Welcome all of you to our exciting introductory course about MIG Welding Stainless Steel.
In this course, we prioritize simplicity, so even a beginner can get what MIG welding with this attractive metal is all about.
After finishing this introductory course, you will learn about:
- What to prepare for MIG Welding Stainless Steel.
- Certain tips and tricks for enhancement of MIG Welding Stainless Steel.
Ready to grab some knowledge? Let’s go!
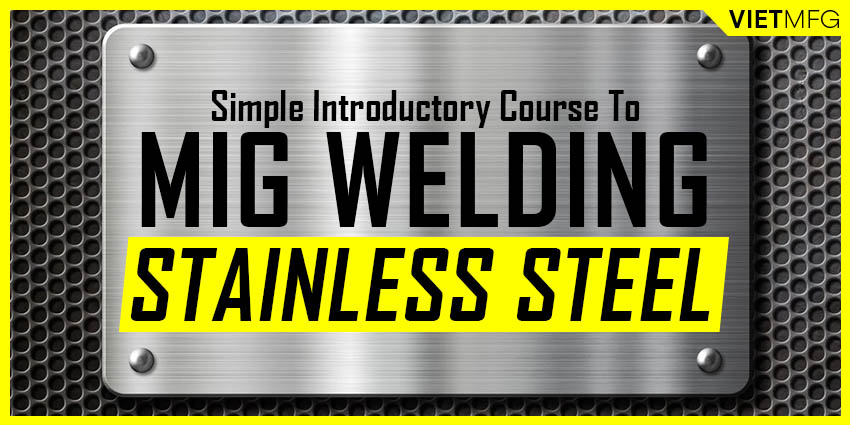
Shielding Gas Selection for MIG Welding Stainless Steel
MIG Gas Selection includes 3 options for MIG Welding Stainless Steel
- The ternary gas mixture of 90% Helium + 7.5% Argon + 2.5% CO2.
- The binary gas mixture of 98% Argon + 2% O2.
- The binary gas mixture of or 98% Argon + 2% CO2.
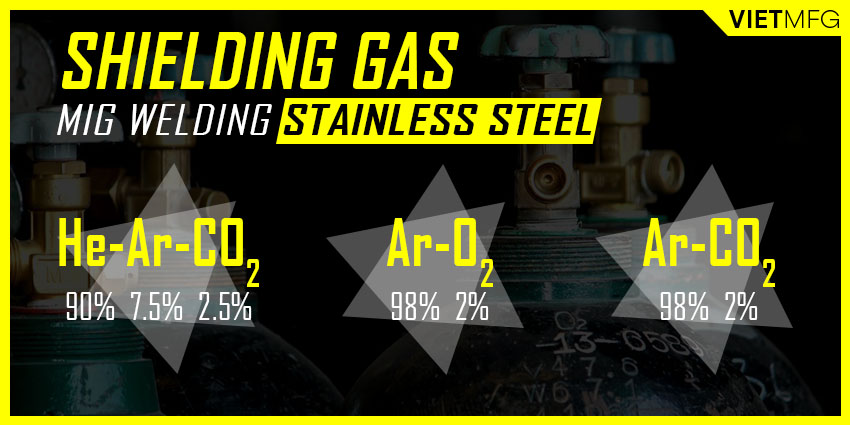
1. Ternary Gas Mixture of 90% Helium + 7.5% Argon + 2.5% CO2
The tri-mix of 90% Helium + 7.5% Argon + 2.5% CO2 is the BEST gas mixture for MIG Welding Stainless Steel.
This tri-mix blend is widely used for short-circuiting transfer, in all welding positions.
The Carbon Dioxide content is kept low to assure good corrosion resistance for stainless steel (as it will not oxidize high alloy content in the metal, such as chrome, etc.)
The Argon and Carbon Dioxide additions provide good arc stability and depth of fusion.
The high Helium content provides significant heat input to overcome the sluggish nature of the stainless steel weld puddle.
