MIG Shielding Gas Selection is tremendously critical to the quality of your completed weld.
Understanding this importance urges us to produce this UNIQUE guide on the selection of MIG Shielding Gas for your projects.
After reading this guide, you will understand:
- Why we need shielding gas for MIG Welding.
- A list of 10 factors that influences your choice on MIG Welding Gas.
- 03 fundamentals properties of MIG Welding Gas.
- 04 basic types of MIG Welding Gas
Ready for some new knowledge? Let’s go!
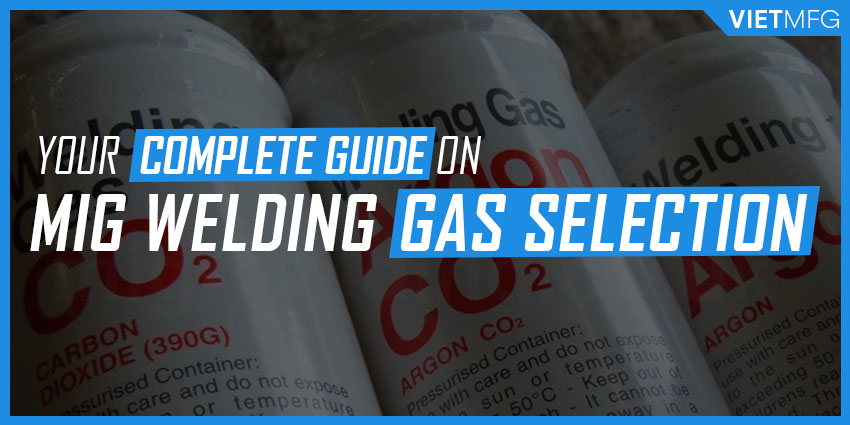
Why do we need shielding gas for MIG Welding?
The main purpose of using shielding gas for MIG welding is to protect the welding area from airborne gases like oxygen, nitrogen, hydrogen, propane, etc.
Without shielding gas application, your molten weld pool shall be exposed to gases and contaminants in the atmosphere.
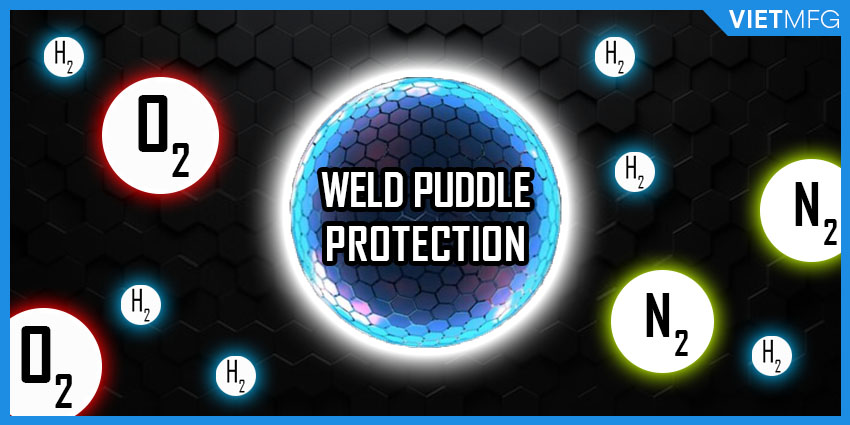
This exposure causes certain welding flaws, such as: fusion defects, porosity (holes within the weld bead), metal embrittlement, and excessive spatter.
On the contrary, the employment of proper shielding gas produces a cleaner and faster MIG welds:
- Cleaner welds are due to the protection from atmospheric contaminants, as mentioned above.
- Faster welds are possible, thanks to the zero interruption in between weld runs to replace contaminated electrodes (as in the case of stick welding).
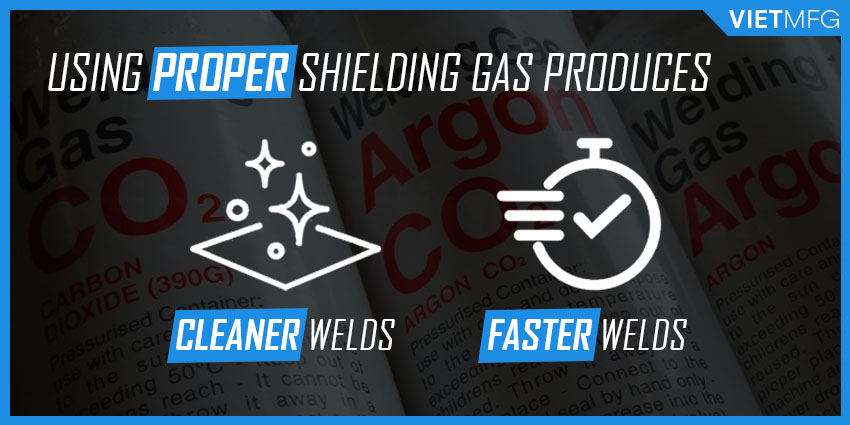
TEN factors influencing your MIG Welding Gas Selection
The use of shielding gas in MIG Welding is proven to be extremely effective.
However, a proper choice of MIG Welding Gas is influenced by many different factors.
We have researched and compiled the following list of 10 factors that all fabricators should consider carefully before selecting shielding gas for your MIG projects.
Here is the list:
- Factor 1: The MIG Welding Wire Selection.
- Factor 2: The mechanical features of the deposited weld metal.
- Factor 3: The thickness and joint type of your workpiece.
- Factor 4: The condition of your workpiece (if it has mill scale, oil or corrosion).
- Factor 5: The MIG modes of metal transfer.
- Factor 6: The welding position.
- Factor 7: The fit-up conditions.
- Factor 8: The desired penetration profile.
- Factor 9: The desired appearance of your weld bead.
- Factor 10: The overall cost (most important factor of all, maybe).
One shortcut for your optimal selection of shielding gas is to consult your supplier of MIG wires
Provide your supplier with a good idea of your MIG welding project details, so that they can offer you some suitable options with consideration of many above factors.
Besides, be sure to check your MIG welder recommendation guide which is located on the inside panel of the welder.
THREE fundamental properties of MIG Welding Gas
In this part, you will learn about 03 fundamental properties of MIG Welding Gas, which are:
- Ionization potential.
- Thermal conductivity.
