MIG Welding Mild Steel is an interesting topic but has limited detailed materials.
This article will provide you with simple and accurate content about how to perform MIG Welding on Mild Steel.
Specifically, we will go over:
- What to prepare for MIG Welding Mild Steel.
- Certain tips and tricks for enhancement of MIG Welding Mild Steel.
Without further ado, let’s start now!
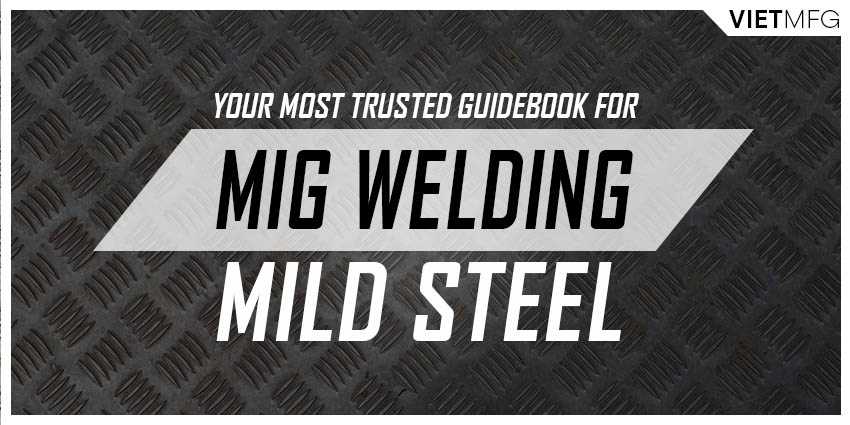
Shielding Gas Selection for MIG Welding Mild Steel
MIG Gas Selection includes 2 preferred options for MIG Welding Mild Steel.
- The binary gas mixture of 75% Argon + 25% CO2 (also known as C25).
- Pure CO2.
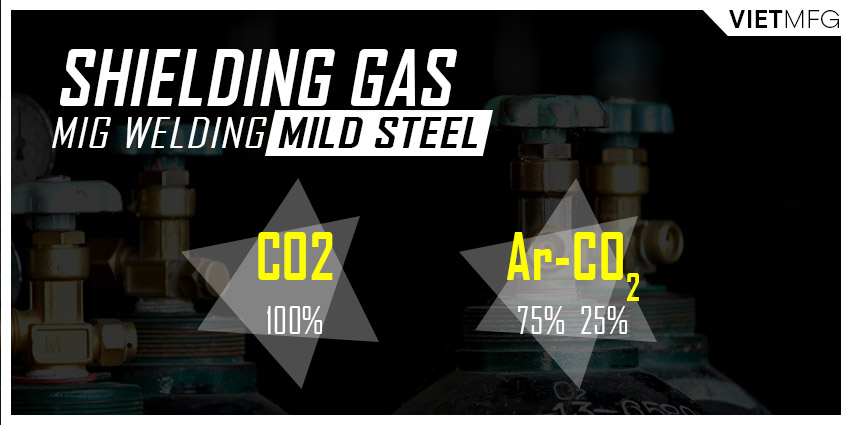
1. Binary gas mixture of 75% Argon + 25% CO2
Benefits of 75% Argon + 25% CO2 Mixture
The gas mixture of 75% Argon + 25% CO2 is suitable for all purposes of MIG Welding Mild Steel.
It creates the minimum spatter level and the best bead appearance.
Moreover, this C25 mixture enhances your travel speeds and does not promote burn-through on thinner sheets of mild steel.
Also, this gas mixture is widely available, as you can find it at any local welder supply store.
Limitations of 75% Argon + 25% CO2 Mixture
One limitation of this gas mixture is that it is quite costly, due to the existence of Argon in the mixture.
