MIG Welding Nozzle is one of the most important MIG welding consumables throughout the whole process.
And trust me, the nozzle choice that you make has an enormous impact on your MIG gun performance, as well as the lifespan of that nozzle itself.
Thus, we have prepared a unique and overall selection guide for you right here in this article by covering:
- 2 Core Functions of MIG Welding Nozzles.
- Overall guide for selecting an appropriate MIG Welding Nozzles for your projects.
- Proper ways to handle, store and maintain MIG Welding Nozzles.
So with that said, let’s dive right in and explain.
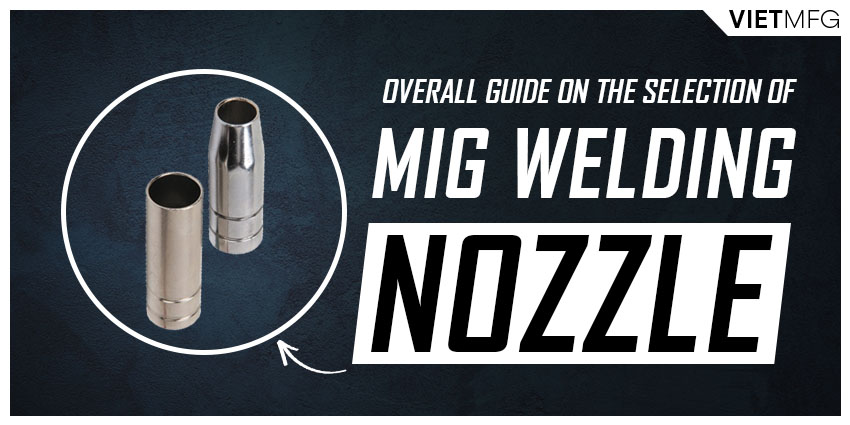
TWO Core Functions of MIG Welding Nozzle
MIG Welding Nozzle has 2 main missions:
- To protect the Contact Tip from meeting the molten metal.
- To direct the flow of shielding gas into the weld puddle.
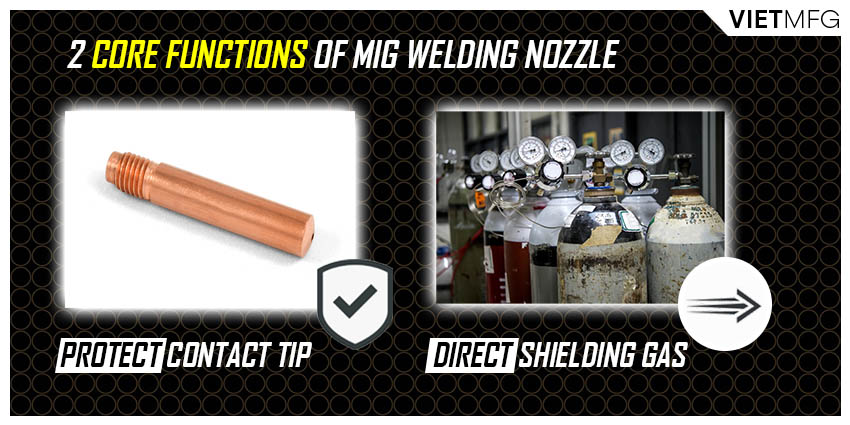
The effectiveness of MIG Welding Nozzles depends on the actual type of nozzle you employ.
Nowadays, the market offers a wide range of nozzle types.
Some types can provide better protection for the Contact Tip, while other types enhance shielding gas coverage.
Overall Selection Guide for MIG Welding Nozzles
Selecting the appropriate gun nozzles for your MIG Welding process depends on many factors, including:
- Joint type: a Tee joint and a Butt joint may require different gun nozzles.
- MIG Modes of Metal Transfer: certain nozzle types only work well with short-circuit transfer, while other types are suitable for axial spray, or pulsed spray, etc.
- Lifespan of the nozzle: choosing a long-lasting welding nozzle is more cost-effective.
Normally, the #1 consideration is to select the largest possible MIG Welding Nozzle, while maintaining the best joint access.