- Chemical reactivity with the molten weld puddle.
1. Ionization Potential of Shielding Gas
Ionization Potential refers to the amount of energy required for ionizing the shielding gas.
The energy is measured in eV (electron volt).
You may ask, why do we need to ionize the gas?
Well, ionization helps the shielding gas become conductive (both heat and electricity conductive).
When the shielding gas is conductive (that is, a plasma), it can transfer both heat and electricity to your workpiece, and make your MIG welding project possible.
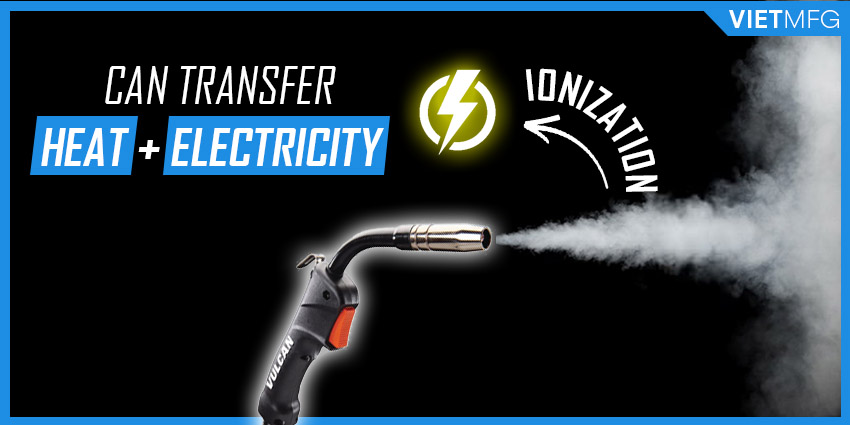
That’s it! So in short, in order to perform MIG welding, we need to ionize the shielding gas, by energy.
Each type of gas has different ionization potential.
- HIGH ionization potential means the gas requires MORE energy to be ionized.
- LOW ionization potential means the gas requires LESS energy to be ionized.
One example is about Argon and Helium – two most common shielding gases for MIG Welding.
If you notice, Argon can start the arc faster than Helium.
This is because it is easier to ionize Argon than Helium.
Argon has lower ionization potential (15.7 eV), while Helium has higher ionization potential (24.5 eV).
2. Thermal Conductivity of Shielding Gas
Thermal conductivity refers to the shielding gas’ ability to deliver thermal energy, or heat, to your workpiece.
It is regarded as the most important consideration when you go out and select a shielding gas for you welding projects.
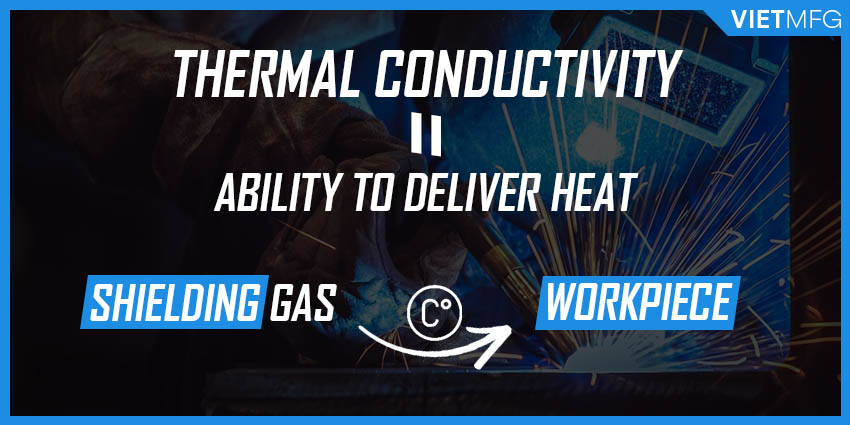
Similar to Ionization Potential, different shielding gases possess unique thermal conductivity levels.
This property affects your arc shape and penetration depth.
- HIGH thermal conductivity (of Helium, for example) creates a wider arc zone with more shallow penetration.
- LOW thermal conductivity (of Argon, for example) produces a smaller arc zone, but a deeper penetration pattern.
3. Chemical Reactivity between Shielding Gas and the Molten Weld Puddle
Well, the title almost says it all.
The chemical reactivity here refers to the most fundamental property of the shielding gas, whether it is inert or reactive with the weld puddle.
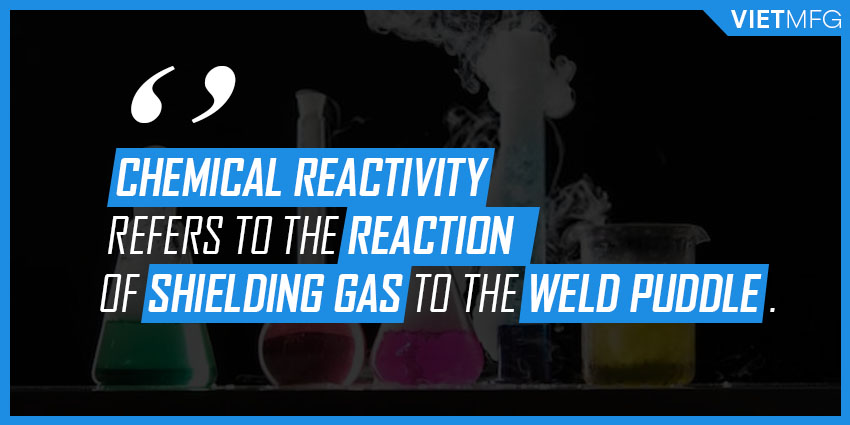
Unlike TIG Welding, in MIG operations, you have more usable options for shielding gas, including both inert gases (Argon, Helium) and reactive gases (Oxygen, CO2, etc.)
The main consideration here is that reactive gases are way more affordable (cheaper) than inert gases.
Therefore, if you have a budget constraint, you may want to lean yourself towards reactive gases.
FOUR basic types for your MIG Welding Gas Mixture
As mentioned earlier, there are two groups of MIG Welding Gas: Inert and Reactive.
The four most common types of shielding gas for MIG operations are: Carbon Dioxide (CO2), Argon, Helium and Oxygen.