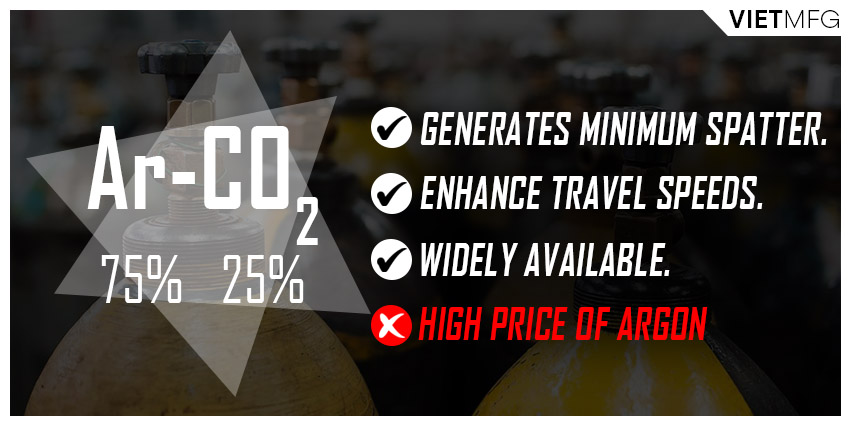
2. Pure CO2
Benefits of Pure CO2
Compared to the binary gas mixture above, Pure CO2 provides a deeper penetration profile, as the CO2 reacts with the arc and generates a hotter weld puddle.
This shielding gas option is also much more affordable than the first binary blend, as it contains no Argon at all.
Pure CO2 is also widely available at all welding supply stores.
Moreover, when you purchase a CO2 tank, you receive more gas volume in the cylinder, compared to the binary mix.
Limitations of Pure CO2
When employing Pure CO2 as shielding gas, the electrical arc is not stable.
Thus, the arc pops more and creates an excessive level of spatter.
Higher spatter level means higher cleanup cost as well.
This is why Pure CO2 should not be applied for welding thinner metal at low amperage, as it can dig holes in the metal sheet.
It also generates a considerable amount of fumes as you perform your MIG Welding projects.
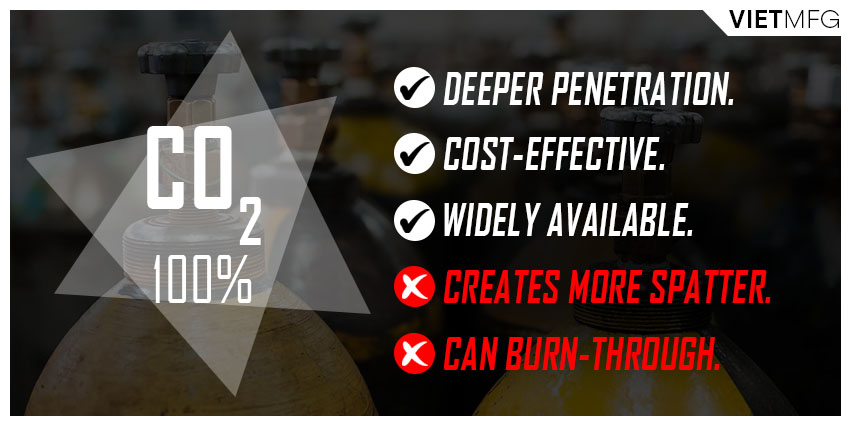
MIG Welding Wire Selection for MIG Welding Mild Steel
1. MIG Wire Material
For MIG Welding Mild Steel, there are 2 preferred options for wire electrode: ER70S-3 and ER70S-6.
- For ER70S-3, it contains medium levels of manganese and silicon. It can be applied for MIG Welding Mild Steel for all purposes.
- For ER70S-6, it should be used when more deoxidizers are required for the welding process.
Besides those top two candidates, there are also other filler wire options that can be applied in special projects:
ER70S-2: This filler wire contains high silicon and manganese contents, as well as deoxidizers (aluminum, zirconium, titanium). It is dedicated for use on mild steel with medium levels of millscale.
ER70S-4: This filler wire has higher contents of silicon and manganese than ER70S-3. It is designed for use in projects that require a higher doxidizer level.
ER70S-7: This filler wire has higher manganese levels than an ER70S-6 wire, but contains lower silicon levels. It can be used with a binary gas mix of Argon and CO2.
ER70S-G: The letter “G” in its name indicates that the filler wire belongs to the general category of AWS classification.