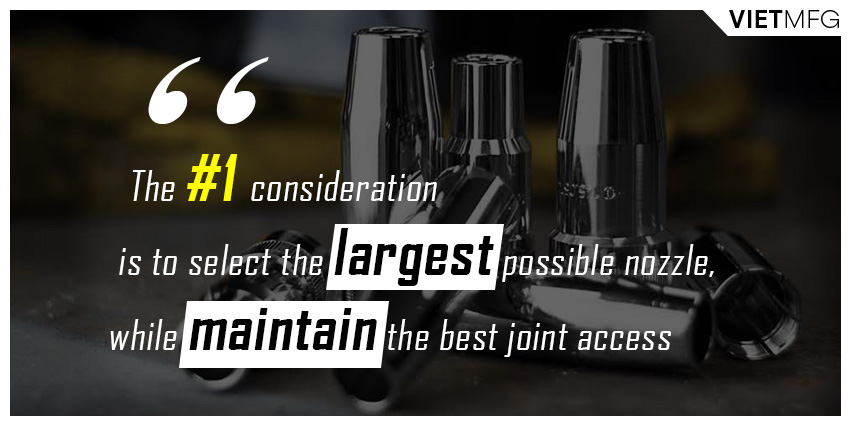
The reason is that larger nozzles (or larger inside diameters) are less likely to pick up and store spatter compared to smaller options.
Thus, choosing such a MIG Welding Nozzle can be confusing.
However, with enough understanding about each nozzle type and your welding requirement, we can gradually narrow down the list of potential options.
Let’s go over some common types of MIG Welding Nozzles!
1. Shape of MIG Welding Nozzles
Based on shapes, you can find (or hear about) 4 typical MIG welding nozzles, which are:
- Straight (cylindrical) nozzles.
- Bottleneck (bottleform) nozzles.
- Taper nozzles.
- Conical nozzles.
- Cylindrical nozzles.
Straight (Cylindrical) MIG Welding Nozzles
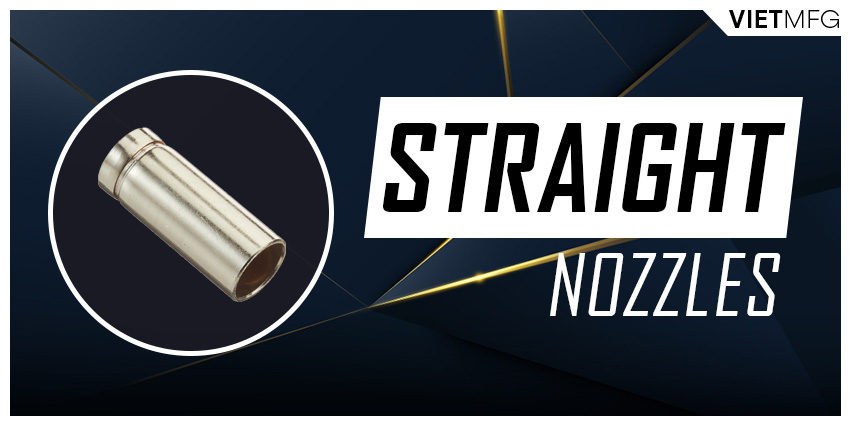
Straight nozzle, or cylindrical nozzle, is a very common option for MIG welding at high amperage.
It has large inside diameters (up to 3/4 inch), and is very suitable to go with larger contact tips (such as the heavy duty M10 or M12 size).
It is recommended to allow as much distance as possible between the straight nozzle and the contact tip (the clearance) to make room for MIG shielding gas.
Due to its large size, this nozzle type is the easiest type to perform cleanup actions, out of all welding nozzle types.
However, the use of straight nozzles has 2 main limitations:
- It provides LESS access to the weld joint (due to its large size).
- It does not work well with small contact tips like M6 or M8 style. Using such small contact tips means the clearance is too large and too much shielding gas is applied to the weld puddle, which can lead to porosity.