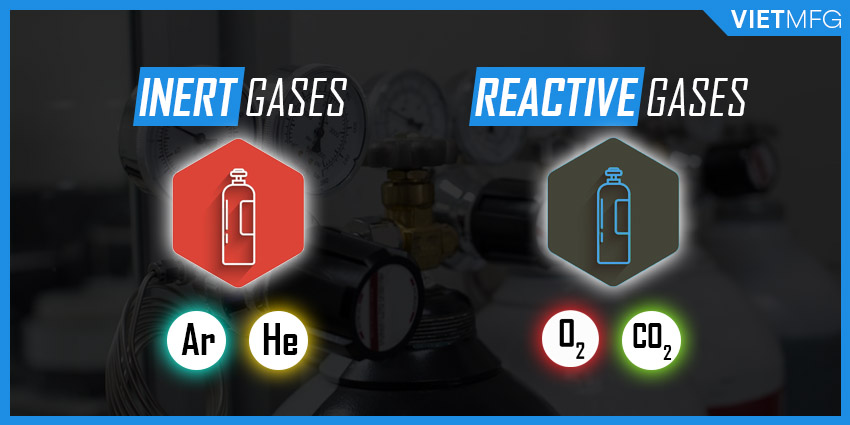
Each option provides unique enhancements, as well as drawbacks, to your MIG performance.
In this part, you will learn about each of them, together with how to mix them to produce the most effective shielding gas for your MIG projects.
So, don’t blink and make sure you follow it all the way to end.
1. Inert MIG Shielding Gas
There are many factors influencing your choice of a shielding gas, especially for MIG welding process since you have a wider range of choice.
One of the factors is the material type of your welded metal (remember Factor 2 mentioned above?)
If the metal being welded is non-ferrous (which means it contains no iron), then congratulate you, as pure inert shielding gas is your best option.
With inert shielding gas for MIG welding, you can choose either Argon or Helium.
(a) Argon
Argon is probably the most widely used inert shielding gas.
As we have discussed, Argon has LOW ionization potential, as well as LOW thermal conductivity.
Thus, it produces a deep and narrow penetration pattern that looks like a finger, which is great for butt and fillet joint types.
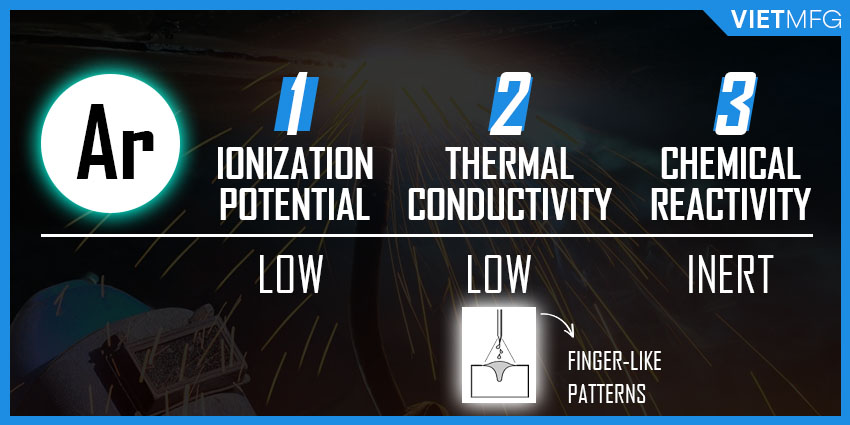
It is also easier to strike an arc using Argon as shielding gas.
Argon is employed widely in MIG welding of non-ferrous metals, such as titanium, copper, nickel, aluminum and magnesium.
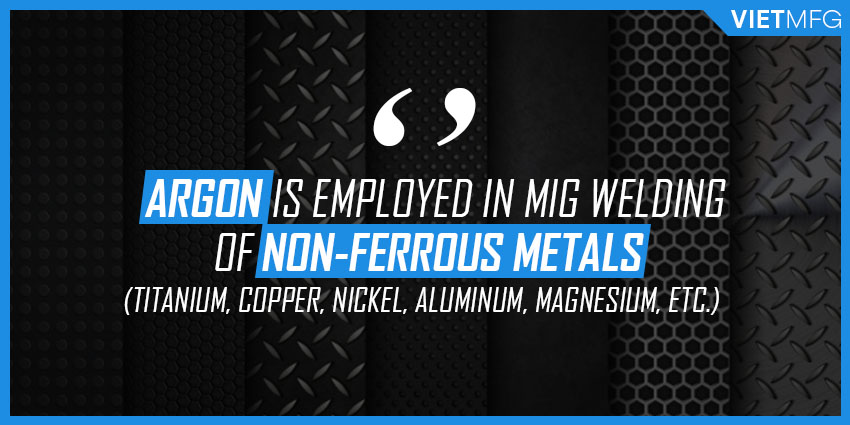
Argon is also a base component for mixing with other gases to create binary (two-gas mixture) or ternary (three-gas mixture) in MIG welding, which will be discussed later in this article.
(b) Helium
Everything about Helium is high: HIGH thermal conductivity, HIGH ionization potential, and HIGH price as well.
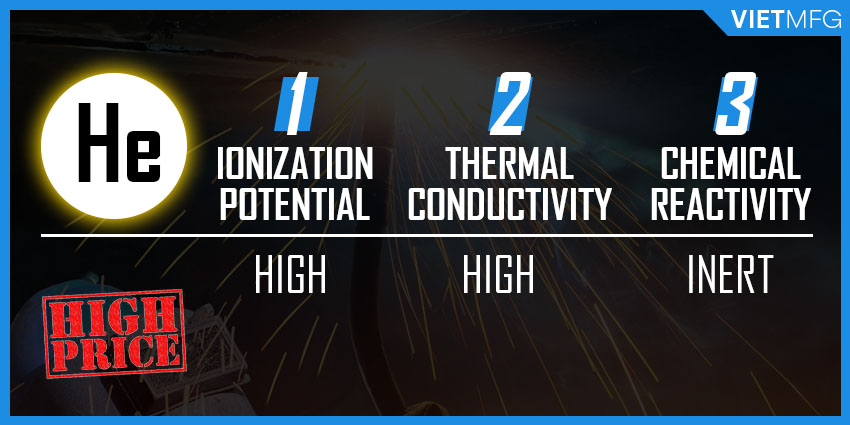
Because of its expensive price tag, helium is often added to a gas mixture, and not used in its pure form.