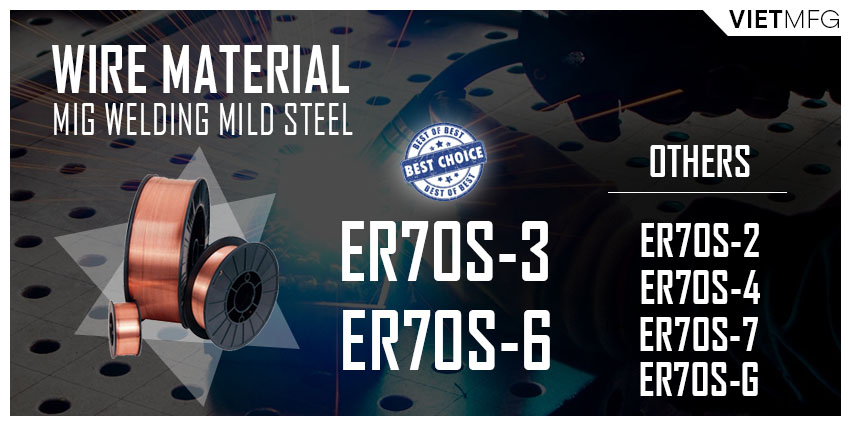
2. MIG Wire Size
About wire size, 0.030 inch (8 mm) diameter is the ultimate choice for all MIG Welding applications of Mild Steel at various metal thicknesses.
However, to MIG weld thinner mild steel, it is recommended to pic 0.023 inch (0.6 mm) diameter to reduce heat input.
And for MIG welding thicker mild steel, select 0.035 inch (0.9 mm) or even 0.045 inch (1.1 mm) inch diameters if they are within your output range.
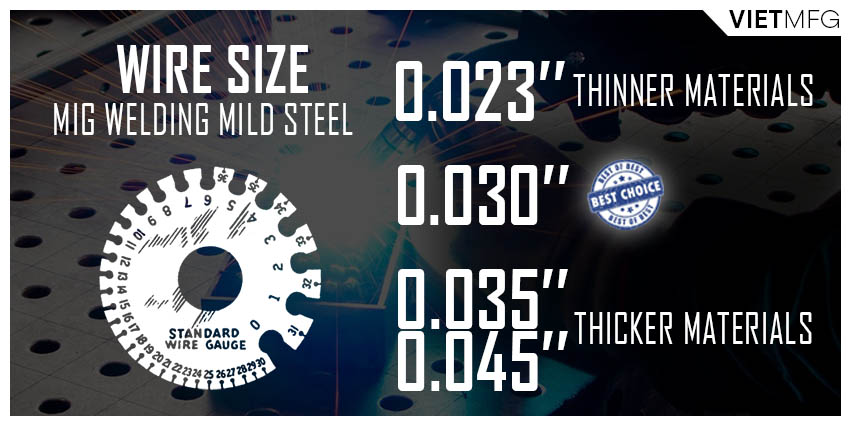
Recommended Welder Setup for MIG Welding Mild Steel
The 2 tables below summarize the correct setup for MIG Welding Mild Steel under two most common metal transfer modes (short-circuit and spray arc transfer), based on the base metal thickness.
Table 1 – Recommended welder setup for MIG Welding Mild Steel (Short-circuit Transfer).