Bottleneck (Bottleform) MIG Welding Nozzles
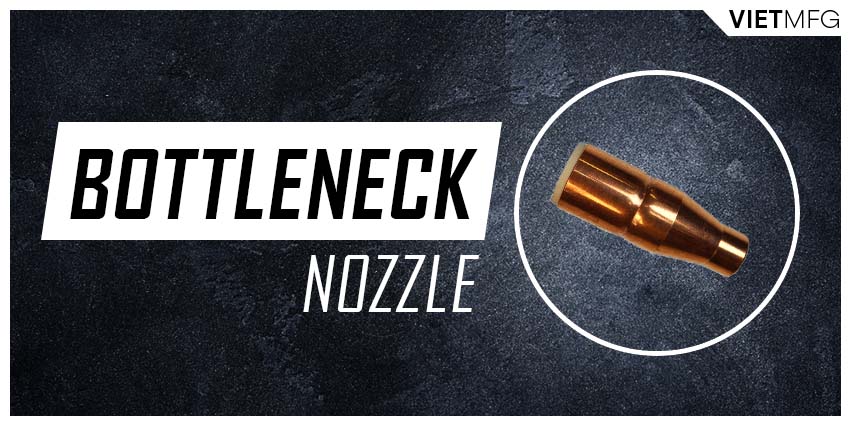
Bottleneck nozzle comes with a smaller inside diameter in comparison with straight option (about 1/2 inch).
Thus, it helps MIG operators with good access to the weld joint.
The front end (bottle neck area) of this nozzle type is usually a straight bore which allows for easy cleanup in robotic applications.
Thus, it is a good choice for automated MIG welding applications, and provides greater joint access.
However, because of the smaller and more constricted bottle neck area, bottleform nozzles have a high risk of spatter buildup.
Taper MIG Welding Nozzles
Taper nozzle has 2 versions: a long taper design, and a short taper design.
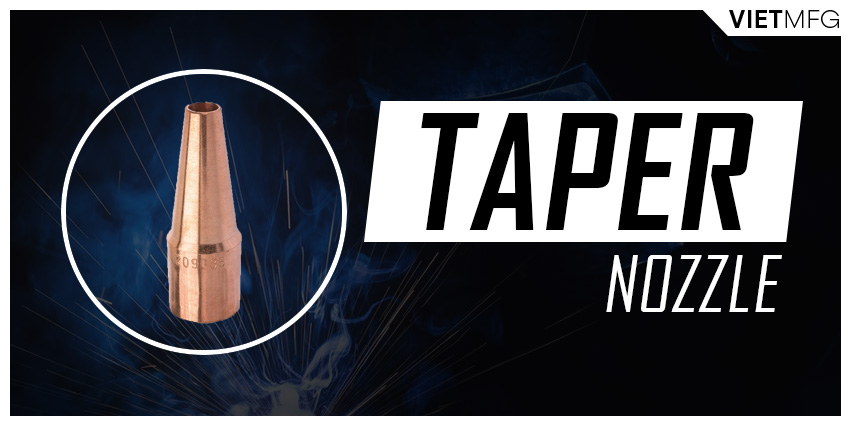
Both versions are preferred choices for high joint access demands from the MIG welding operation.
However, the long taper nozzle usually has a smaller inside diameter than that of the short design.
Thus, it is easier for the long taper version to collect and store spatter internally, which reduces the final weld quality of the MIG welding process.
With that being said, using a short taper nozzle can solve such a problem.
Taper nozzles are designed for applications with tight access like pipe welding or welding of very tight corners.
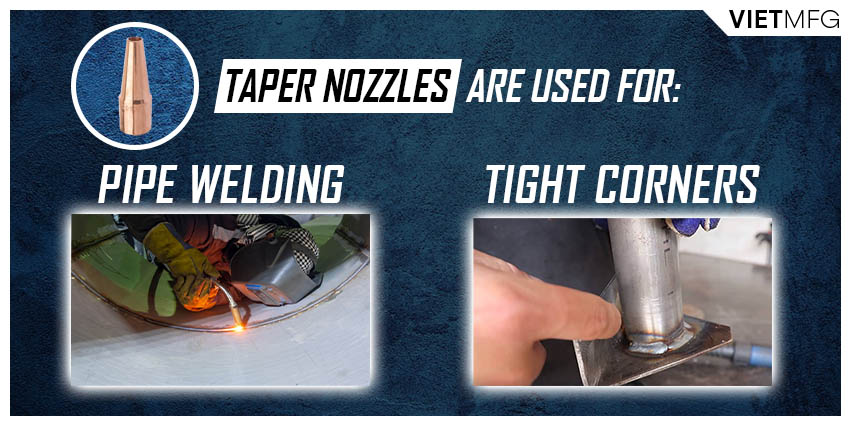
Conical MIG Welding Nozzles
Among all options, a conical-shaped welding nozzle provides you the best level of gas coverage, while still allows for sufficient access to the weld joint.