Besides non-ferrous metals, Helium is also applied for stainless and aluminum MIG welding, especially for pieces with thickness greater than 1 inch (25 mm).
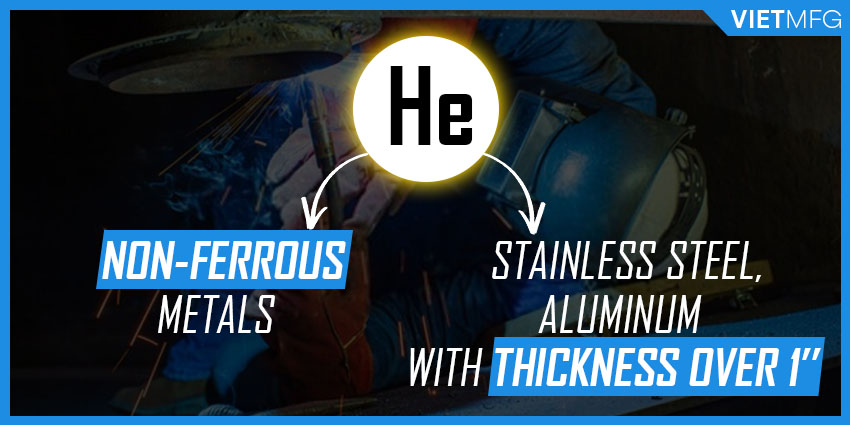
When you use helium, you can produce a broader penetration profile, but not as deep as that of Argon.
One special thing about Helium is that it can boost your productivity.
This is possible because Helium creates a hotter arc, which forces you to move your MIG gun faster (increased travel speed), and eventually, you finish your MIG welds faster.
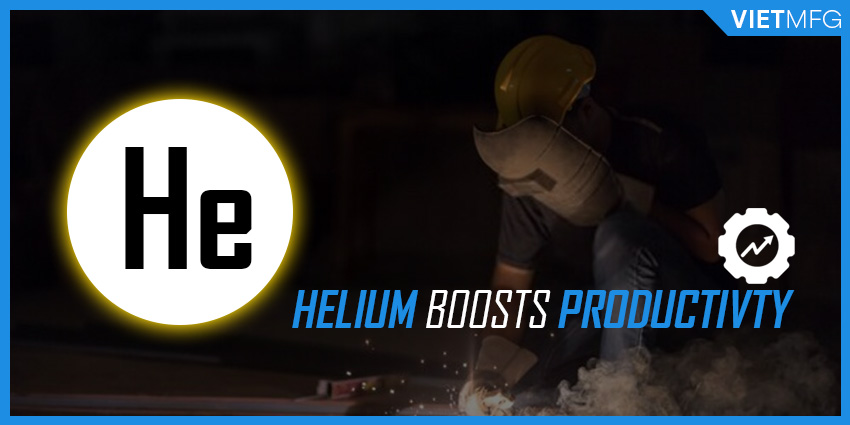
2. Reactive MIG Shielding Gas
Reactive shielding gases used for MIG operations include: Carbon dioxide (CO2), Oxygen, Nitrogen, Hydrogen, etc.
Reactive gases can chemically react with the molten weld pool to create a desirable feature.
(a) Carbon Dioxide (CO2)
CO2 is the only reactive gas that you can use in its pure form (without any mix of inert gases).
Thanks to this, CO2 is considered the most affordable option.
The use of CO2 as a MIG shielding gas provides a deep and broad penetration pattern (which is explained more detailedly later).
This feature makes CO2 the optimal choice for MIG welding thick materials.
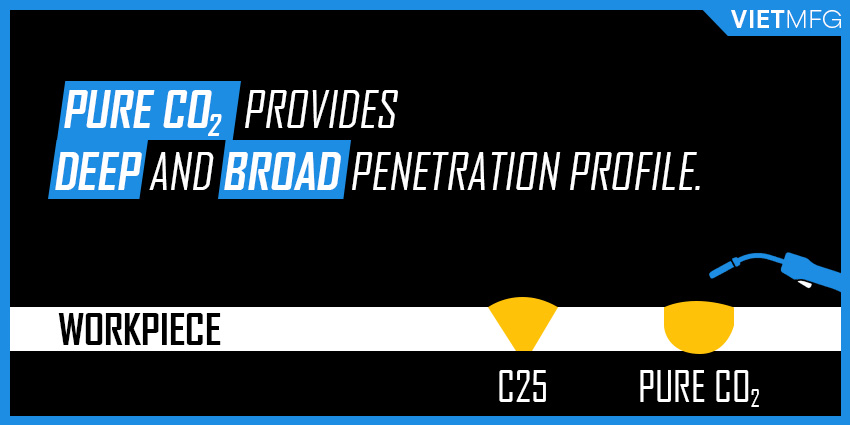
However, out of the 4 modes of metal transfer, pure CO2 is suitable only with short circuit mode.
Moreover, the use of pure CO2 creates more spatter than when it is mixed with other gases.
Thus, it is advised to use for projects with low aesthetic requirements, such as on the underside of a car.
That’s the basics for CO2!
The following content goes a little deeper into why CO2 provides a deep and broad penetration pattern.
CO2 only becomes reactive with the molten weld puddle after being ionized.
Such a penetration pattern is possible thanks to the two processes called “dissociation” and “recombination”.
- Dissociation: At the anode region (DC+), the CO2 molecule is broken into free carbon, oxygen, and carbon monoxide (CO).
- Recombination: At the cathode region (DC-), which is the workpiece itself, the released components of the CO2 molecule recombine together to form CO2. This creates a high energy level, which leads to a broad and deep penetration pattern.
