If you are getting confused on how to select the most appropriate flux core wire for your welding projects, then congratulations, as you have come to the right place.
In this article, I will narrow things down and walk you through the journey of picking up the best flux core wire. After reading, you can:
- Grasp the basic ideas of what flux core wires are.
- Understand different types of flux core wires.
- Having a comprehensive guide on how to purchase flux core wires.
Let’s waste no more time and jump right in!

What Is Flux Core Wire?
Flux Core Wire is simply a welding wire used in the Flux Cored Arc Welding process, which contains flux inside its hollow core covered by the welding materials (usually mild steel) on the outside.
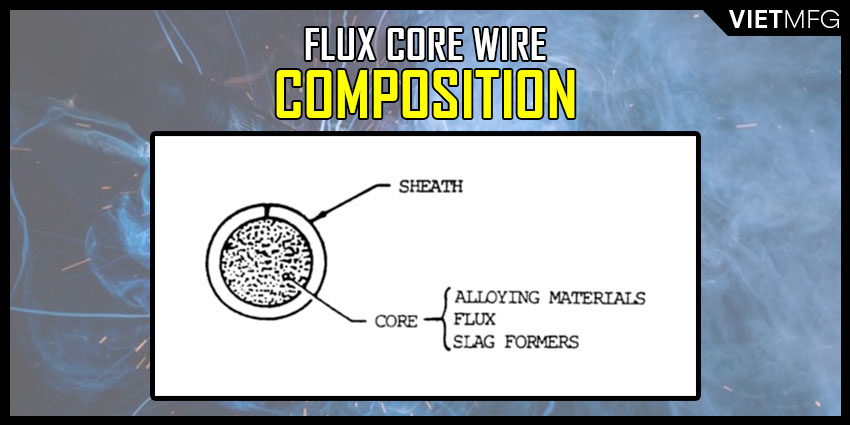
What makes flux core wire special is its flux, of course. The flux comprises many compounds that, when melted, generate a shielding gas to protect the weld from being contaminated. It also contains scavengers and deoxidizers to push impurities out of the weld and into the slag. The slag layer will be removed once the welding process is done.
There are various situations where you can make use of flux core welding wires. Some of them includes:
- You are a novice welder, or you plan to fix a broken metal.
- You do not have expensive welding guns.
- You need to get the welding application finished quickly.
- You are dealing with rusty or contaminated metals.
- You are performing the welding process outdoors or under windy conditions.
- You are forced to weld in awkward welding positions (vertical up, overhead).
Flux core wires function on constant-voltage (CV) DC power sources. It can work well on both DCEP and DCEN, depending on its composition. We will discuss this issue more detailedly in the later part of this article.
The concept of flux core wires has emerged around since the 1950s. There are basically two broad types of flux core wires: gas-shielded (FCAW-G); and self-shielded (FCAW-S).
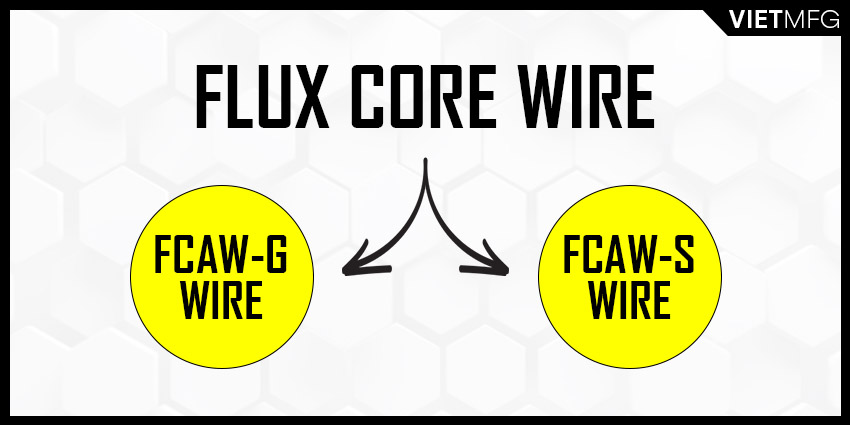
1. Gas-shielded Flux Core Wires (FCAW-G)
This first type refers to flux core wires that utilize an external shielding gas during the welding process. The slag formed from this type is easy to remove.
The flux of gas-shielded flux core wires solidifies faster than the molten weld metal. As a consequence, it can create a shelf to hold the molten pool more quickly. Hence, FCAW-G is very ideal for performing welding overhead or vertical up positions.
As the wires employ both the flux and the external shielding gas to protect the molten weld puddle, it is often regarded as the “double-shielded mechanism”.
When dealing with thick metals or difficult welding positions mentioned above, I highly recommend using gas-shielded flux core wires. This type of flux core wires is also applicable in some popular industries like pressure vessels building, petrochemical piping, and heavy equipment production.