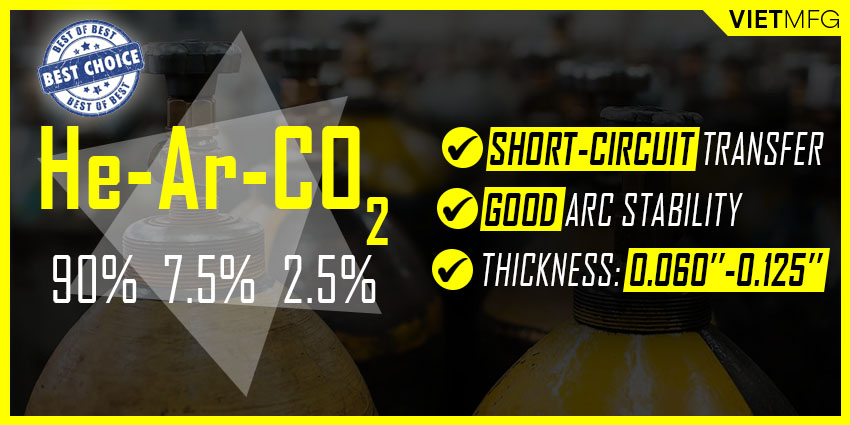
High inductance setting in the power supply also works fine with this gas blend.
This gas blend can be employed for stainless steel with thickness from 0.060 inch to 0.125 inch.
2. Binary Gas Mixture of 98% Argon + 2% O2
Another option of gas blend is the binary mixture of 98% Argon + 2% O2.
This blend is used for spray arc MIG Welding Stainless Steel.
It provides greater wetting action than the 1% O2 mixture.
Weld mechanical properties and corrosion resistance of the 1% O2 mixture and 2% O2 mixture are pretty much the same.
However, bead appearance will be darker and more oxidized for the 2% mixture with stainless steels.
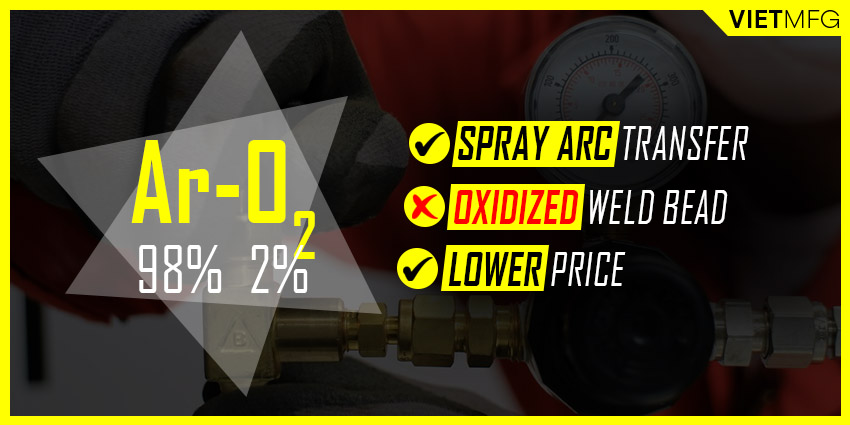
Compared to the tri-max mixture, this binary gas blend creates a colder weld.
But, thanks to its lower price, this gas mixture is also preferred.
3. Binary Gas Mixture of 98% Argon + 2% CO2
One more shielding gas option for MIG Welding Stainless Steel is the binary mixture of 98% Argon + 2% CO2.
Increasing the CO2 content will increase weld penetration and bead wetting characteristics.
At higher current levels and CO2 content, increased spatter may result.
This gas mixture can be used to join a wide range of material thickness, while utilizing a variety of modes of metal transfer.
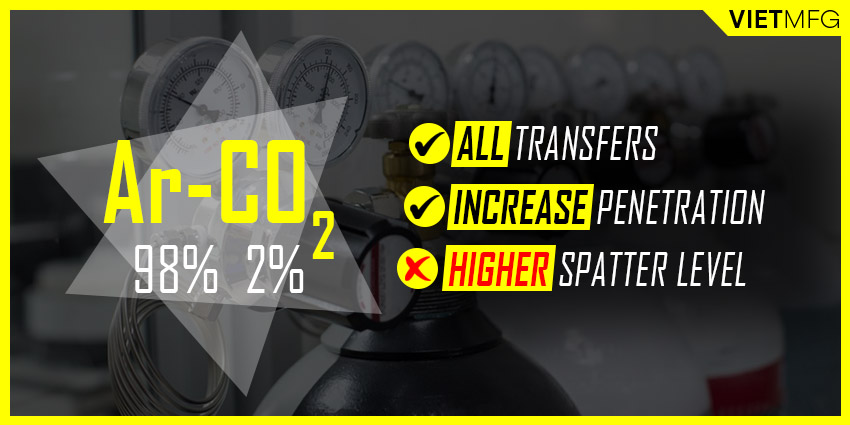
4. Restricted Shielding Gas to use for MIG Welding Stainless Steel
Do NOT employ a pure inert shielding gas for MIG Welding Stainless Steel, such as Pure Helium or Pure Argon.