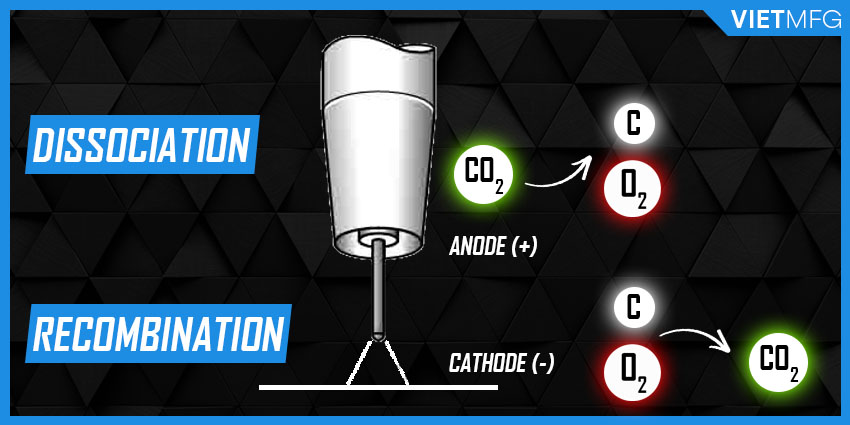
The amount of CO2 used as shielding gas can seriously affect the appearance of your finished weld.
*** HIGH level of CO2
A high level of CO2 will release more free oxygen after going through dissociation and recombination processes.
These free oxygen will react with your metal alloys (silicon, manganese, iron, etc.) to form a layer of oxide.
Then, the oxide layer floats to the weld pool surface and solidifies there, creating slag.
*** LOW level of CO2
On the contrary, a low level of CO2 will release less free oxygen, and thus create no oxide layer for slag forming in the end.
Thus, performing MIG with low level of CO2 can reserve all alloyed elements in your workpiece, and enhance ultimate tensile strength of your finished MIG welds.
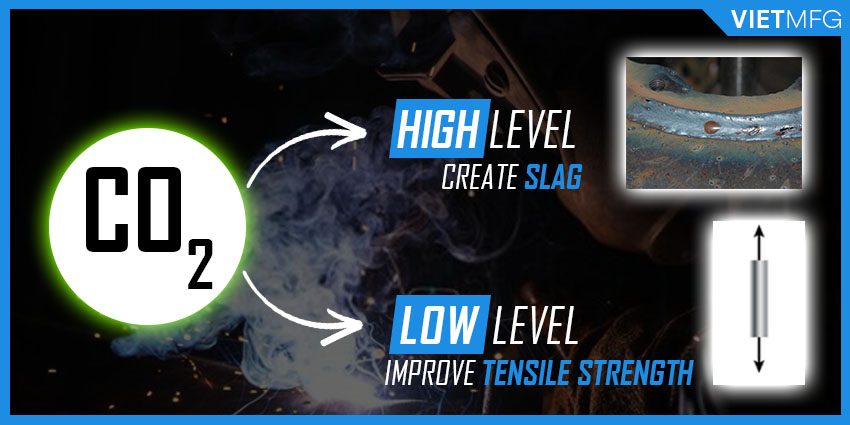
(b) Oxygen (O2)
Oxygen (O2) will surely react with your molten weld pool to form oxides.
Thus, it must be kept at low levels (1-9%), and must be mixed with an inert gas.
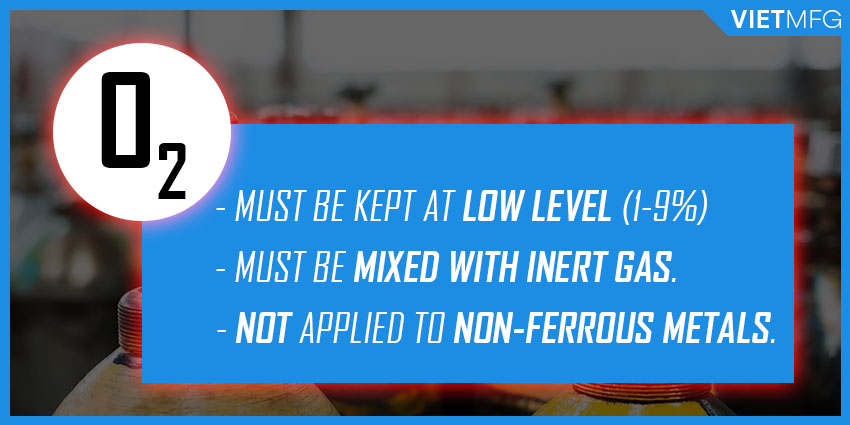
The application of O2 helps enhance weld pool fluidity, arc stability and weld appearance.
O2 is good for MIG Welding Stainless Steel and MIG Welding Mild Steel.
It is prohibited to use O2 with non-ferrous metals, such as copper, aluminum, magnesium, as it can cause oxidation.
(c) Hydrogen (H2)
Hydrogen (H2) is also used in small amounts (1-5%), and mixed with an inert gas (probably Argon).
It has HIGH thermal conductivity, which helps create a more fluid weld pool and allows for faster travel speeds.
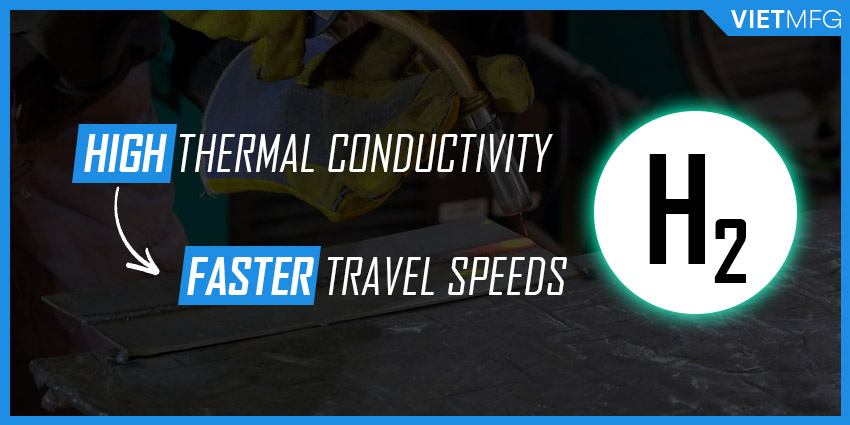
Hydrogen can be applied in high-temperature projects for austenitic stainless steels.
(d) Nitrogen (N2)
Nitrogen (N2) is often employed for MIG welding stainless steel tubes, mainly as a back-purging gas.
It can also be mixed with Argon and used as a shielding gas for MIG projects of stainless steels.