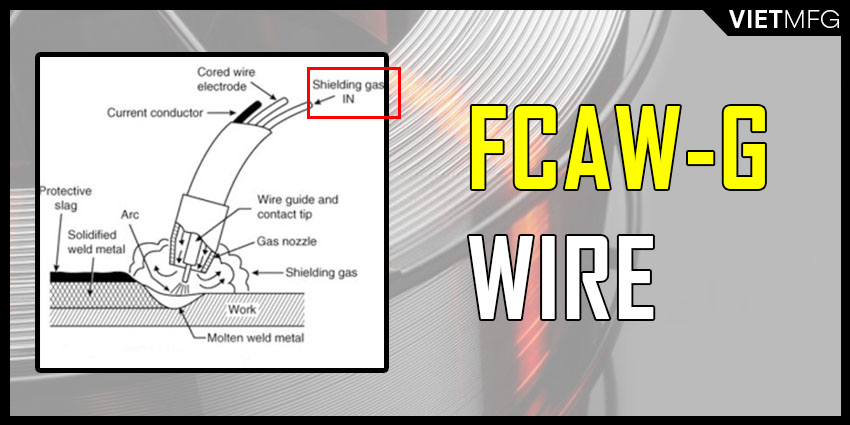
2. Self-shielded flux core wires (FCAW-S)
Contrary to gas-shielded flux core wires, self-shielded type does not require an external shielding gas and employs purely the flux for molten weld pool protection.
As the wire is burnt during the welding process, its flux will generate shielding gas to safeguard the molten weld puddle from contaminants.
With no external shielding gas utilized, FCAW-S provides more portability to the welding process. It can totally be used for outdoor processes.
You will often find self-shielded flux core wires being used in small-scale projects, like a DIY application or a small commercial environment, with a flux cored welder. However, it can also be utilized in some special industries, such as structural steel, and bridge construction.
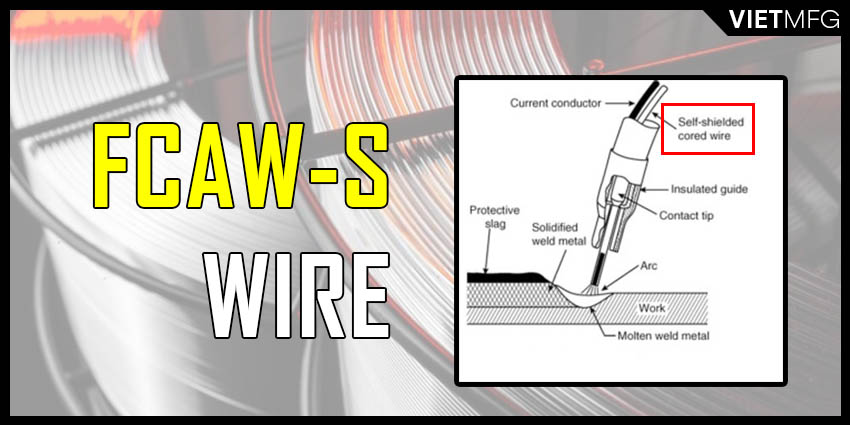
Advantages And Disadvantages Of Using Flux Core Wires
Like many other factors, the use of flux core wires also bear many pros and cons. Understanding them clearly will give you more confidence in when to use them. In this part, let’s talk about the advantages and disadvantages that flux core wires can bring about.
1. Advantages Of Flux Core Wires
In general, both types of flux core wires provides quick benefits of:
- Being efficient with welding dirty, cracked and rusted metal.
- Suitable for welding galvanized steel.
- Appropriate for novice welders to pick up and develop their welding skills.
- Allowing welders to duel with thick metals at low voltage quickly (thanks to their high deposition rates).
- Creating strong and clean welds.
With regard to gas-shielded flux core wires, they have many great advantages as follows:
- They deal better with thicker materials.
- They are perfect for awkward welding positions (overhead, vertical up), thanks to their flux coating getting solidified faster than other types.
Self-shielded flux core wires also possess various strengths:
- They do not rely on external shielding gas, so outdoor welding with them is possible (especially in windy conditions).
- Welding machines that run with self-shielded flux core wires are more compact and portable as they have no function for external gas shielding.
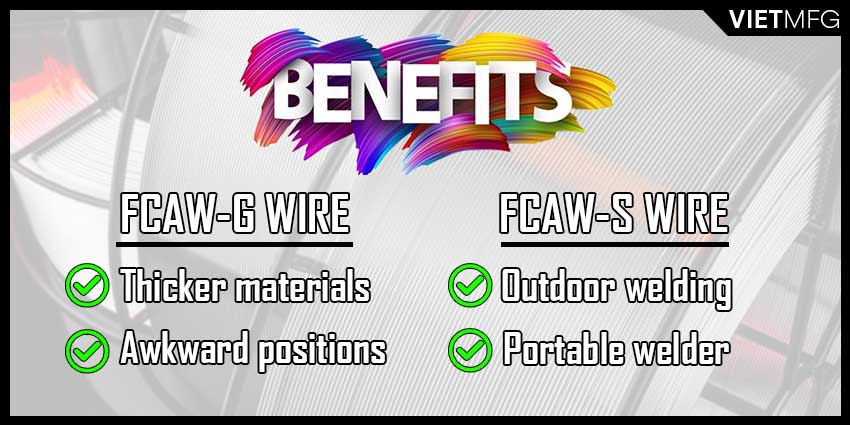
2. Disadvantages Of Flux Core Wires
Besides those great advantages, flux core wires aren’t that perfect. They still have their own problems in flux core arc welding. Some of their cons include:
- They are actually not good for indoor welding, as the flux compositions will not have enough natural air to react with during their melting. Eventually, you will have cracks, porosity and incomplete fusion, which all lead to an unsatisfactory welding job.