These pure options are only applicable for TIG Welding only.
Moreover, do NOT use Pure CO2 or the binary blend of 75% Argon + 25% CO2 for MIG Welding Stainless Steel as well.
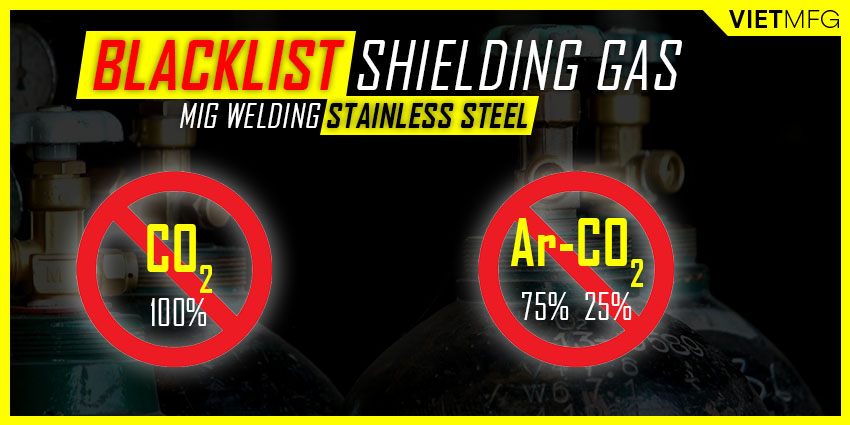
Both carbon and oxygen from such shielding gas would react with the stainless steel under a high heat environment, which leads to a reduction in corrosion resistance.
The maximum level for carbon dioxide in a shielding gas blend for stainless steel is 5%.
MIG Wire Selection for MIG Welding Stainless Steel
1. MIG Wire Material
For a suitable MIG Welding Wire Selection, you need to know what type of stainless steel you are welding.
The main principle is to match your wire material with that stainless steel type.
You can refer to the annex at the end of this article for an overall guide on how to select your wire for MIG Welding Stainless Steel.
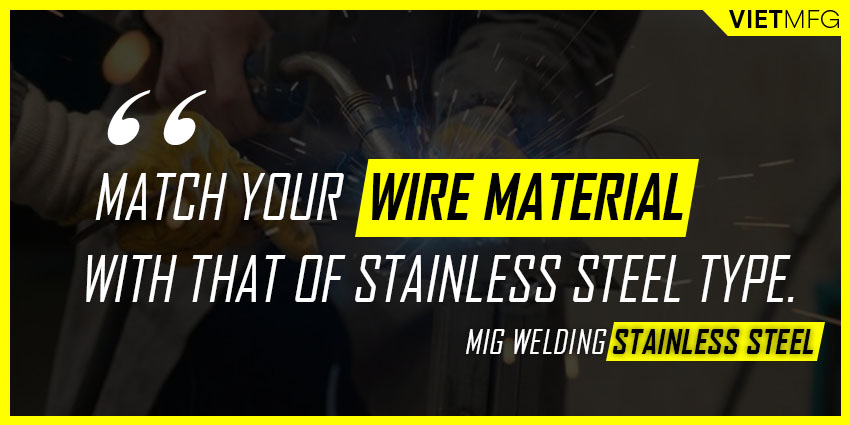
But for now, we would like to give out some examples, to show you that this selection process can be very tricky.
- If your base metal is 316L stainless steel, you can select the ER316L wire. This is the simple case: just match the base material number of your wire with that of your workpiece.
- However, if your base metal is now 304 stainless steel (which is the most popular one), things get trickier, as there is no 304 filler metal. In this case, you should use ER308 wire type. Although it has a small difference in its chemistry, this wire type still allows the filler metal to be deposited into the puddle without cracking.
- Another example is the 2205 duplex stainless steel whose chemistry contains some nickel. In this case, you should use ER2209 filler wire, as it produces a weld with almost the same level of ferrite and austenite as the base stainless steel.
- For MIG Welding of Martensitic stainless steel, 410 is the typical filler metal selection.