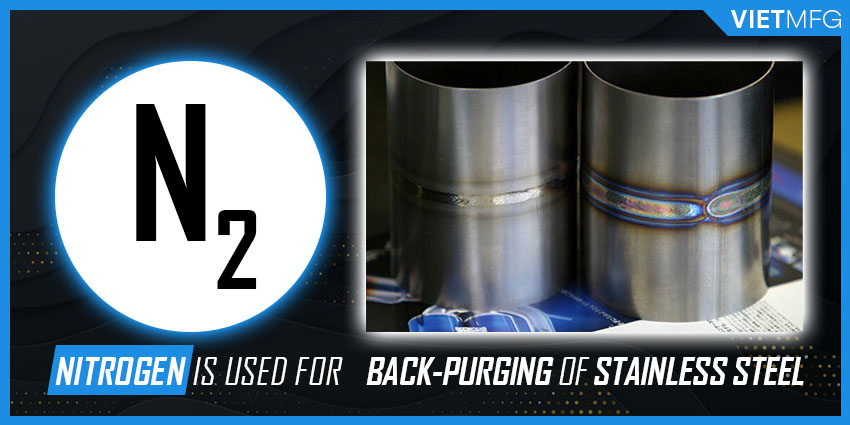
3. Two-part MIG Shielding Gas Mixtures (Binary Mixtures)
Two-part MIG Shielding Gas Mixtures, also known as Binary Mixtures, are often the combination of either: Argon + Helium; Argon + CO2; or Argon + O2.
(a) Argon + Helium
The mixture of Argon and Helium is normally applied for MIG Welding Aluminum, nickel and stainless steel.
Axial spray and pulsed spray transfer are this mixture’s favorite mode of metal transfer.
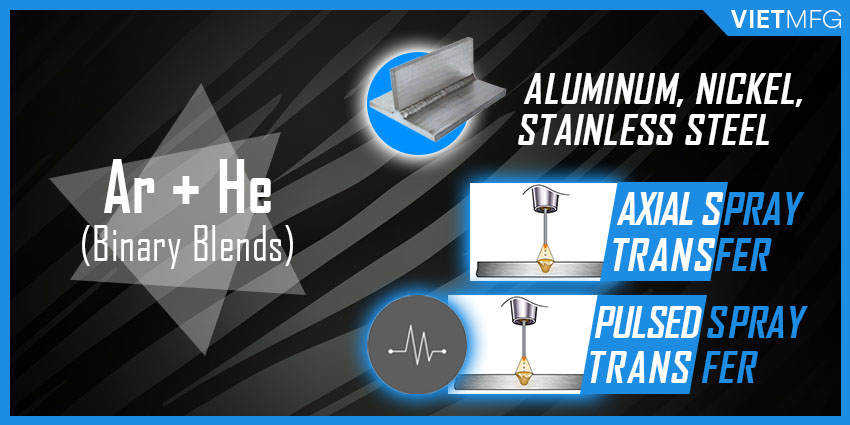
The addition of Helium to this binary gas blends enhances the weld pool’s fluidity and thus, increases travel speed.
Helium also reduces the finger-like pattern that is found in Pure Argon application, especially on aluminum.
So in short, while Argon makes it easy to strike an arc and helps with the cleaning action (on aluminum), Helium increases travel speed and reduces finger-like penetration pattern.
There are two common binary blends for Argon and Helium:
- Firstly, it is 75% Argon + 25% Helium. Compared to Pure Argon, this mixture enhances the puddle fluidity and penetration profile better for MIG welding of aluminum, nickel and copper.
- Secondly, it is 25% Argon + 75% Helium. Higher levels of Helium further increases thermal conductivity, puddle fluidity, and broadens the penetration profile. Ultimately, it provides a higher travel speed.
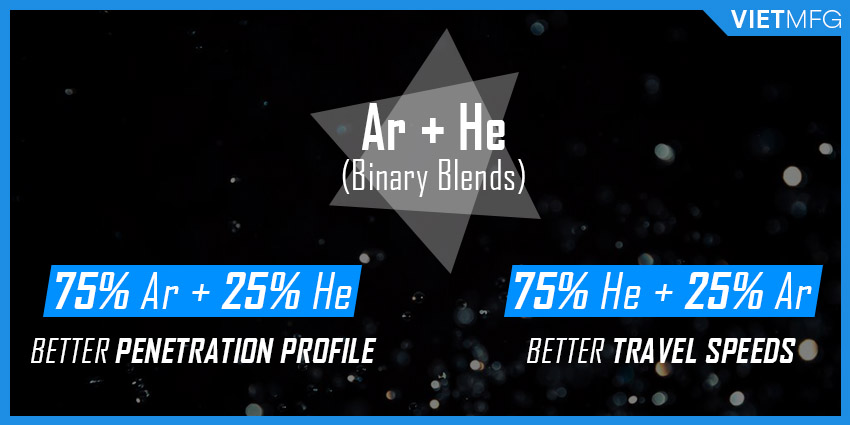
(b) Argon + CO2
The mixture of Argon and Carbon Dioxide (CO2) is good for MIG welding stainless steel and mild steel.
All modes of metal transfer can be used with this gas mixture.
However, depends on the level of CO2, the suitable mode of metal transfer is different
- If CO2 content is lower than 4%, pulsed spray mode should be used, especially for stainless steel.
- If CO2 content is less than 18%, axial spray mode is a good choice.
- If CO2 content reaches over 18%, short circuit mode is more effective.
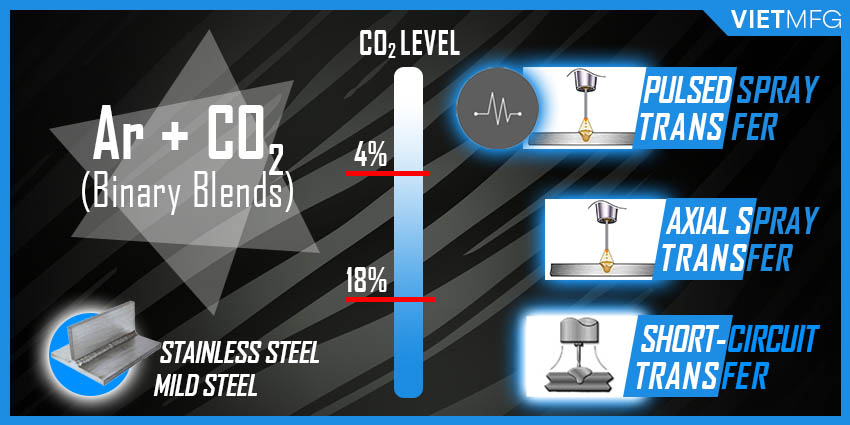
Normally, CO2 level varies from 5% to 25% in the mixture.