- Also, using gas-shielded flux core wires causes more trouble and complication than usual. This type of wires is designed specifically for heavy-duty tasks and expert welders. Beginners should not mess around with this thing.
Decoding The Meaning Of Flux Core Wires’ Names
As I mentioned above, there are two broad types of flux core wires, which are the gas-shielded and the self-shielded. However, flux core wires actually have many more categories to discover. Each comes with a different name. So, before jumping into all the details about those categories, let’s decode the meaning of these flux core wires’ names.
As most flux core wires are dedicated for mild steel, I will focus on them as well. Flux core wires for other metals will be discussed separately in other related articles.
1. Specification Codes Of Flux Core Wires For Mild Steel (AWS)
The specification codes of flux core wires for mild steel follow this format: EXXT-XX-JXHX.
Now, do not freak out! Let me slowly explain everything about the name for you.
Every name of flux core wires has two parts: Mandatory Designators (EXXT-XX) and Optional Supplemental Designators (JXHX).
Table 01: Discovering The Names Of Mild Steel Flux Core Wires.
Main part | Sub part | Meaning | |
Mandatory Designators | E | Current carrying electrode | |
X | Tensile Strength Designator | Minimum tensile strength: X*10 ksi, or X*10,000 psi | |
X | Position Designator | Welding position: “0” = Flat and Horizontal only“1” = All Position | |
T | Tubular electrode (Flux cored wire) | ||
X | Usability Designator | Usability (signals requirements for polarity and general operating characteristics) | |
X | Shielding Gas Designator | Shielding gas type: (Blank) = no shielding gas“M” = 75% – 80% Ar/ CO2 mixture“C” = 100% CO2 | |
Optional Supplemental Designators | J | Improved toughness “J” = Electrode will produce welds with CVN(*) values of at least 27 J at -40 celsius degrees. | |
X | Impact Designator | Supplemental mechanical property requirements “D”/ “Q” = will meet requirements when welded with high heat input and low heat input procedures. | |
HX | Diffusible Hydrogen Designator | Diffusible hydrogen levels “H4”/ “H8”/ “H16” = there will be a maximum of 4 ml (or 8 or 16) hydrogen per 100 grams of weld metal. |
(*) CVN stands for Charpy V Notch, which is a test to measure the energy amount absorbed by the material during fracture.
2. Meaning Of Usability Designator
In the table above, there is one designator called Usability that might be ambiguous to you at first sight. Don’t worry, as I will cover all its meaning in the following table:
Table 02: Understanding Usability Designator.
Usability Designator | Meaning | Flux Core Wire Type |
1 | DCEP polarity Rutile base slag Spray type transfer Low spatter loss Flat to slightly convex bead Moderate slag level Single or multiple pass Down hand only (large diameter) 5/64 inches or largerHigh deposition rate All position (small diameter) 1/16 inches or smaller Used with both CO2 and Argon-CO2 mix shielding gas Good impact properties (minimum CVN = 27 J at -18 celsius degrees) Good mechanical properties (70 – 95 ksi tensile strength) | FCAW-G |
2 | Same characteristics as T-1, but with higher levels of silicon and/or manganese Higher level of deoxidizersFor scaled or rimmed steels Single pass only Down hand only (generally) | FCAW-G |
3 | DCEP polarity Spray type transfer High welding speeds Single pass only Low penetration Sheet metal applications | FCAW-S |
4 | DCEP polarity Globular type transfer High deposition Low penetration Down hand only | FCAW-S |
5 | DCEP polarity Lime-fluoride basic slag Globular type transfer More spatter loss Slightly convex bead Thin slag level Down hand only (large diameter) All position (small diameter) Single or multiple pass Improved impacts and crack resistance against rutile types. | FCAW-G |
6 | DCEP polarity Spray type transfer Deep penetration Good low temperature impacts Multiple pass Down hand only | FCAW-S |
7 | DCEN polarity High deposition Down hand only (large diameter) All position (small diameter) Multiple pass | FCAW-S |
8 | DCEN polarity All position Multiple pass Good low temperature impacts | FCAW-S |
9 | Exact same characteristics as T-1 electrodes, but with better impact properties (minimum CVN = 27 J at -29 celsius degrees) | FCAW-G |
10 | DCEN polarity High travel speeds Single pass only Down hand only Unlimited material thickness | FCAW-S |
11 | DCEN polarity Spray type transfer General purpose All position High speed Multiple pass | FCAW-S |
12 | Exact same characteristics as T-1 electrodes, but with: Better impact properties (minimum CVN = 27 J at -29 celsius degrees)Lower manganese level (maximum level of 1.6%, tensile strength ranges from 70 – 90 ksi) | FCAW-G |
13 | DCEN polarity All position (except vertical up) Single pass only For root pass on pipe | FCAW-S |
14 | DCEN polarity All position (except vertical up) Single pass only Applicable for galvanized, aluminized and other coated steels | FCAW-S |
Apart from the fourteen values above, Usability Designator also includes “G” and “GS”, which stands for “General” and “General, Single pass” respectively. In both situations, they are general as not all specific requirements of other designation classifications are dedicated to this classification.