- If you are joining 304L stainless steel with carbon steel, use ER309L filler wire. It is a great option for MIG welding dissimilar metals under high heat.
- However, if you are not sure what your base stainless steel is, you can choose a safe option such as the ER312 filler electrode. This filler wire provides high strength and corrosion resistance to the weld. However, it is very costly, about 3-4 times more expensive than standard filler wires.
2. MIG Wire Size
The size (diameter) of MIG wire should range from 0.030 inch to 3/32 inch (0.8 – 2.4 mm).
Among those sizes, wire diameters of 0.035 inch and 0.045 inch (0.9 mm and 1.1 mm) are widely used for pulsed spray transfer.
While a very large wire diameter of 3/32 inch is suitable for axial spray transfer.
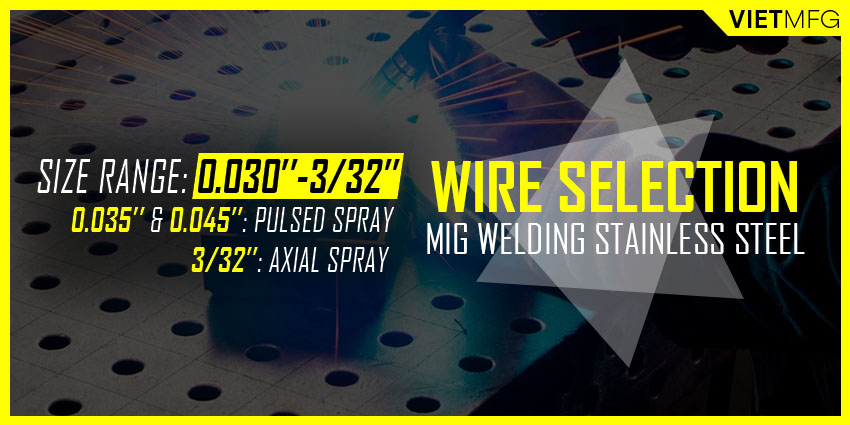
Recommended Welder Setup for MIG Welding Stainless Steel
The 2 tables below summarize the MIG Welding Correct Parameters setup for MIG Welding Stainless Steel for short-circuit and spray arc transfer respectively, based on the base metal thickness.
Table 1 – Recommended welder setup for MIG Welding Stainless Steel (Short-circuit Transfer).
Base Metal Thickness | Wire Diameter | Wire Feed Speed Setup | Voltage Setup (*) | Amperage Setup | |
gauge/ inch | mm | mm | ipm | volt | ampere |
18 | 1.2 | 0.9 | 120 – 150 | 19 – 20 | 50 – 60 |
16 | 1.6 | 0.9 | 180 – 205 | 19 – 20 | 70 – 80 |
14 | 2.0 | 0.9 | 230 – 275 | 20 – 21 | 90 – 110 |
12 | 2.6 | 0.9 | 300 – 325 | 20 – 21 | 120 – 130 |
3/16’’ | 4.8 | 0.9 | 350 – 375 | 20 – 21 | 140 – 150 |
1/4’’ | 6.4 | 0.9 | 400 – 425 | 20 – 21 | 160 – 170 |
5/16’’ | 7.9 | 0.9 | 450 – 475 | 21 – 22 | 180 – 190 |
3/8’’ | 9.5 | Not Recommended | |||
1/2’’+ | 12.7+ | Not Recommended |
(*): 90% Helium + 7.5% Argon + 2.5% CO2 as shielding gas
Table 2 – Recommended welder setup for MIG Welding Stainless Steel (Spray Arc Transfer).
Base Metal Thickness | Wire Diameter | Wire Feed Speed Setup | Voltage Setup (**) | Amperage Setup | |
inch | mm | mm | ipm | volt | ampere |
18 | 1.2 | Not Recommended | |||
16 | 1.6 | Not Recommended | |||
14 | 2.0 | Not Recommended | |||
12 | 2.6 | Not Recommended | |||
3/16’’ | 4.8 | 0.9 | 400 – 425 | 23 – 24 | 160 – 170 |
1/4’’ | 6.4 | 0.9 | 450 – 475 | 24 – 25 | 180 – 190 |
5/16’’ | 7.9 | 1.1 | 250 – 300 | 24 – 25 | 200 – 210 |
3/8’’ | 9.5 | 1.6 | 140 – 170 | 25 – 26 | 250 – 275 |
7/16’’ | 11.1 | 1.6 | 170 – 200 | 26 – 27 | 275 – 300 |
1/2’’+ | 12.7+ | 1.6 | 200 – 230 | 27 – 32 | 300 – 325 |
(**): 98% Argon + 2% O2 as shielding gas
Some Tips and Tricks for MIG Welding Stainless Steel
1. Use appropriate MIG Welding Technique
You should employ the proper technique based on the joint type.
