST UPDATED Handbook for TIG Welding Gas in 2020
- Tungsten Electrode: Journey to the Center of TIG Welding [2020]
- TIG WELDING STAINLESS STEEL: 15 BEST TIPS AND TRICKS FOR BEGINNERS [2020]
- A COMPLETE GUIDE ON HOW TO TIG WELDING ALUMINUM FOR BEGINNERS (2020)
- TUTORIAL ON TIG WELDING SPECIAL MATERIALS: CAST IRON, BRASS & MILD STEEL [2020]
Reference
- Welding Principles and Practices (5th Edition) – McGraw Hill Education. Edward R.Bohnart. [2017]
- What is Tungsten Inert Gas (GTAW or TIG) Welding? The Welding Institute (TWI). Retrieved 04 September 2020.
- Welding Tips: The Secret to Success When TIG Welding. Miller Welds. Retrieved 04 September 2020.
- TIG Welding Tips. Miller Welds. Retrieved 04 September 2020.
- The History of TIG Welding. Prime Weld. Retrieved 04 September 2020.
- TIG Welding Overview and Application. Tulsa Welding School (TWS). Retrieved 04 September 2020.