The purpose of these two Usability values is to allow newly developed flux core welding wires that might be different in one way or another to all other counterparts a way to still be categorized according to the filler metal specification.
In other words, “G” and “GS” allows a flux core wire to be used right away, without having to wait a long time for the filler metal specification to be revised to create a new usability designation.
Moreover, we can totally recognize the flux core wire to be FCAW-S or FCAW-G from the Usability Designator only:
- FCAW-S: T-3, -4, -6, -7, -8, -10, -11, -13, -14, -G, -GS
- FCAW-G: T-1, -2, -5, -9, -12, -G, -GS
3. What Are The Different Welding Effects Between Using Pure CO2 (C) and Argon-CO2 Gas Mixture (M) In The Case Of FCAW-G?
As we all know from the Shielding Gas Designator, there are two applicable shielding gases for FCAW-G. They are Pure CO2 (C) and Argon-CO2 gas mixture (M). Each shielding gas brings about different welding effects.
Employing Pure CO2 provides a better penetration profile. However, it also generates more spatter and creates a less stable arc.
On the other hand, the gas mixture of Argon-CO2 offers wonderful arc quality and creates less spatter. But, the gas mixture provides less penetration.
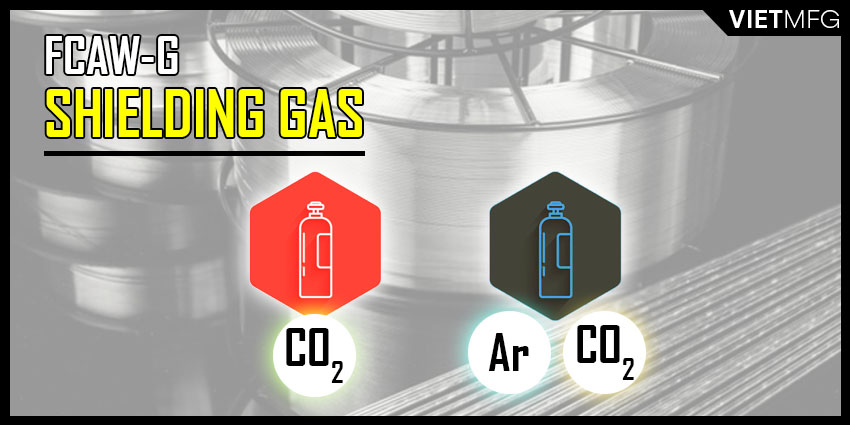
4. Official AWS Sources For Flux Core Wires’ Names
For flux core wires of mild steel, you can refer to A5.20/A5.20M:2005 “Specification for Carbon Steel Electrodes for Flux Cored Arc Welding”.
Besides mild steel, there are also flux core wires of low alloy metals. These electrodes are categorized in A5:29:A5:29M:2010 “Specification for Low Alloy Electrodes for Flux Cored Arc Welding”. These electrodes create stronger welds than mild steel electrodes, and possess higher minimum tensile strength of 80 – 120 ksi.
One key difference in the name between mild steel flux core wires and their low alloy counterparts is the position of the little dash (“-”). With mild steel flux core wires, the dash comes right before the Usability designator. On the other hand, in the names of low alloy flux core wires, the dash comes after the Usability designator.
For example: E71T-1M-JH8 is a mild steel flux core wire, while E81T1-K2M-JH4 is a low alloy electrode.