- For fillet welds, using backhand technique is more beneficial.
- For butt welds, forehand welding is suitable.
- For outside corner welds, performing a straight motion of MIG welding is recommended.
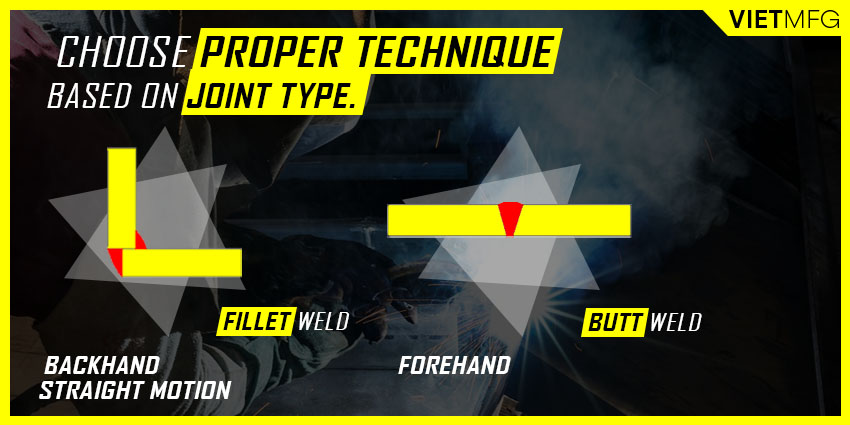
Moreover, along the axis of your joint, you should do a slight backward and forward motion.
If your MIG Welding Stainless Steel is carried out with a semi-automatic gun, forehand technique is more preferred.
Your technique is also influenced by the material thickness:
- For thicker base metal (over 1/4 inch of thickness), you should move the gun back and forth in the direction of the joint, while at the same time, perform a side-to-side movement.
- On thinner base metal, only back and forth motion along the joint is applied.
2. Use copper backup on your workpiece
Copper backup plates are great ways for MIG Welding Stainless Steel with high thickness (up to 1/16 inch).
These copper bars are often attached on the back of your stainless steel workpiece to increase its whole mass.
They are also applicable for stainless pieces over 1/4 inch in thickness.
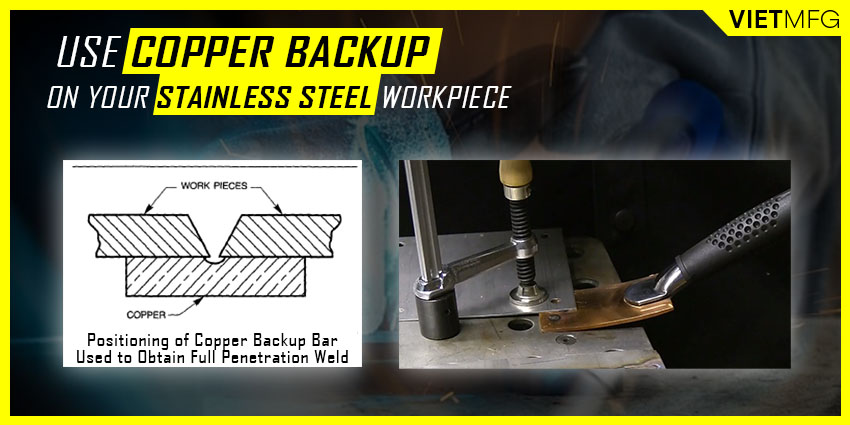
3. Hold your workpiece securely during MIG Welding
To prevent your stainless steel piece from slipping during your MIG welding session, which could ruin your joint angle, you should hold the workpiece securely.
One way to do it is to use wooden blocks to brace everything tightly.
4. Clean your weld joint
The use of filler wire for MIG Welding Stainless Steel can cause spatter, even if your filler wire is of high quality.
This spatter can become sharps on the weld joints, which can injure people handling the final products.
