Have you ever received an order to do a weld repair on a piece of stainless steel? But you lack the strong TIG welder, as well as the budget to buy bulky external shielding gas for the project.
Well then, you should check out Flux Cored Welding stainless steel[1] . This article will give you some tips on how to perform flux cored welding stainless steel by covering the following content:
- The appropriate flux cored wires for flux cored welding stainless steel.
- The correct setting for flux cored welding stainless steel.
- Some tips and tricks in performing flux cored welding stainless steel.
Without further ado, let’s set the ball rolling!
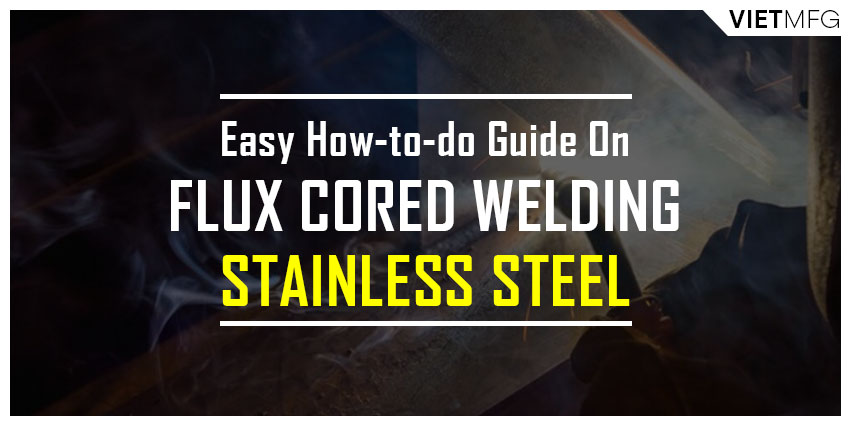
The Classic Advice For Welding Stainless Steel
I believe upon your research on welding stainless steel, the most preferable advice you will find is to utilize TIG or MIG welding for stainless steel.
This common advice means you will need solid stainless steel welding wires and external shielding gas, mainly the tri-mix of 90% Helium, 7.5% Argon and 2.5% CO2.
Don’t get me wrong! I mean, this is a great advice to follow.
However, there is one additional option which is more portable, and that is Flux Cored Welding Stainless Steel.
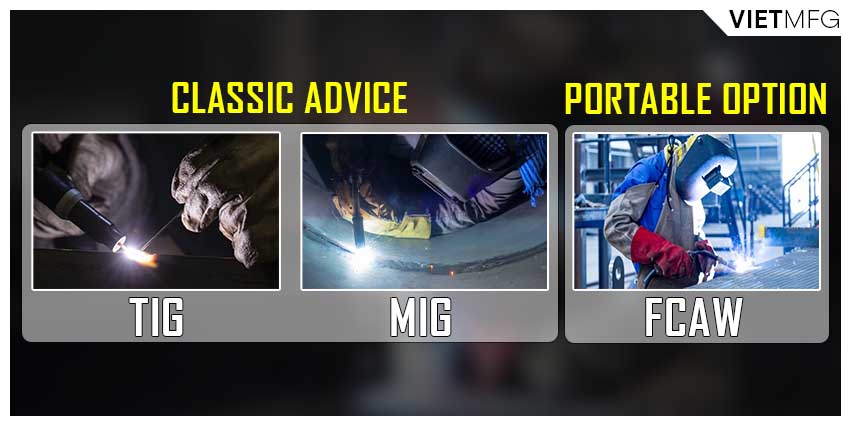
Suitable Welding Wires For Flux Cored Welding Stainless Steel
The general rule is to use a gasless stainless steel flux core wire[2] in Flux Cored Welding Stainless Steel. Depending on your stainless steel grade (series), you will choose a proper Flux Cored Stainless Steel Wire accordingly.
For example, if you are dealing with 308 base material, you should pick 308L welding wire to match the grade of your base metal. The letter “L” stands for low carbon, which helps prevent weld decay.
Fortunately, unlike the non-existence of wires used for flux cored welding aluminum[3] , we can actually find flux core wires for stainless steel.
One of the most reputed brands that produce these gasless stainless wires is Blue Demon. You can find their products available on Ebay and Amazon.