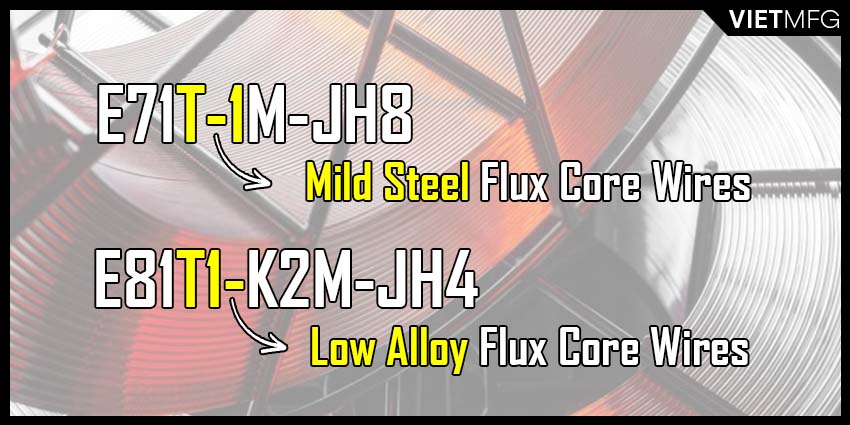
Besides the two above AWS documents, please note that in 2011, the official organization released another filler metal specification named A5.36/A5.36M:2012 “Specification for Carbon and Low-Alloy Steel Flux Cored Electrodes for Flux Cored Arc Welding and Metal Cored Electrodes for Gas Metal Arc Welding”.
The new document covers both mild steel and low alloy flux cored welding wires, as well as mild steel and low alloy metal cored electrodes. One notable thing is that the usability designators are similar to those in A5.29 and A5.20 published before.
If you notice, you will recognize that there is no official AWS document on flux cored welding aluminum . We will discuss this topic in a separate article.
Different Categories Of Flux Core Wires
If you understand how to retrieve information from the name of flux core wires, you would know by now there are 14 different types of wires. However, in this section, I will introduce the top 6 frequently used types.
1. E71T-1 Wire
Our first flux core wire, E71T-1, offers wonderful performance. As the name says, this is a gas-shielded flux core wire (T-1). The shielding gas can be either Pure CO2 or Argon-CO2 gas mixture.
This wire creates rapid freezing rutile slag, which is simple to remove after welding. E71T-1 also has the highest deposition rate, especially in the vertical-up position (up to 7 pounds per hour).
By using E71T-1, you can achieve an unsurpassed smooth welding arc with very little spatter, even with the employment of Pure CO2.
In the welding world, E71T-1 is regarded as the most popular flux core wire. It is ideal for shipbuilding, structural steel, as well as other general steel fabrications.
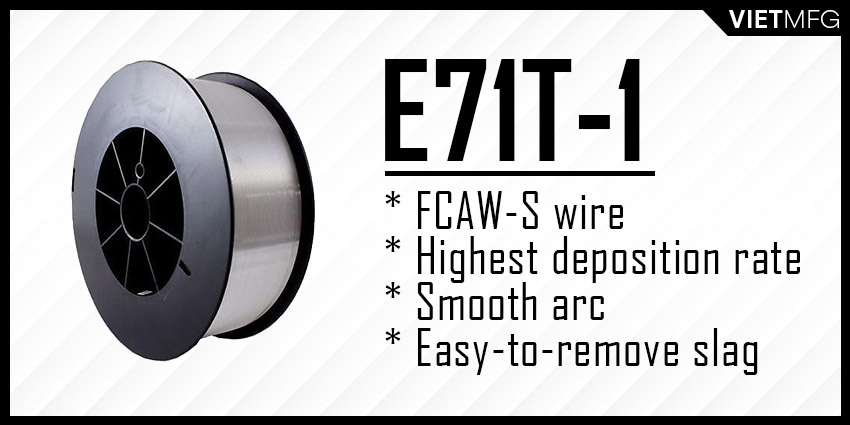
2. E71T-8 Wire
The next flux core wire, E71T-8, belongs to the self-shielded category.
It also provides very high deposition rates of up to 4.5 pounds per hour (in the vertical-up position).
This flux core wire is the perfect choice for welding outdoors and erection of structural steel projects.
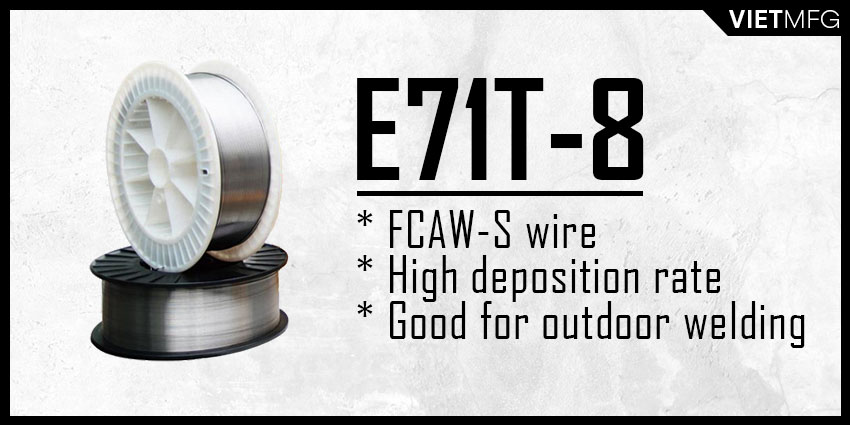
3. E70T-4 Wire
If you are having a tough time joining thick steel plates, then you should consider the gas-shielded wire E70T-4.