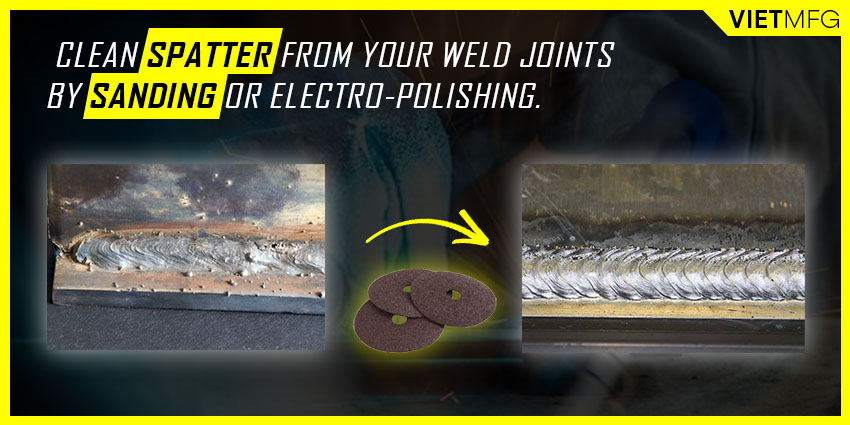
Thus, it is recommended to clean your weld joint by sanding or electro-polishing it to remove these spatters or sharps completely.
5. Use tools dedicated only for stainless steel
When dealing with stainless steel, it is a must to use a separate set of tools (like hammers, clamps and brushes) only for this material.
Do not use a carbon steel brush to clean stainless steel.
Why?
Because the amount of carbon steel adhered to the tools can jump into stainless steel, causing them to rust.
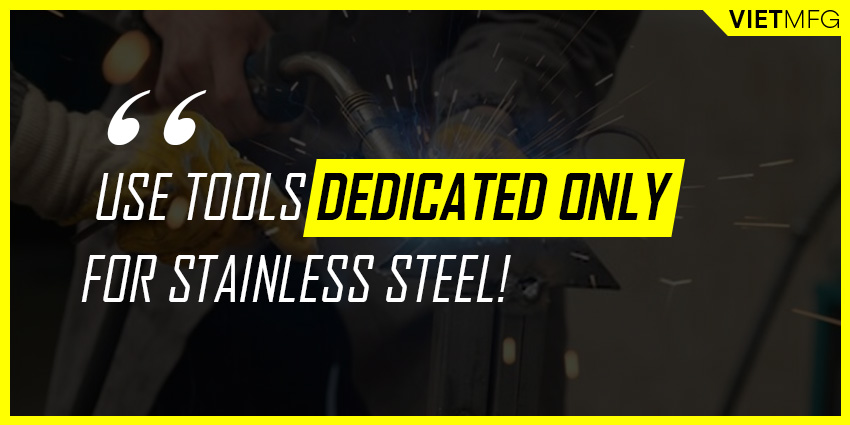
6. Monitor the temperature for both the base metal and weld metal
Monitor closely the temperature for both the base metal and weld metal to make sure you stay within the specified temperature ranges.
Otherwise, you would experience performance problems.
You can monitor the temperature by one of the following tools:
- Temperature-indicating sticks: can accurately measure the temperature and record for a long time. However, different sticks are designed for limited temperature ranges only.
- Electronic infrared thermometers: can sense the stainless steel’s surface temperature quickly, even from a distance. However, shiny surfaces and other light-related issues can lead to false results.
- Surface temperature probes: are available in different lengths that allow you to touch the metal for a measure. These probes are often mounted on the workpiece for continuous temperature monitoring. They can even print graphs of metal temperature throughout the welding session.
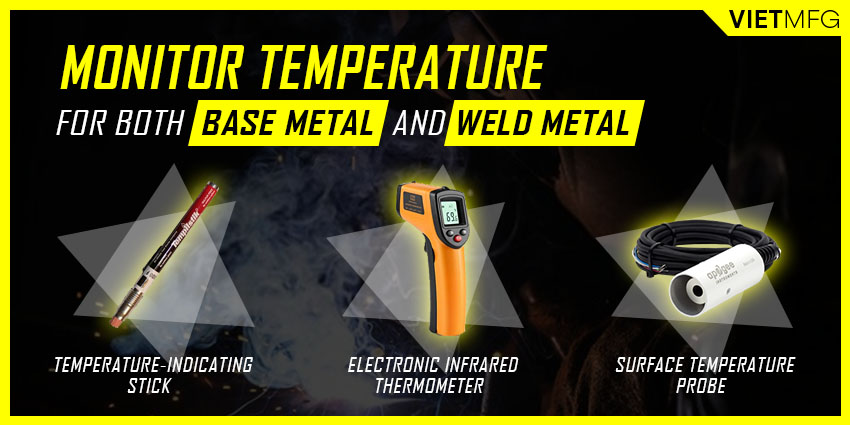
Dictionary on the Selection of Electrode Wire for MIG Welding Stainless Steel
This section serves as a dictionary (or an annex) that you can always refer to whenever you have hard time selecting a proper electrode wire for your MIG Stainless Steel projects.