Base Metal Thickness | Wire Diameter | Wire Feed Speed Setup | Voltage Setup | Amperage Setup | |
gauge/ inch | mm | mm | ipm | volt | ampere |
22 | 0.8 | 0.8 | 90 – 100 | 15 – 16 (*) 16 – 17 (**) | 40 – 55 |
20 | 0.9 | 0.8 0.9 | 120 – 135 105 – 115 | 17 – 18 (*) 15 – 16 (**) | 50 – 60 |
18 | 1.2 | 0.8 0.9 1.1 | 150 – 175 140 – 160 70 | 18 – 19 (*) 16 – 17 (**) | 70 – 80 |
16 | 1.6 | 0.8 0.9 1.1 | 220 – 250 180 – 220 90 – 110 | 19 – 20 (*) 17 – 18 (**) | 90 – 110 |
14 | 2.0 | 0.8 0.9 1.1 | 250 – 340 240 – 260 120 – 130 | 20 – 21 (*) 17 – 18 (**) | 120 – 130 |
1/8’’ | 3.2 | 0.9 1.1 | 280 – 300 140 – 150 | 21 – 22 (*) 18 – 19 (**) | 140 – 150 |
3/16’’ | 4.8 | 0.9 1.1 | 320 – 340 160 – 175 | 21 – 22 (*) 18 – 19 (**) | 160 – 170 |
1/4’’ | 6.4 | 0.9 1.1 | 360 – 380 185 – 195 | 23 – 24 (*) 21 – 22 (**) | 180 – 190 |
5/16’’ | 7.9 | 0.9 1.1 | 400 – 420 210 – 220 | 23 – 24 (*) 21 – 22 (**) | 200 – 210 |
3/8’’ | 9.5 | 0.9 1.1 | 420 – 520 220 – 270 | 24 – 25 (*) 23 – 24 (*) | 220 – 250 |
1/2’’+ | 12.7+ | Not Recommended |
(*): Pure CO2 as shielding gas.
(**): 75% Argon + 25% CO2 as shielding gas.
Table 2 – Recommended welder setup for MIG Welding Mild Steel (Spray Arc Transfer).
Base Metal Thickness | Wire Diameter | Wire Feed Speed Setup | Voltage Setup (***) | Amperage Setup | |
inch | mm | mm | ipm | volt | ampere |
22 | 0.8 | Not Recommended | |||
20 | 0.9 | Not Recommended | |||
18 | 1.2 | Not Recommended | |||
16 | 1.6 | Not Recommended | |||
14 | 2.0 | Not Recommended | |||
1/8’’ | 3.2 | 0.9 1.1 | 320 – 340 160 – 175 | 23 – 24 | 160 – 170 |
3/16’’ | 4.8 | 0.9 1.1 | 360 – 380 185 – 195 | 24 – 25 | 180 – 190 |
1/4’’ | 6.4 | 0.9 1.1 | 400 – 420 210 – 220 | 24 – 25 | 200 – 210 |
5/16’’ | 7.9 | 0.9 1.1 | 420 – 520 220 – 270 | 25 – 26 | 220 – 250 |
3/8’’ | 9.5 | 1.1 | 375 | 26 – 27 | 300 |
1/2’’+ | 12.7+ | 1.1 | 390 | 29 – 30 | 315 |
(***): 98% Argon + 2% O2 as shielding gas
Some Tips and Tricks for MIG Welding Mild Steel
1. Properly check tension applying on your MIG wire
It is important to set a proper tension on your MIG wire during the welding session.
Too much or too little tension on the MIG wire, or on the drive rolls located at the drive roll assembly, or even on the wire spool, can make it impossible to perform MIG weld.
Please check out how to set proper tension on the MIG wire at our article MIG Welding: Setting the Correct Parameters.
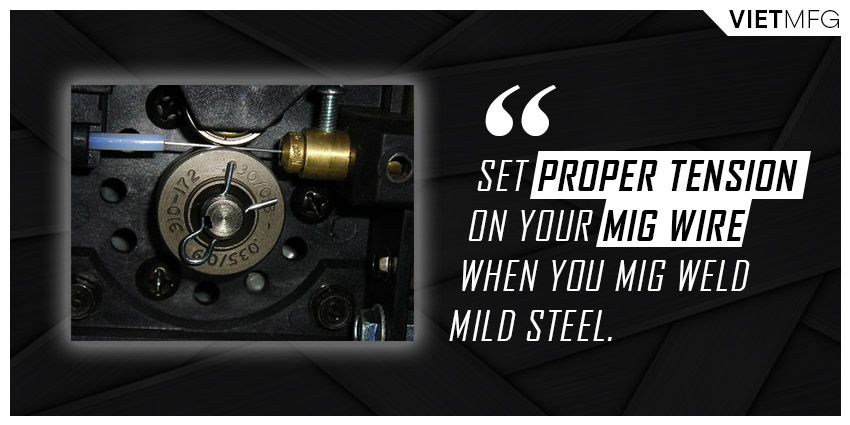
2. Carefully inspect all your gun consumables
The internal spaces of your gun consumables (MIG welding nozzle, contact tip, liners, etc.) are ideal places for spatter buildups.