This flux core wire should be used in the flat position, as it can bring about very high deposition rates of up to 40 pounds per hour.
Once again, this self-shielded gas is mainly utilized for outdoor projects, thanks to its independence of external shielding gas. Projects involving joining thick steels with no CVN requirement are appropriate for the use of this flux core wire.
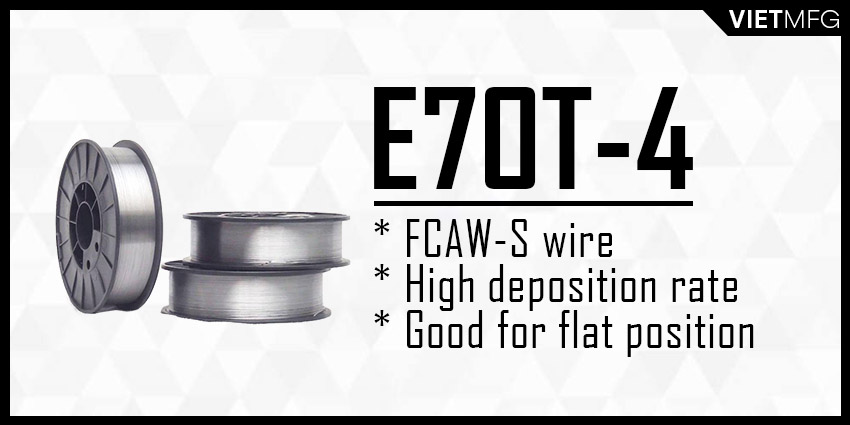
4. E70T-1 Wire
E70T-1 is considered an upgraded version of E70T-4, as it can be applied for projects with the CVN requirement.
It has a slightly lower deposition rate, around 30 pounds per hour. However, it offers a much smoother welding arc.
This flux core wire can deal effectively with rust and dirty plates. It is widely used in structural steel fabrication stores, with the use of Pure CO2 as the shielding gas.
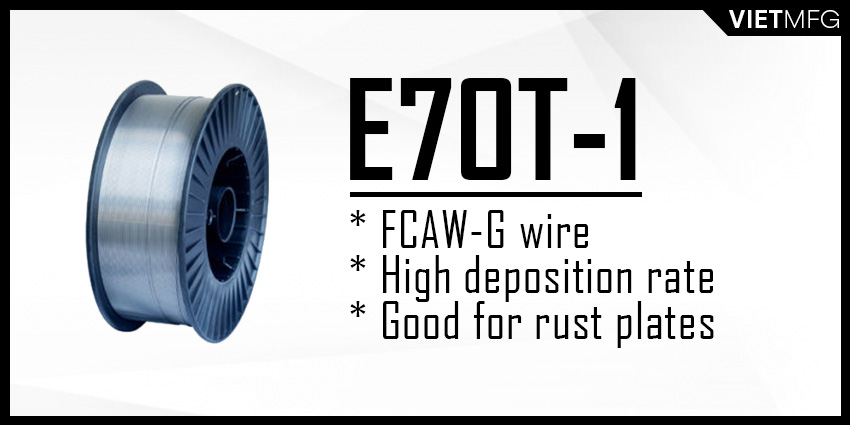
5. E71T-14 Wire
E71T-14 is the top choice for welding coated and galvanized sheet steels.
This self-shielded wire contains core flux that explodes in the arc to volatilize the steel coating and minimize porosity and cracking. The final result is a much stronger weld which is accomplished at faster welding speeds.
E71T-14 wires are utilized commonly in the automotive industry for welding galvanized steels.
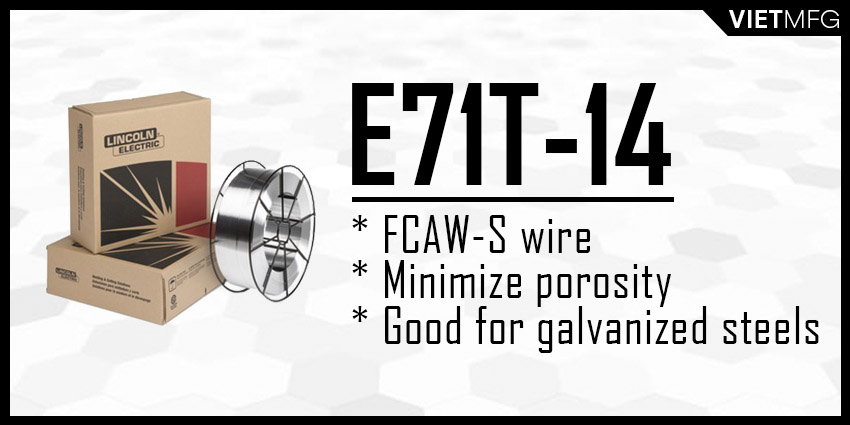
6. E70T-5 Wire
The gas-shielded E70T-5 wires offer the fastest solution for welding hard-to-weld steels, thanks to its superior crack resistance.