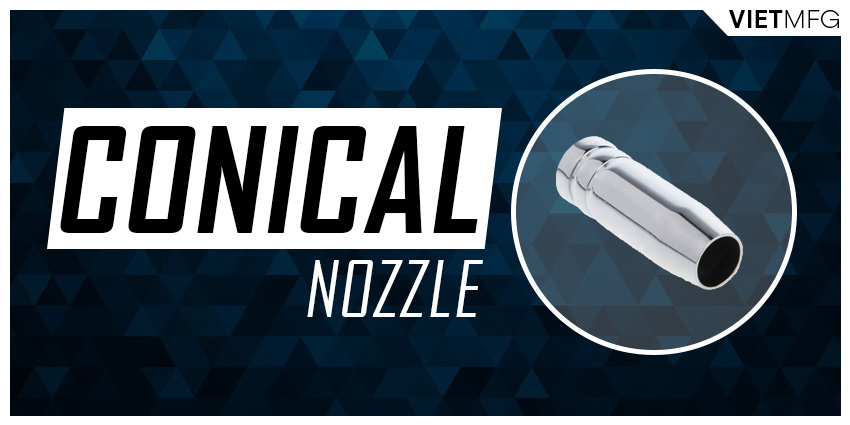
Thanks to the inner conical shape, shielding gas covers a larger area surrounding your weld puddle.
The conical shape also helps increase the speed of shielding gas into the weld puddle, which pushes atmospheric contaminants away from the puddle.
Conical nozzles are excellent choices for MIG welding zinc-coated metals, as they allow for an easier and more effective spatter cleanup.
This really helps as MIG welding of such material will create excessive spatter.
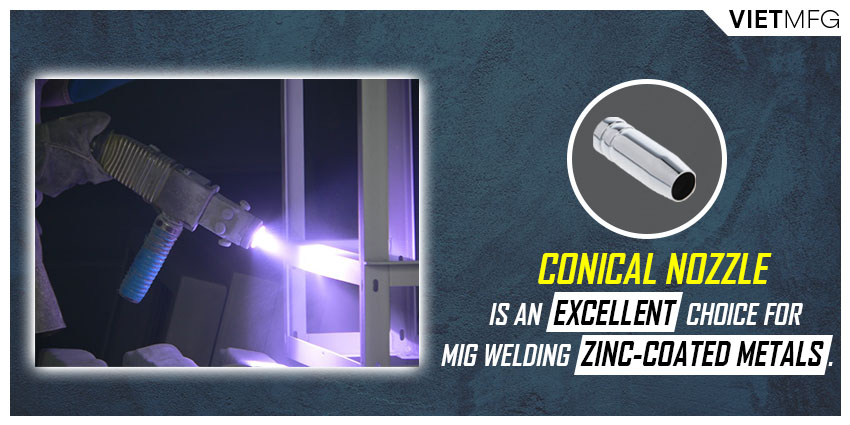
2. Size of MIG Welding Nozzles
The size of your MIG welding nozzles depends largely on their shape.
Typical nozzle size ranges include:
- Straight (cylindrical) nozzles are only available in big sizes, as they come with large bores.
- Bottleform nozzles have sizes ranging from 3/8 inch to 7/8 inch (9.5 – 21.5 mm).
- Conical nozzles have various bore sizes, commonly from 1/2 inch to 5/8 inch (13 – 15.5 mm).
3. Material of MIG Welding Nozzles
MIG Welding Nozzles are commonly made of copper, brass and even chrome or nickel-plated.