The addition of CO2 provides better arc stability and reduces spatter that Pure CO2 might cause.
But be careful, higher levels of CO2 increases the chance of spatter and burn-through.
Here are some common combinations for this gas mixture:
Binary Blends | Characteristic | Mode of Metal Transfer |
75% Argon + 25% CO2 (also known as C25) | Prevents spatter and enhances weld bead appearance on carbon steel applications. | Short Circuit |
80% Argon + 20% CO2 | ||
98% Argon + 2% CO2 | Provides great puddle fluidity and fast travel speeds with carbon steel or stainless steel electrodes. | Axial Spray/ Pulsed Spray |
95% Argon + 5% CO2 | Enhances puddle fluidity, with carbon steel electrodes. Suitable for thicker workpiece. | Pulsed Spray |
92% Argon + 8% CO2 | Suitable for carbon steel applications. | Axial Spray/ Pulsed Spray |
90% Argon + 10% CO2 | Suitable for carbon steel applications. Provides a broader arc and reduces the depth of finger-like penetration pattern. | Axial Spray/ Pulsed Spray |
85% Argon + 15% CO2 | Enhances sidewall fusion on sheet metal. Provides less heat and reduces burn-through risk. | Axial Spray/ Pulsed Spray/ Short circuit |
82% Argon + 18% CO2 | Can be used for various welding thicknesses. Produces a broad penetration pattern. | Axial Spray/ Short circuit |
(c) Argon + O2
The use of Argon and Oxygen mixture allows you to increase travel speed on thin materials.
This mixture is popular with MIG welding stainless steel and mild steel.
However, the level of O2 used should not exceed 5%.
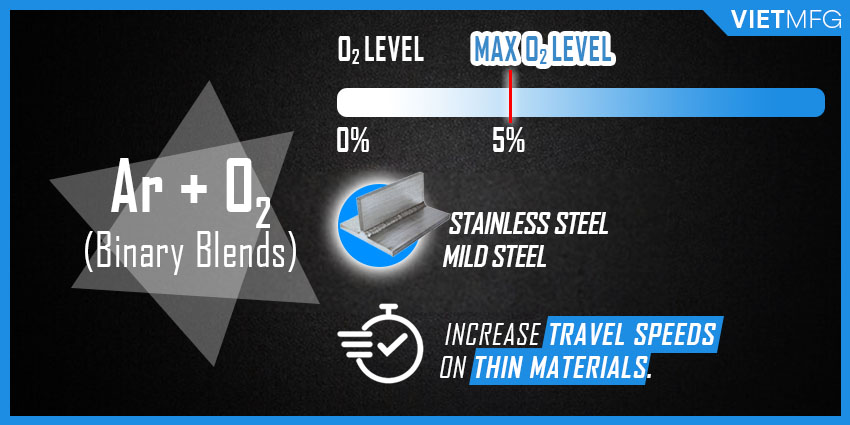
Here are top 3 mixtures of Argon and Oxygen:
- 99% Argon + 1% Oxygen: This is mainly applied for MIG stainless steel projects. However, it produces a greyish appearance on your stainless.
- 98% Argon + 2% Oxygen: This can be used for both MIG mild steel and stainless steel applications. But, this mixture creates a dull grey appearance on your stainless pieces.
- 95% Argon + 5% Oxygen: This is generally used with axial spray or pulsed spray mode of metal transfer. It is good for thicker parts of mild steel. However, due to high levels of Oxygen, the base metal must be free of contaminants to avoid oxidation.
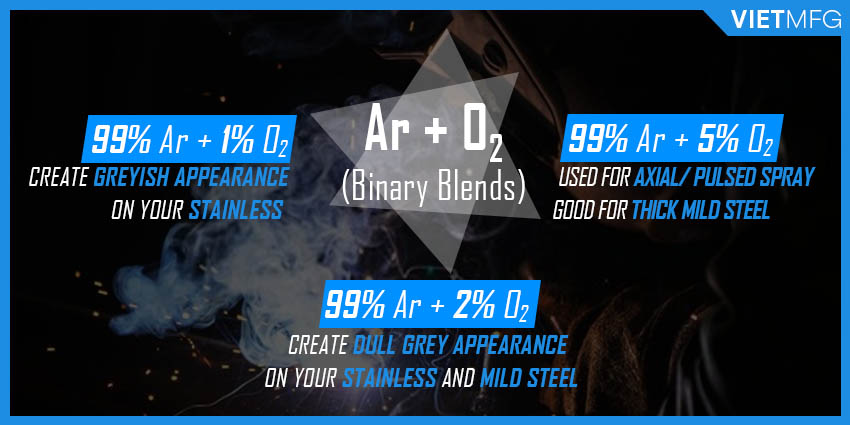
4. Three-part MIG Shielding Gas Mixture (Ternary Gas Mixture)
Three-part MIG Shielding Gas Mixture, also known as Ternary Gas Mixture, comprises at least 3 different gases, one of which is inert (for example, Argon).
Ternary gas mixtures are very popular for MIG welding of stainless steel, carbon steel and even nickel alloys.
Here are top 4 ternary gas mixture that you can find at various shops:
- 90% Helium + 7.5% Argon + 2.5% CO2: This mixture is perfect for short circuit transfer mode on MIG welding stainless steel projects. The high level of Helium provides excellent fusion and travel speed. Besides short circuit mode, it is also employed in pulsed spray mode for stainless and nickel materials with thickness larger than 1.6 mm.
- 55% Helium + 42.5% Argon + 2.5% CO2: This mixture supplies a cooler arc, which is suitable for pulsed spray transfer mode. It can also be used for short circuit and axial spray transfer mode.
- 38% Helium + 65% Argon + 7% CO2: This mixture allows for broader penetration pattern, and is a good choice for short circuit transfer in MIG welding of mild steel.
- 90% Argon + 8% CO2 + 2% O2: This mixture greatly reduces spatter (due to high level of inert gas). It works well with short circuit, pulsed spray and axial spray transfer modes, for MIG welding on mild steel projects.