Three most commonly used items from Blue Demon are: Blue Demon 308LFC Gasless Stainless Steel Flux Cored, Blue Demon 309LFC Gasless Stainless Steel Flux Cored, and Blue Demon 316FC-O Gasless Stainless Steel Flux Cored.
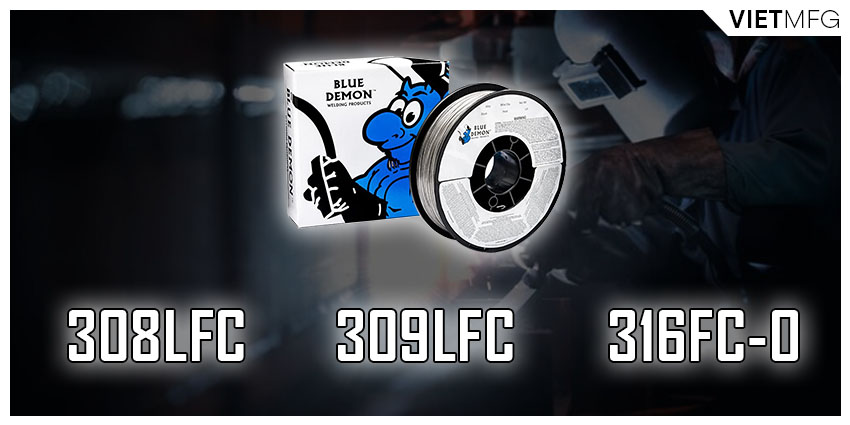
Table 01: Top 3 Blue Demon Gasless Stainless Steel Flux Core Wires
Blue Demon Items | Applicable Stainless Steel | Available Sizes | Recommended Output Current | Applicable Welding Position |
Blue Demon 308LFC | 300 to 308 series stainless steel, sometimes 430 stainless parts are applicable | 0.035 inch and 0.045 inch | 130 – 150 amperes | Flat and horizontal |
Blue Demon 309LFC | 300 to 309 series stainless steel, can weld stainless with mild steel. | 0.035 inch and 0.045 inch | 130 – 150 amperes | Flat and horizontal |
Blue Demon 316FC-O | 316 series stainless steel (food grade stainless) | 0.035 inch and 0.045 inch | 130 – 150 amperes | Flat and horizontal |
Configuring The Correct Polarity For Flux Cored Welding Stainless Steel
Getting the right polarity is very important for Flux Cored Welding Stainless Steel.
Always remember that flux cored stainless steel welding wires must go with DCEP polarity.
Don’t even try with DCEN, as it just won’t work.
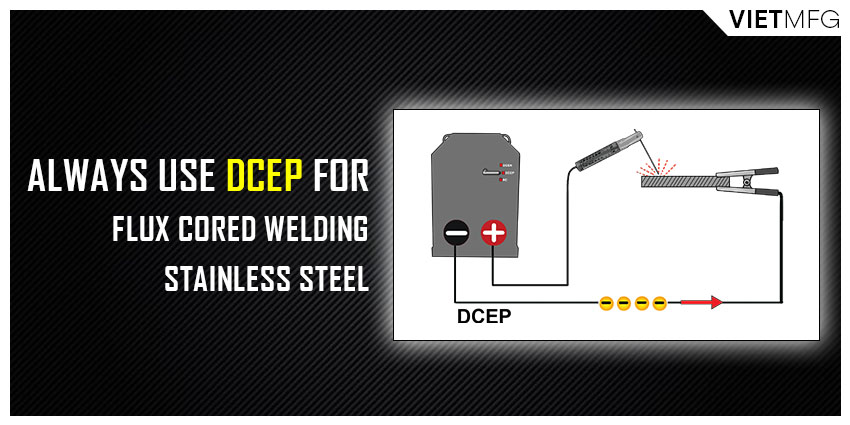
Pros And Cons Of Flux Cored Welding Stainless Steel
Let’s learn why Flux Cored Welding Stainless Steel is preferred and what its drawback is, before we go further.
1. Benefits Of Using FCAW On Stainless Steel
Flux Cored Arc Welding[4] on Stainless Steel is preferred among hobbyists who do not engage in stainless projects so often.
Hence, it is an economical method to deal with some small jobs relating to stainless steel.
Plus, you do not need to carry the bulky gas cylinders around like in TIG or MIG processes.