Copper Welding Nozzles
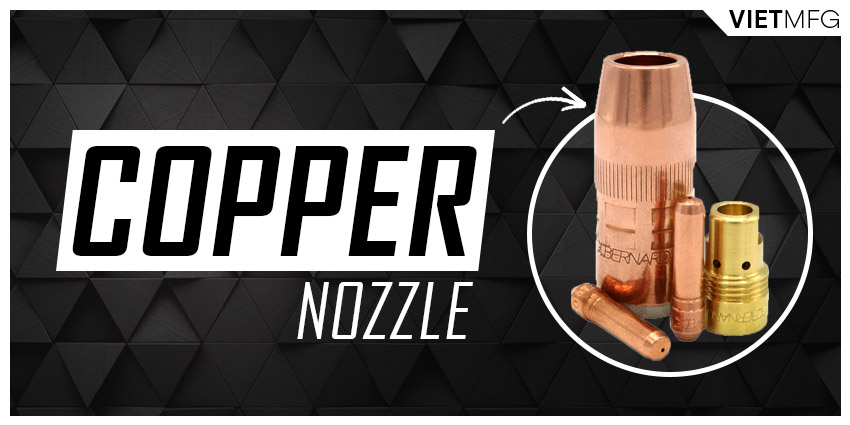
Copper nozzles are good at preventing spatter.
Unlike brass type, copper nozzles work fine on welding projects that require high amperage settings (over 300 amps) or long arc-on time.
For heavy duty projects with even higher amperage settings (400 – 600 amps), copper nozzles are built with thicker walls to provide sufficient protection against the heat.
Brass Welding Nozzles
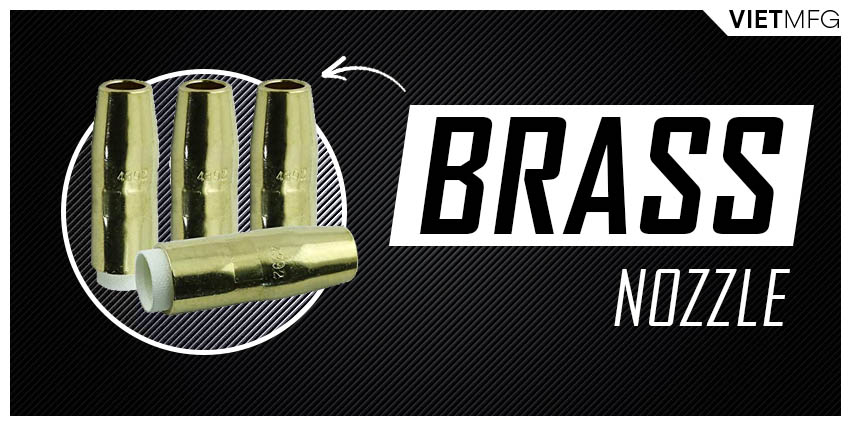
Brass nozzles have better spatter resistance, in comparison with copper type.
Brass nozzles are excellent options if you are working on low amperage projects (100 – 300 amps).
They also have lower price than their copper partners.
However, be aware that in a high heat environment, brass welding nozzles can fail, or even shatter into pieces.
Chrome or Nickel-plated Welding Nozzles
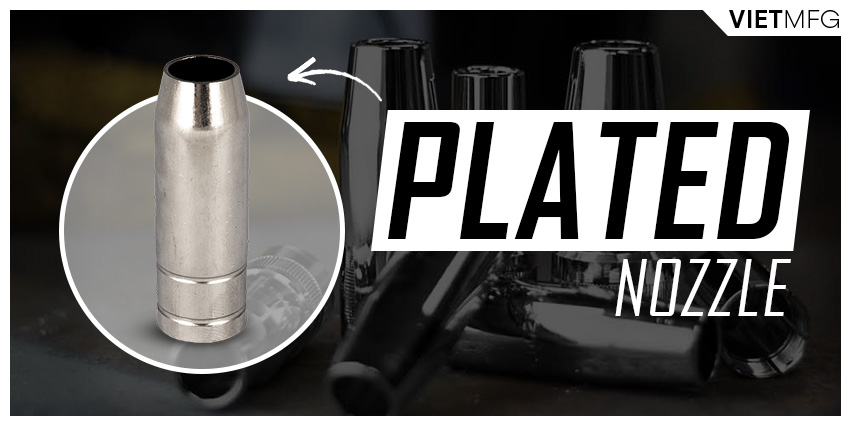
Usually, copper nozzles are equipped with chrome or nickel plates.