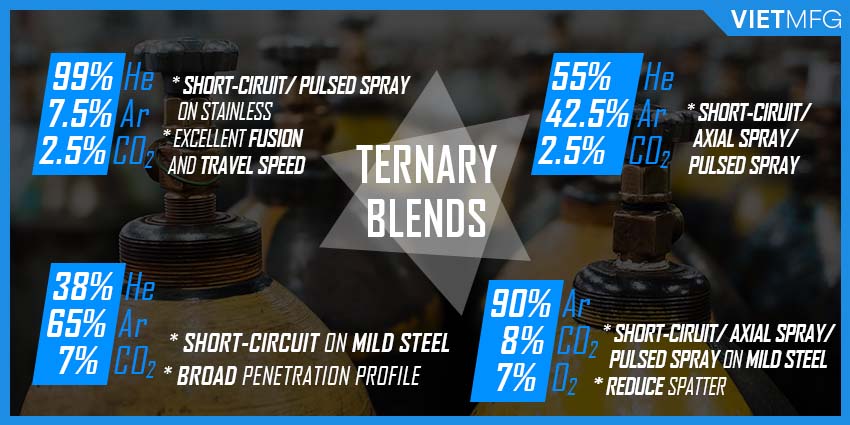
Optimal Flow Rate for your MIG Welding Gas
The optimal flow rate for MIG welding gas depends on 4 main factors:
- Weld geometry: Flat surfaces will demand higher gas flow than bumpy materials, as gas spreads out more.
- Travel speed: MIG welding at higher speed simply requires more gas to shield the weld pool.
- Electrical current setting: Higher current settings need more volume of shielding gas, especially Helium, in order to fully cover the weld pool.
- Mode of metal transfer for MIG welding: The 4 main variations of MIG welding have different requirements for shielding gas flow. Short circuit and pulsed spray modes need approximately 20 ft3/h. Globular transfer demands about 30 ft3/h, while spray transfer works well with over 40 ft3/h.
Foundation Guide on MIG Shielding Gas Selection
As mentioned earlier, the choice of MIG Shielding Gas depends on as many as 10 different factors.
The selection of shielding gas is also one crucial step in setting up MIG Welding Correct Parameters.
Thus, this is an important, yet complicated decision to make.
We have compiled a table below, which hopefully will reduce the complexity and help you make a decision faster.
Base Material | Electrode Type | Metal Transfer Mode | MIG Shielding Gas Selection |
Carbon Steel | ER70S-3 ER70S-4 ER70S-6 E70C-6M | GMAW-S or STT | 100% CO2 75-90% Argon + 10-25% CO2 |
Axial Spray or GMAW-P | 82-98% Argon + 2-18% CO2 95-98% Argon + 2-5% O2 90% Argon + 8% CO2 + 2% O2 | ||
Low Alloy Steel | ER80S-Ni1 ER80S-D2 ER100S-G ER110S-G E90C-G E110C-G | GMAW-S or STT | 100% CO2 75-80% Argon + 20-25% CO2 |
Axial Spray or GMAW-P | 95% Argon + 5% CO2 95-98% Argon + 2-5% O2 | ||
Aluminum | ER1100 ER4043, ER4047 ER5183, ER5356 ER5554, ER5556 | Axial Spray or GMAW-P (No GMAW-S) | 100% Argon 75% Helium + 25% Argon 75% Argon + 25% Helium 100% Helium |
Austenitic Stainless Steel | ER308LSi ER309LSi ER316LSi | GMAW-S or STT | 98-99% Argon + 1-2% O2 90% Helium + 7.5% CO2 + 2.5% O2 55% Helium + 42.5% Argon + 2.5% CO2 |
Axial Spray or GMAW-P | 98-99% Argon + 1-2% O2 98% Argon + 2% CO2 97-99% Argon + 1-3% H2 55% Helium + 42.5% Argon + 2.5% CO2 | ||
Nickel Alloys | ERNi-Cr3 ERNiCrMo-4 ERNiCrMo-3 ERNiCrMo-10 ERNiCrMo-14 ERNiCrMo-17 | GMAW-S or STT | 90% Helium + 7.5% Argon + 2.5% CO2 75% Helium + 25% Argon 75% Argon + 25% Helium |
Axial Spray or GMAW-P | 100% Argon 75% Helium + 25% Argon 75% Argon + 25% Helium 97-99% Argon + 1-3% H2 | ||
Duplex Stainless Steel | 2209 2304 | GMAW-S or STT | 90% Helium + 7.5% Argon + 2.5% CO2 98-99% Argon + 1-2% O2 98% Argon + 2% CO2 |
Axial Spray or GMAW-P | 75% Helium + 25% Argon 75% Argon + 25% Helium 100% Argon 100% Helium | ||
90/10 Copper Nickel Alloys | ERCuNi Type 70/30 | Axial Spray or GMAW-P (No GMAW-S) | 100% Argon 75% Helium + 25% Argon 75% Argon + 25% Helium |
Copper Alloys | ERCu (Deoxidized) | Axial Spray or GMAW-P | 100% Argon 75% Helium + 25% Argon 75% Argon + 25% Helium |
Silicon Bronze and Brasses | ERCuSi | GMAW-S or STT Axial Spray or GMAW-P | 100% Argon |
Aluminum Bronze | ERCuAl-A1 ERCuAl-A2 ERCuAl-A3 | Axial Spray or GMAW-P Limited GMAW-S | 100% Argon |
Conclusion
This is the end of all basics about MIG Shielding Gas and how to choose for your project a suitable one.
After reading this article, we hope you understand about those factors that influence your MIG gas selection, main properties of the shielding gas and certain gas/ gas mixture types.
Reference
- Welding Principles and Practices (5th Edition) – McGraw Hill Education. Edward R.Bohnart. [2017]
- Gas Metal Arc Welding: Product and Procedure Selection – Lincoln Electric. [2014]
- Gas Metal Arc Welding. Wikipedia. Retrieved September 28th 2020.
- How to Wire Feed Weld. Welding Headquarters. Retrieved September 28th 2020.
- MIG Welding Shielding Gas Basics. Bernard. Retrieved September 28th 2020.
- The Fundamentals of MIG Welding Gases. American Torch Tip. Retrieved September 28th 2020.
- MIG Welding Gases. GoWelding. Retrieved September 28th 2020.