So, Flux Cored Welding Stainless Steel is more portable and can be performed outside in windy conditions.
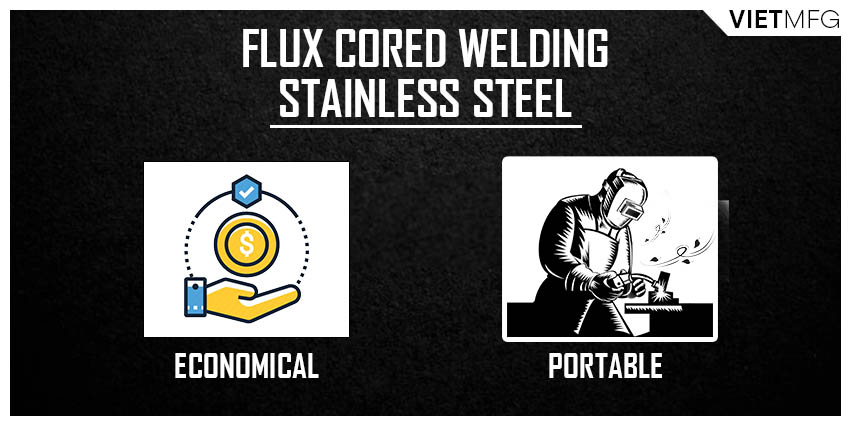
2. Drawbacks Of Using FCAW On Stainless Steel
It is quite challenging to find flux cored stainless steel wire that is applicable for out-of-position welding (vertical and overhead).
As I recommended above, all three products from Blue Demon are designed for flat and horizontal welding positions only.
This fact implies that Flux Cored Welding Stainless Steel is NOT an effective solution in dealing with exhaust pipe welding, because such a project requires the operators to weld in all positions.
Sometimes, flux Cored Welding Stainless Steel is not applicable in some really cheap flux cored welders[5] , as such machines cannot run on DCEP polarity.
The process certainly cannot produce a weld that is as strong and beautiful as TIG welding. Also, you can experience slag inclusion when using Flux Cored Welding Stainless Steel.
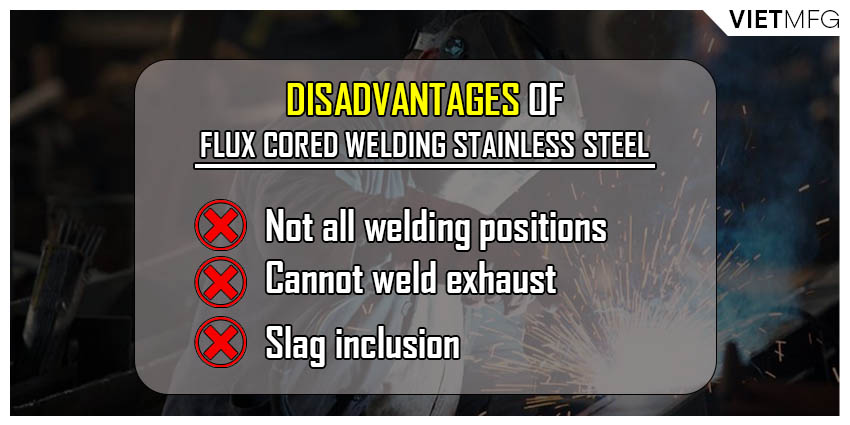
Testing Out Some Parameters On Flux Cored Welding Stainless Steel
With Flux Cored Welding Stainless Steel, what would happen when we change some basic welding settings? Let’s find out in this section.
1. Wire Feed Speed
When you set the wire feed speed too low, you will receive massive amounts of spatter.
However, if you use too much wire feed speed, you will have your flux cored wires stubbed.
2. Travel Speed
If you move your welding gun too slow, you will see that your slag cannot cover the weld pool well enough. Your bead will crown high, and the metal will turn gray. Porosity appears and the final weld would become rusty very easily.
On the other hand, too fast travel speed will make the weld bead become too narrow.
3. Contact Tip to Work Distance (CTWD)
When you maintain too short CTWD, you will get poor flux coverage because the flux would not be preheated enough. Then, your weld will become dark and porosity issues will occur.
But, if your CTWD is too long, it would be very difficult to control the weld. You will experience ripples in the weld bead.