These buildups cause great resistance to your MIG welding, which leads to unstable arc.
Thus, it is recommended to regularly inspect and spray your gun consumables with anti-spatter products.
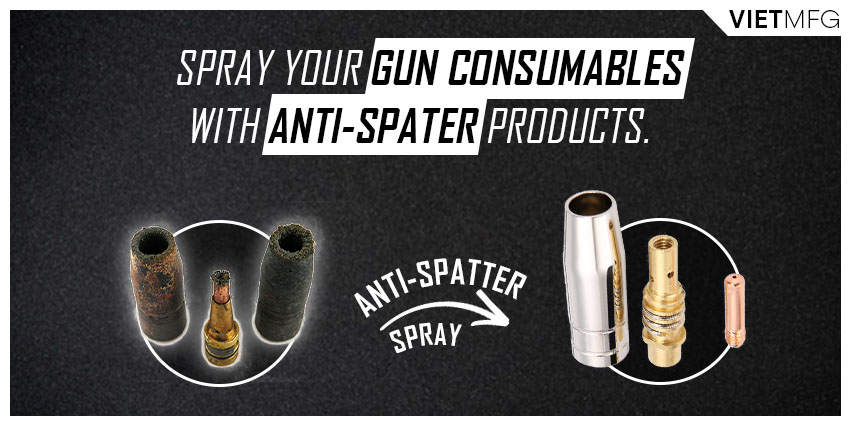
3. Travel your gun not too slow, but not too fast!
Make sure to move your MIG gun slow enough to achieve a good and hot weld.
However, do NOT go too slow, as it could concentrate heat at a single point for too long and cause it to be burnt-through.
Depending on the base material thickness that you are MIG Welding, you would like to travel your gun by 1 inch for every 10 seconds.
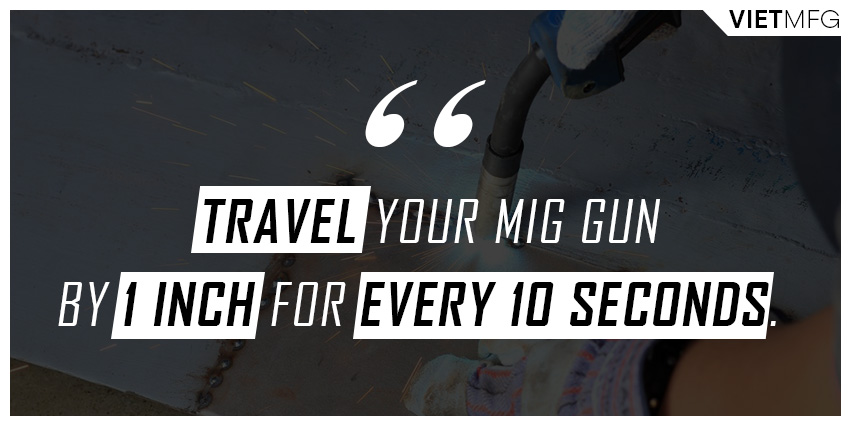
Conclusion
Those are the fundamental things about MIG Welding Mild Steel.
Believe me! Just remember the appropriate setup and enough practice, you will master the process in no time.
Reference
- Welding Principles and Practices (5th Edition) – McGraw Hill Education. Edward R.Bohnart. [2017]
- Gas Metal Arc Welding: Product and Procedure Selection – Lincoln Electric. [2014]
- MIG Welding: The Basics for Mild Steel. Miller. Retrieved October 8th 2020.
- What is the Best Gas for MIG Welding Mild Steel? Welding Headquarters. Retrieved October 8th 2020.
- MIG (Solid Core) Welding Calculator. Miller. Retrieved October 8th 2020.
- How to MIG Weld Stainless Steel to Mild Steel | MIG Monday. Youtube (Weld.com channel). Retrieved October 9th 2020.