The plate helps the nozzles become more durable, even in high heat environments, as it deflects heat (instead of absorbing heat).
This means that during the MIG welding session, both the inside and outside part of your nozzle stays cooler, which increases its lifespan.
And copper nozzles, on its own, are already good at spatter resistance.
So, with this type, you are kind of getting “the best of both worlds” (the benefits of both metals combined).
This type of nozzle is often applied in robotics welding projects.
4. Thread-on vs Slip-on MIG Welding Nozzles
Thread-on and Slip-on nozzles are 2 separate types due to their difference in installing onto the front end of the MIG gun.
- Slip-on, as the name says, means that you just need to slip the nozzle onto the front end (no need to twist or snug down or anything like that).
- On the other hand, thread-on nozzles require twisting in order to install the nozzle properly. Thus, this type offers a more secure connection to prevent gas leak.
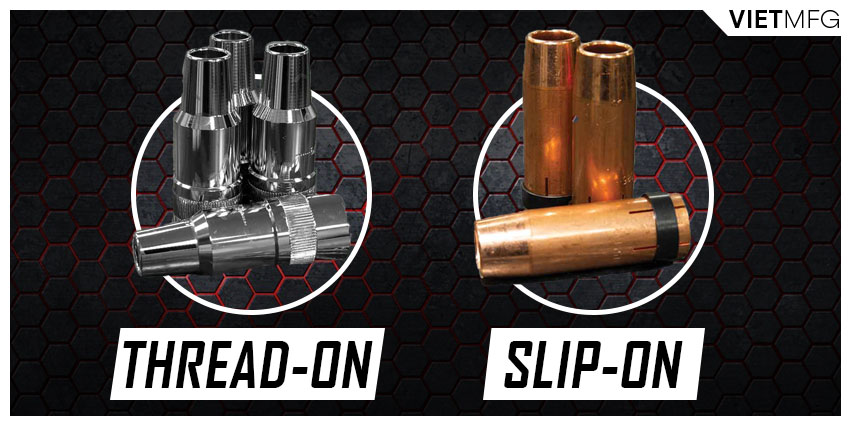
Among the two, slip-on nozzle is more popular, because of 3 reasons:
- Firstly, more MIG guns are designed to go with this type.
- Secondly, slip-on nozzles can be installed faster and easier than thread-on types.
- Lastly, slip-on nozzles are way more affordable than thread-on types.
However, when it comes to robotic applications, the slip-on type is not preferred because it is not very reamer-friendly and can be displaced during the cleanup process.
5. MIG Welding Nozzles in relation with Contact Tip Placement
For most cases, the use of MIG welding nozzles also decides the placement of your contact tip.
If we look at the contact tip placement, we will have another 3 types of welding nozzles:
- Flush nozzles.
- Stick-out (protruding) nozzles.
- Recessed nozzles.
Flush MIG Welding Nozzles
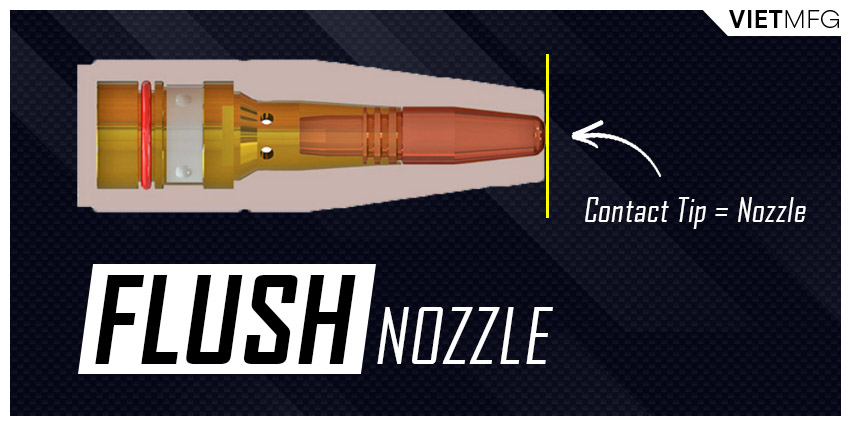
Flush nozzles are typically applied in short-circuit MIG welding.