4. Current Polarity
When you do not run on DCEP for Flux Cored Welding Stainless Steel, you will have a ridiculously large amount of spatter.
Thus, make sure to use the correct polarity for this welding process.
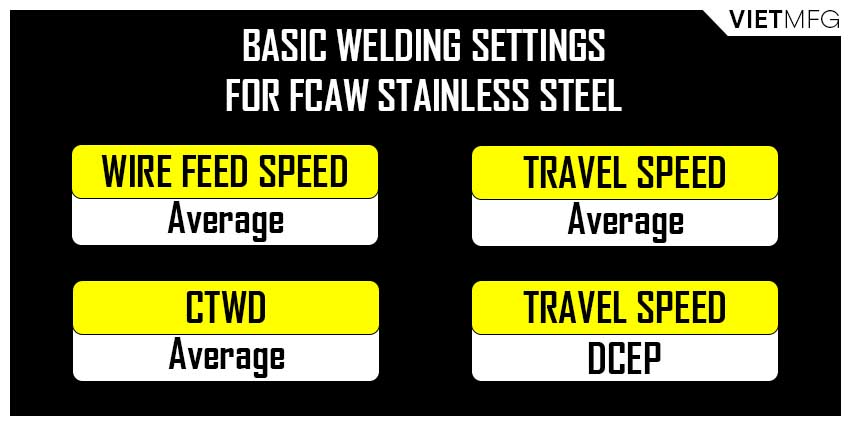
How Flux Cored Welding Stainless Steel Is Different From MIG Stainless Steel
The first difference lies in the arc produced by the two welding processes. With Flux Cored Welding Stainless Steel, the arc is not as smooth and steady as MIG Stainless Steel.
Another awkward thing about Flux Cored Welding Stainless Steel is that the more you pay attention to where the weld puddle is, the more distracted you become. Ultimately, you will not drag the flux cored wires fast enough.
This is quite different from MIG stainless steel. So, do not try to control the puddle. Keep practicing to build the feeling of how fast should you move the wires.
Tips And Tricks On Flux Cored Welding Stainless Steel
Here is what I think the most important tip to give for Flux Cored Welding Stainless Steel, that is “with slag, you drag”.
Through dragging motion, you allow the flux inside your hollowed wires to rise on top of the weld puddle for a proper coverage.
Maintain the drag angle of about 10 degrees.
And make sure to trim the flux cored stainless steel wires every time you lay down a bead. Otherwise, you will create a silicon blob at the tip of your wire, and that can totally mess up your welding.
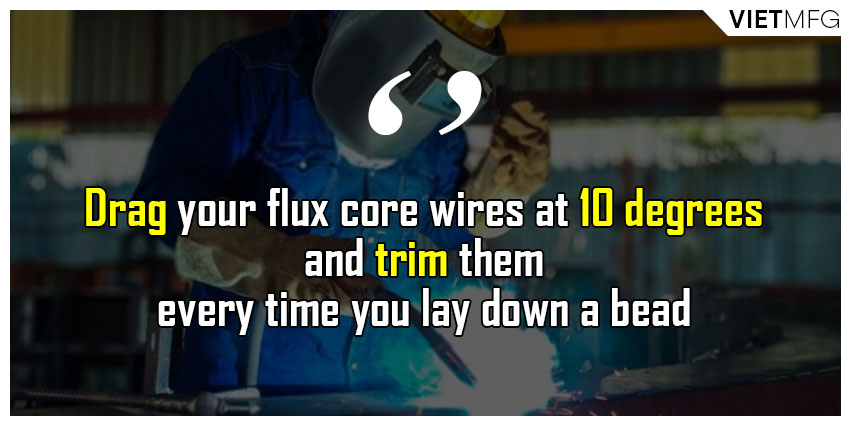
Conclusion
There you have it! A very simple guide on how to perform flux cored welding stainless steel.
I hope the article has saved yourself some time scratching around.
With a little bit of practice, you will surely be ready to take on that stainless steel repair.
Reference
- What? Stainless Steel Flux Core Welding Wire (Home Welder). Weld It Myself. Retrieved January 25th, 2021.
- Stainless FCAW: How-To and Tips. Make It From Metal. Retrieved January 25th, 2021.