E70T-5 possesses the basic slag system that shares many similarities to the 7018 stick electrode. The flux core wires can remove sulfur and phosphorus from the weld metal. This property prevents poor toughness, cracking and porosity.
One notable thing about E70T-5 wires is that it has the lowest diffusible hydrogen levels among all flux core wires. This characteristic helps enhance resistance to delayed hydrogen cracking.
Moreover, E70T-5 produces exceptional CVN properties (Charpy impact toughness).
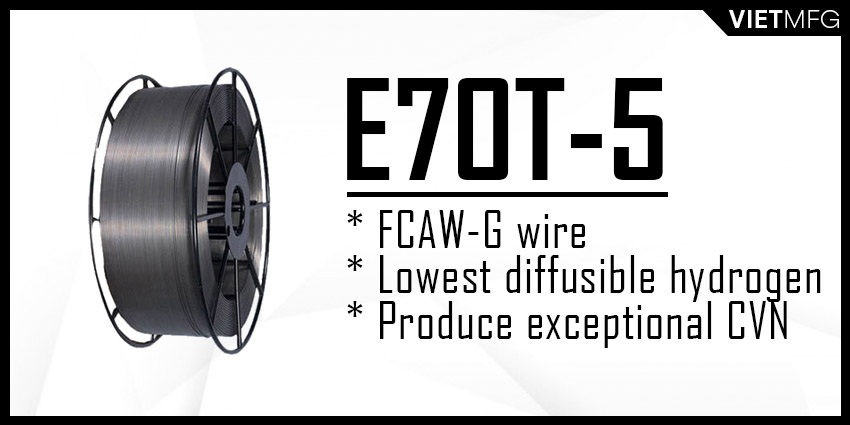
Table 04: Summary Information On Popular Types Of Flux Core Wires
Flux Core Wires | Category | Remarks |
E71T-1 | FCAW-G | Highest deposition rates for out-of-position welding |
E71T-8 | FCAW-S | Highest deposition rates for out-of-position welding without external shielding gas |
E70T-4 | FCAW-S | Highest deposition rates for flat welding position |
E70T-1 | FCAW-G | Highest deposition rates for flat welding position with Charpy properties |
E71T-14 | FCAW-S | Fastest travel speed on galvanized coated steels |
E70T-5 | FCAW-G | Fastest way to weld hard-to-weld steels |
Common Sizes Of Flux Core Wires
All two types of flux core wires are available in various standard sizes (or diameters), ranging from 0.03 inch all the way up to 3/32 inch.
In particular, there are seven different wire sizes that you can choose: 0.03 inch, 0.035 inch, 0.045 inch, 0.052 inch, 1/16 inch, 5/64 inch, and 3/32 inch.
To choose a proper size for your flux core wires, you must consider the following factors: material thickness, welding position, welding amperage, single or multipass weld joints.
Each size is dedicated to a specific application. For novice welders with general welding projects, a flux core wire with 0.03 inch or 0.035 inch in diameter is a good all-round choice for dealing with a wide range of metal thicknesses.
Regarding flux core wires with larger sizes (0.045 inch, 0.052 inch, 1/16 inch), you need to increase your amperage level. These three sizes are often classified as EX1T-X, which means they can be applied in all welding positions. You might also increase your travel speed as well, when you choose a larger size flux core wire.
Flux core wires with the size of 5/64 inch and 3/32 inch are considered as EX0T-X types, which are dedicated for flat and horizontal welding only. The amperage level required for these two sizes usually ranges from 400 to 450 amperes.
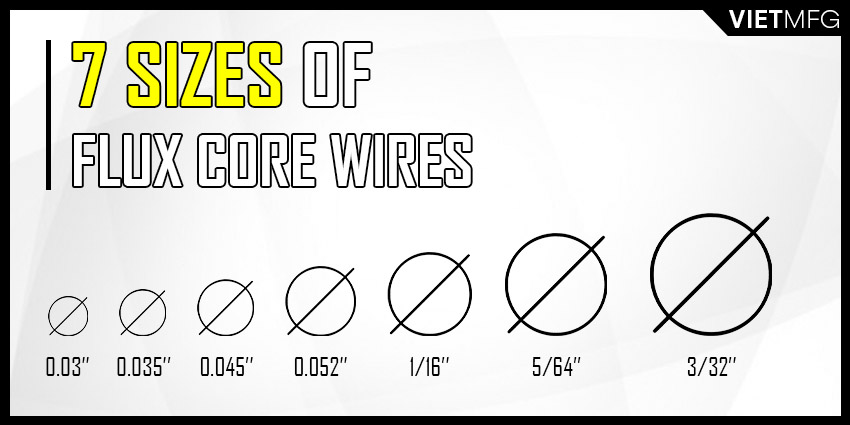
0.030 VS 0.035 Inch Flux Core Wires: Which Is The Better Option?
There is a heated debate among beginners and hobbyists regarding which is the better option between 0.030 and 0.035 inch flux core wires. I will try my best to give you a satisfactory answer on this debate.