This nozzle option does not have too much wire stick-out, which offers you a better view of where the MIG wire is running.
In other words, flush welding nozzles give you better visibility and this is very good for manual MIG welding.
However, the use of flush nozzles also has one limitation, which is the requirement for regular cleanup.
Otherwise, the contact tip located inside the nozzle can build up spatter.
Stick-out MIG Welding Nozzles
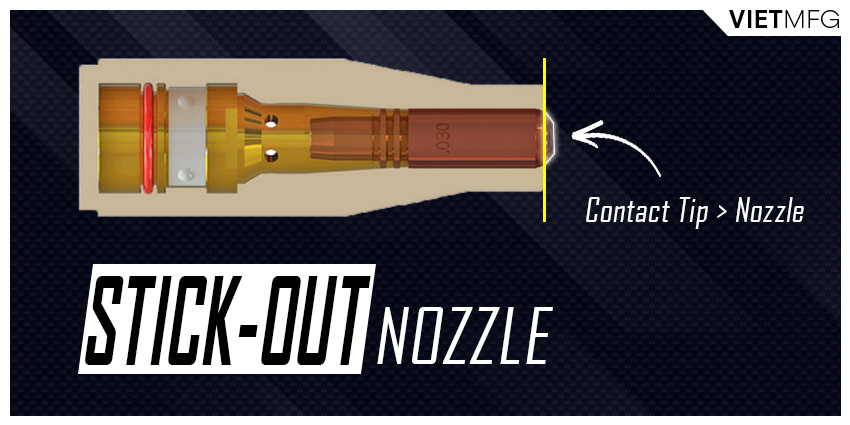
Stick-out nozzles are welding nozzles that feature the electrode wire to reach outside of the nozzle exit point and even touch the workpiece before the nozzles.
It provides poor shielding gas coverage due to the large clearance of contact tip.
Thus, stick-out type is restricted for use in MIG welding projects of very tight corners or at a spot that is too difficult to access.
Recessed MIG Welding Nozzles
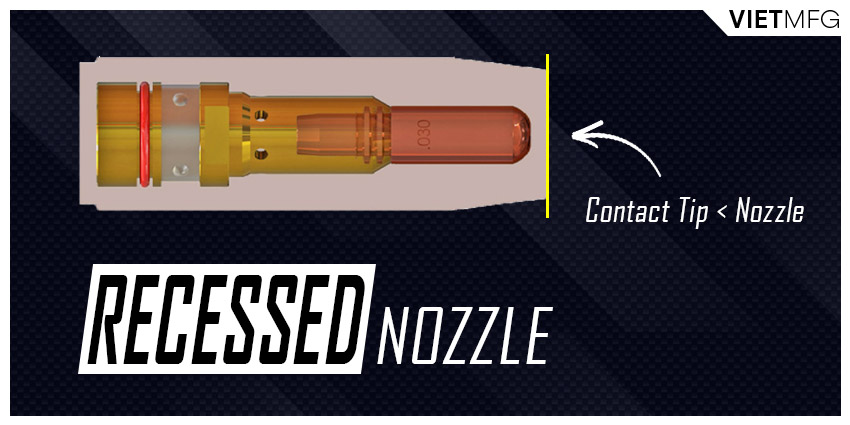
Recessed nozzles are welding nozzles with their contact tips located way inside.
This recessed position allows this nozzle type to have better gas coverage.
Thus, it can greatly prevent porosity.
Normally, this type of nozzle is applied for spray and pulse modes of metal transfer, with high amperage levels.
Maintenance of MIG Welding Nozzles
Choosing a high quality welding nozzle will surely enhance its lifespan.
However, with budget constraints, this is not always a preferred option.
Thus, knowing how to handle, store and maintain nozzles correctly will be more beneficial.