This dictionary-like section is divided into 03 tables for 03 types of stainless steel.
1. MIG Wire for Welding Austenitic Stainless Steels
Base Stainless Steel | Recommended Stainless Steel MIG Wire |
201, 202 | ER209, ER219, ER308, ER308S |
205 | ER240 |
216 | ER209 |
301, 302 | ER308, ER308S, ER308LSi |
304 | ER308, ER308S, ER308LSi, ER309, ER309S, ER309LSi |
304H, 304HN | ER308H |
304L, 304LN | ER308L, ER308LS, ER347, ER308LSi |
304N, 305, 308 | ER308, ER308S, ER308LSi, ER309, ER309S, ER309LSi |
308L | ER308L, ER308LS, ER308LSi, ER347 |
309 | ER309, ER309S, ER309LSi, ER310 |
309S | ER309L, ER309LS, ER309LSi |
310, 310S, 314 | ER310 |
312 | ER312 |
316 | ER316, ER308Mo |
316H | ER316H, ER16-8-2 |
316L | ER316L, ER316LSi, ER308MoL |
316LN | ER316L, ER316LSi |
316N | ER316 |
317 | ER317 |
317L | ER317L |
321, 321H | ER321 |
329 | ER312 |
330, 330HC, 332 | ER330 |
347, 347H, 348, 348H | ER347, ER347Si |
Nitronic 33 | ER240 |
Nitronic 40 | ER219 |
Nitronic 50 | ER209 |
Nitronic 60 | ER218 |
254SMo | ERNiCrMo-3 |
AL-6XN | ERNiCrMo-10 |
Source: AWS Filler Metal Specifications: A5.4, A5.9, A5.22
2. MIG Wire for Welding Ferritic Stainless Steels
Base Stainless Steel | Recommended Stainless Steel MIG Wire |
405 | ER410NiMo, ER430 |
409 | ER409, AM363, EC409 |
429 | ER409Cb |
430, 430F, 430FSe | ER430 |
434 | ER434 |
442 | ER442 |
444 | ER316L |
446 | ER446 |
26-1 | ER26-1 |
Source: AWS Filler Metal Specifications: A5.4, A5.9, A5.22
3. MIG Wire for Welding Martensitic and Duplex Stainless Steels
Base Stainless Steel | Recommended Stainless Steel MIG Wire |
403, 414, 431 | ER410 |
410 | ER410, ER410NiMo |
410S | ER410NiMo |
416 | ER312, ER410 |
416Se, 416PlusX, 420F | ER312 |
420 | ER420, ER410 |
440A, 440B, 440C | Not recommended for Arc Welding |
2205, 2304 | ER2209 |
255 | ER2553 |
Source: AWS Filler Metal Specifications: A5.4, A5.9, A5.22
Conclusion
This is the end of our introductory course to MIG Welding Stainless Steel.
We hope this article can assist you on your MIG Welding with this particular material.
Reference
- Welding Principles and Practices (5th Edition) – McGraw Hill Education. Edward R.Bohnart. [2017]
- Gas Metal Arc Welding: Product and Procedure Selection – Lincoln Electric. [2014]
- MIG Welding Gases. GoWelding. Retrieved September 28th 2020.
- Stainless Steel MIG Welding with Compact Welders. Lincoln Electric. Retrieved September 30th 2020.
- How to MIG Weld Stainless Steel. Marlin Wire. Retrieved September 30th 2020.
- Stainless Steel MIG Welding Tips | MIG Monday. Youtube (Weld.com channel). Retrieved September 30th 2020.
- Basic Tips for MIG Welding Stainless Steel: Part 1 | MIG Monday. Youtube (Weld.com channel). Retrieved September 30th 2020.