Both 0.030 and 0.035 inch flux core wires are wonderful options. However, there are four aspects you should look at before deciding which size wire to use.
The first criteria is metal thicknesses. The thicker the wires, the more filler and flux they contain, and thus they serve better with thicker metals.
- 0.030 inch flux core wires: dedicated to metal thicknesses between 22 gauge to 1/8 inch.
- 0.035 inch flux core wires: are suitable for thicknesses ranging from 16 gauge to 1/2 inch.
Besides material thicknesses, the type of welding machines you are using also determines which size of flux core wires should be chosen.
- If you are using a 220 voltage machine to weld not too thin metal, you should go with 0.035 inch size wire.
- If you have a small welding machine designed specifically to flux core, then the 0.030 inch size wire is the better option.
The next aspect is the joint factor. Thicker size wires will create broader beads, which can weaken your joints in case they are tight. So, if you are dealing with tight joints with no caps, then stick with the 0.030 inch size wire.
Lastly, each size wire is compatible with a different amperage range.
- If you set your current level to around 125 amperes or less, then consider using the 0.030 inch wire.
- If your amperage setting is above 140 amperes, 0.035 inch wire is a great solution, unless you are dealing with very thin metals.
In short, I have compiled a small table that can quickly give you an overall look on the two popular options:
Table 03: Brief Comparison Between 0.030 And 0.035 Inch Flux Core Wires
Flux core wire size | 0.030 inch | 0.035 inch |
Metal thickness | From 22 gauge to 1/8 inch | From 16 gauge to 1/2 inch |
Welder type | 220 voltage welders | Small welders dedicated to flux core arc welding |
Joint factor | Tight joints with no caps | N/A |
Amperage level | Less than 125 amperes | Above 140 amperes |
All in all, there is no clear answer to the question: which is the better option? Both 0.030 and 0.035 inch flux core wires can give excellent performance under their preferable conditions.
Thus, instead of spending your time in the meaningless debate, let’s focus more on your metal workpiece as well as the welding conditions that can help you achieve the best results.
Flux Core Wires VS MIG Wires
In this part, I will discuss a little bit about flux core wires and MIG wires (or solid wires). These two wire types receive many attention from the welding community. Let’s learn more about them.
In terms of composition, flux core wires have a hollow core which is filled with flux chemicals. When being burnt, this flux will generate shielding gas and later, create a slag over the weld puddle to protect it from being contaminated. On the other hand, MIG wires have a solid core, which means it is filled with filler metal only.
Regarding the performance, both wires produce good bead appearances (under correct usage and within the suitable parameter settings). They both create deep penetration and little spatter. However, with flux core wires, they are better with sidewall fusion.
About the application, both MIG wires and flux core wires are easy to use and suitable for novice welders. But, MIG wires are preferable for thinner applications, as there is no need to chip off slag after welding. Thus, MIG wires can produce more aesthetic weld beads on thinner workpieces.
Comprehensive Buying Guide Of Flux Core Wires
In this section, I will outline several important aspects that you should consider before purchasing your desired flux core wires.
1. Reason For The Purchase
This should be your first question you ask yourself before the purchase.
You must understand your level of expertise, whether you are an advanced or a novice welder.
It will determine your ideal choice for flux core wires.
2. The Type Of Your Project
Understanding your project accurately will make it simpler for you to search for the appropriate flux core wires. Every welding project has unique demands that can only be fulfilled by specific wires.
If you are performing welding in large-scale projects (automobile workshop repairing, shipbuilding welds, etc.), you must look into higher quality materials. Cheap wires will only leave you with unsatisfactory beads.
Another noteworthy point is to match your flux core wire’s base material with your workpiece. For example, you will not stainless flux core wires for flux cored welding stainless steel .
3. Select Reliable Manufacturers
Reliable and trusted manufacturers will ensure offering you flux core wires with high quality, as well as good warranty policy and support.
Conclusion
That is everything I can share with you about flux core wires.
Remember, there is no one-size-fits-all wire that exists. Flux core wires, including both self-shielded and gas-shielded types, are only effective if applied correctly.
Therefore, knowing about flux core wires is good. But understanding your project is even more important. Only by that can you utilize the suitable flux core wires to make your welding better.
Reference
- Flux-Cored Wire Selection. Lincoln Electric. Retrieved January 4th, 2021.
2. Best Flux Core Wires – Top Picks and Reviews. Weld Guru. Retrieved January 4th, 2021.
3. Best Flux Core Wire On the Market Right Now Reviews and Comparison Table 2021. WeldingPros. Retrieved January 5th, 2021
4. Solid Wire Versus Flux-Cored Wire: When to Use Them and Why. Miller. Retrieved January 5th, 2021.
5. Flux-Cored Welding: The Basics for Mild Steel. Miller. Retrieved January 5th, 2021.
6. Selecting the Correct Diameter for Flux-Cored Wire. ESAB. Retrieved January 5th, 2021.