Below are some of the tips to handle the welding nozzles properly:
- Select the nozzles with smooth surface and smooth edges, as they prevent spatter more efficiently than nozzles with uneven surface.
- Heavy nozzle is a greater option than light nozzle, as it often comes with a thicker wall for better heat resistance.
- Look for nozzles with heavy-duty crimpings on them. These crimpings are signs for the longevity and durability of the nozzles.
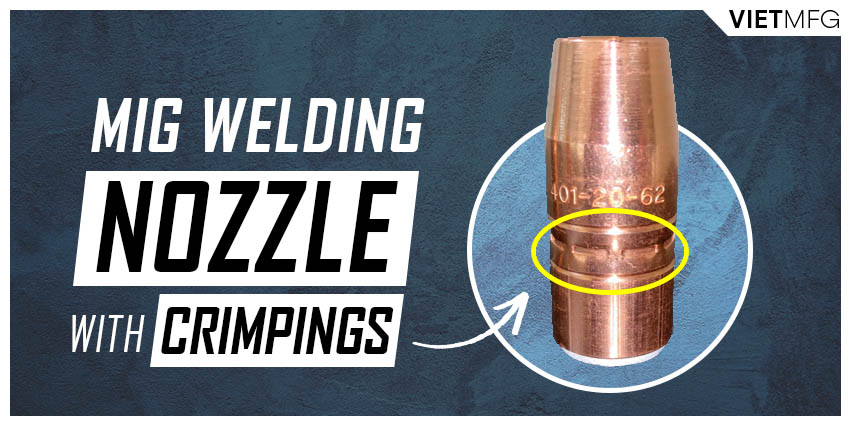
- Check and clean the nozzle regularly with anti-spatter products. Cantesco is a good spray to use.
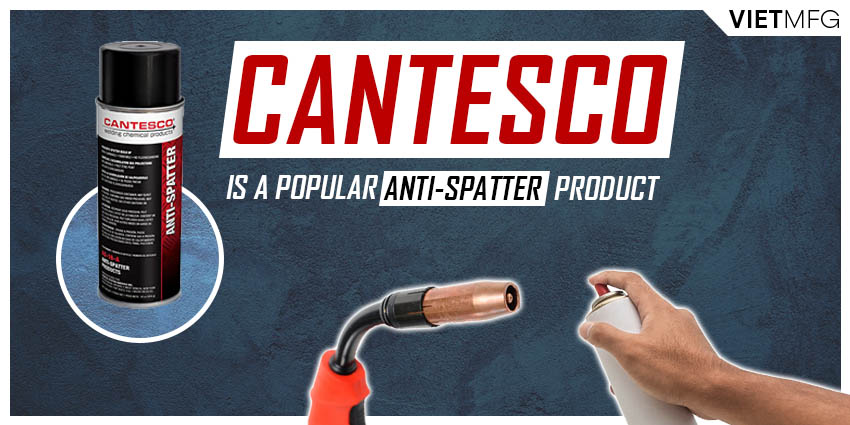
- Use gloves when replacing or touching the nozzles to prevent oil or other contaminants caught up to them.
- Store nozzles in their original packaging (normally a small plastic bag). If you store them in other places (like in a bin), it could lead to dents and scratches, which are wonderful places for spatter to stick to. That will shorten the nozzle’s lifespan.
Conclusion
That is every basics about MIG welding nozzles and how to treat them.
Remember that no matter what size, shape or material your welding nozzles are, always handle it well with anti-spatter sprays to prolong its lifespan.
Reference
- Welding Principles and Practices (5th Edition) – McGraw Hill Education. Edward R.Bohnart. [2017]
- Gas Metal Arc Welding: Product and Procedure Selection – Lincoln Electric. [2014]
- Understanding MIG Welding Nozzles. Tregaskiss. Retrieved October 6th 2020.
- Everything You Need to Know about MIG Welding Nozzles. American Torch Tip (ATTC). Retrieved October 6th 2020.
- Understanding MIG Welding Nozzles. Abicor Binzel Blog. Retrieved October 7th 2020.
- Binzel Basics: MIG Welding Nozzles. Youtube (Abicor Binzel channel). Retrieved October 7th 2020.